Avoiding problems in electrohydraulic control systems design
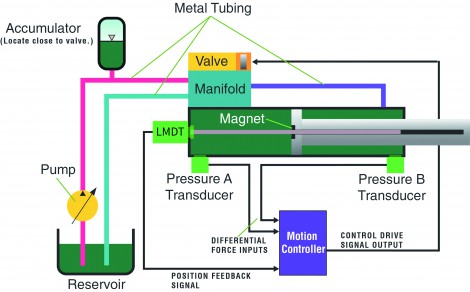
By Jacob Paso, Delta Computer Systems Inc.
Closed-loop control gives machines great precision to apply force or lift heavy objects or follow very precise motion profiles. Set up incorrectly, however, an electrohydraulic linear motion system can be unstable and cause damage to products or be dangerous to people.
The key to unlocking the benefits of electrohydraulic control is understanding system requirements, selecting the proper system components, sizing them appropriately, and correctly programming and tuning the motion controller for optimal performance.
Selecting/sizing cylinders
Building a precisely controllable motion system is all about understanding the concepts of force and natural frequency. For a typical hydraulic motion system, the acceleration and velocity are limited by the available force, not the flow. In addition, the natural frequency of a system determines the maximum acceleration rate that it can achieve under control.
Where mistakes are often made is in cylinder diameter. Cylinder choice is crucial since both the force it can apply, and the natural frequency of the system are functions of the cylinder diameter. A common error is to use small diameter cylinders that are capable of moving very quickly under light loads. Unfortunately, under higher loads, the piston in a narrow cylinder provides too little surface area for hydraulic oil flow to push on to produce the required force. A small diameter cylinder acts like a hydraulic spring, resulting in a low natural frequency, especially if the system has a large mass. This can cause oscillation if the motion profile requires quick acceleration, or if the system exhibits stiction (static friction exceeds dynamic friction).
The natural frequency of a system is related to its stiffness. Because fluid is compressible, a fluid power system with a large bore is much stiffer than a system using a long, narrow cylinder. Hence, systems with larger bore diameters will not compress as much when accelerating and are capable of quicker controlled acceleration and deceleration. As a general rule, in order to be precisely controllable by a standard PID algorithm, the natural frequency of a cylinder acting on a particular load mass should be three to four times greater than the frequency at which the system is commanded to move.
Choosing pumps and accumulators
After the cylinders are chosen, the next step is to size the hydraulic pump correctly to provide fluid flow in order to support the required cylinder speed. If the pump is too large, fluid and energy may be wasted. If the flow is too small, the system won’t perform even with the correct cylinders. The optimal flow calculation is relatively simple: The required volume of oil flow matches the required change in internal volume of the cylinder over time. Because the flow is proportional to the square of the cylinder diameter, doubling cylinder diameter requires four times the flow.
-
PPMA 2025
23 September, 2025, 9:30 - 25 September, 2025, 16:00
NEC, Birmingham UK -
Advanced Engineering Show 2025
29 October, 2025, 9:00 - 30 October, 2025, 16:00
NEC, Birmingham UK