Avoiding problems in electrohydraulic control systems design
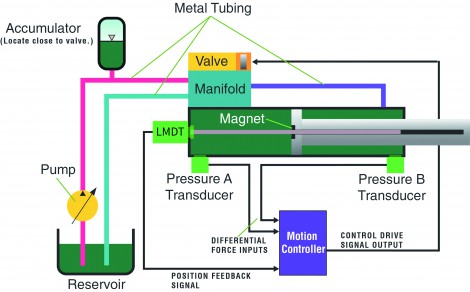
If quick motion is necessary, a feedforward component can be added that anticipates the drive required to start the motion. A good design practice is to use feedforwards to produce the bulk of the motion drive signal, with the P, I and D terms doing fine-tuning of the motion in response to smaller error factors than would occur if the PID factors were used alone. Using the PID terms in this manner focuses that part of the algorithm to respond to environmental conditions such as temperature changes that can vary from production cycle to production cycle.
But what happens if fast-changing feedback levels cause the motion controller to change its outputs too quickly, a phenomenon that could be a result of noisy transducer connections. Figure 3 shows the inclusion of an output filter between the output of the control loop and the connection to the valve. In the case of Delta Computer Systems’ motion controllers, support for output filtering is provided as a standard programming function.
Good tools help with diagnosing and fixing problems
When selecting a motion controller, designers should look for a product that is supported with tools to simplify the development and tuning of motion systems, as well as diagnostic tools that can help isolate system problems. Delta Computer Systems’ Plot Manager, a feature of the company’s RMCTools support package, can be used to monitor how the actual motion differs from target motion during an operational cycle. It was by using the Plot Manager that the engineers identified a problem with tuning the motion of the gang saw wiggle box described above.
Another Delta tool is the Tuning Wizard, which can be used to automatically generate a set of control parameter gains that will reduce the error between the target and actual motion profile (see Figure 4). Further tweaking is sometimes necessary, but the Tuning Wizard will accelerate the tuning process. In the case of the wiggle box problem, the actuator tuned up easily after changing the tuning to acceleration control using the Delta’s Tuning Wizard. The tuning process took less than 10 minutes.
By choosing the correct system components, including the right motion controller and automated tools such as these, hydraulic system designers can avoid some difficult problems and gain the full potential of hydraulic power.
-
PPMA 2025
23 September, 2025, 9:30 - 25 September, 2025, 16:00
NEC, Birmingham UK -
Advanced Engineering Show 2025
29 October, 2025, 9:00 - 30 October, 2025, 16:00
NEC, Birmingham UK