- Home » Editorial » Hydraulics
Optimising lubrication for hydraulic systems
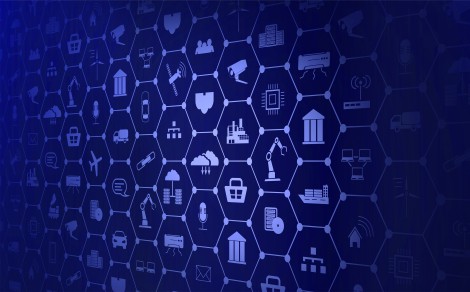
Proper hydraulic fluid maintenance ensures performance, efficiency, and longevity. Monitoring condition, controlling contamination, and maintaining lubrication prevent wear, reduce downtime, and extend machinery life. H&P reports
Hydraulic systems are at the core of many industries, driving everything from machinery in manufacturing plants to equipment
in agriculture. These systems rely on hydraulic fluid, not just for power transfer but also for lubrication. Proper lubrication is essential for the smooth operation of these systems, helping to reduce friction, prevent wear, and ensure the longevity of the
components. However, maintaining the fluid’s quality and performance over time is no simple task, and regular fluid maintenance is necessary to keep things running smoothly.
At the heart of hydraulic lubrication is the fluid itself, which acts as both a power transmitter and a lubricant for the internal components. Over time, the fluid can degrade due to heat, contamination, or chemical breakdown. This can lead to a reduction in the fluid’s ability to lubricate the system effectively, increasing friction and wear on critical components like pumps,
valves, and cylinders. This is why regular checks on the hydraulic fluid are vital to ensure the system is properly lubricated and
protected from excessive wear.
Contamination
One of the most common issues in hydraulic systems is contamination. Dust, dirt, water, and even air can make their way into the fluid, affecting its ability to lubricate the system effectively. Particles in the fluid increase friction between moving parts, leading to excessive wear and sometimes even catastrophic failure. Water contamination, in particular, can cause corrosion in metal parts and degrade the fluid’s lubrication properties. This is why contamination control is an integral part of fluid maintenance. Using high-quality filters, along with regular fluid checks, can help remove contaminants before they cause harm. In some cases, installing water-absorbing filters can prevent water from degrading the fluid or corroding the system’s components.
Viscosity is another critical factor in lubrication. Hydraulic fluid needs to maintain the right thickness to effectively lubricate moving parts and transfer power. If the fluid becomes too thick, it won’t flow smoothly through the system, causing excessive pressure and heat. If it’s too thin, it can’t provide an adequate lubricating film, leading to increased wear on components. This is why monitoring the fluid’s viscosity is a key part of lubrication maintenance. If the fluid has become too thick or thin due to age or contamination, it should be replaced or treated to restore its proper consistency.
Temperature also plays a significant role in the fluid’s ability to lubricate. As hydraulic systems operate, they generate heat, and high temperatures can cause the fluid to break down faster. This not only affects the fluid’s lubrication properties but can also lead to the formation of harmful deposits or sludge that can block filters and other components. Conversely, if the fluid becomes too cold, it can thicken and flow poorly, putting stress on the system. It’s important to monitor the temperature of the hydraulic system to ensure the fluid stays within its optimal operating range. In many cases, temperature sensors are used to provide real-time data, allowing operators to adjust the system before overheating or underperformance becomes an issue.
-
SMART Manufacturing & Engineering Week
04 - 05 June, 2025
NEC, Birmingham UK -
PPMA 2025
23 September, 2025, 9:30 - 25 September, 2025, 16:00
NEC, Birmingham UK -
Advanced Engineering Show 2025
29 October, 2025, 9:00 - 30 October, 2025, 16:00
NEC, Birmingham UK