- Home » Editorial » Hydraulics
Navigating hydraulic filtration challenges in manufacturing
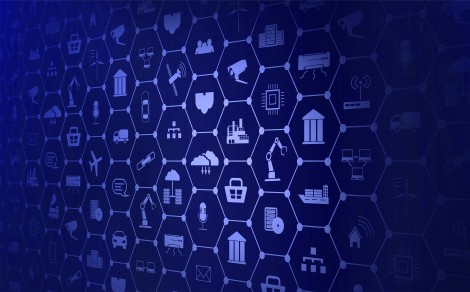
To ensure optimal performance and longevity of hydraulic systems, proper filtration is essential. Filtration serves as a frontline defence, removing contaminants and impurities that can compromise the integrity and functionality of hydraulic components. H&P delves into the significance of filtration in manufacturing, the challenges faced, and the solutions available to address them
Hydraulic systems rely on the seamless flow of hydraulic fluid to transmit power and operate machinery efficiently. However, hydraulic fluids are susceptible to contamination from various sources, including dirt, debris, moisture, and particulate matter. Without effective filtration, these contaminants can wreak havoc on hydraulic components, leading to decreased performance, increased wear and tear, and ultimately, system failure.
Filtration plays a critical role in maintaining the cleanliness and purity of hydraulic fluids by removing harmful particles and impurities. By implementing proper filtration measures, manufacturers can safeguard their hydraulic systems against damage and ensure reliable operation, thereby minimising downtime and maximising productivity.
Challenges
Despite the importance of filtration in hydraulic systems, manufacturers often encounter several challenges in implementing effective filtration strategies.
Manufacturing environments are prone to contamination from various sources, including airborne particles, dust, and debris. Contaminants can enter hydraulic systems through breather vents, reservoir openings, or during maintenance procedures, posing a significant challenge to filtration efforts.
Maintaining optimal filtration performance also requires regular monitoring and maintenance of filtration equipment, including filter elements, housings, and seals. However, due to time constraints and resource limitations, manufacturers may struggle to implement comprehensive maintenance practices, leading to compromised filtration efficiency.
In addition, selecting the right filtration equipment and components that are compatible with specific hydraulic systems can be challenging. Manufacturers must consider factors such as fluid viscosity, flow rates, pressure ratings, and system requirements when choosing filtration solutions, adding complexity to the selection process.
Navigating the challenges associated with hydraulic filtration requires thoughtful strategies and proactive measures. Manufacturers can employ various approaches to enhance filtration efficiency and safeguard their hydraulic systems against contamination.
One such approach involves implementing preventive maintenance programmes. Establishing regular inspection and maintenance schedules for filtration equipment is essential for ensuring optimal performance. This includes routine replacement of filter elements, cleaning of housings, and monitoring of filtration efficiency to prevent contamination build-up and maintain system integrity.
Investing in quality filtration equipment from reputable manufacturers is another critical strategy. Selecting high-quality filter elements, housings, and accessories that meet industry standards and specifications can help minimise downtime and reduce maintenance costs in the long run, ensuring reliability and longevity of hydraulic systems.
Incorporating multi-stage filtration systems with different filtration media and micron ratings can further enhance filtration effectiveness. By filtering out contaminants of varying sizes at different stages, manufacturers can achieve higher levels of cleanliness and extend the lifespan of hydraulic components, bolstering the resilience and efficiency of their systems.
Furthermore, educating personnel on the importance of hydraulic filtration, proper maintenance procedures, and troubleshooting techniques is vital. By providing training and fostering a culture of awareness and accountability among employees, manufacturers can empower them to identify and address filtration issues proactively, mitigating risks associated with hydraulic contamination and ensuring the reliability of their hydraulic systems.
By understanding the importance of filtration, recognising the challenges faced, and implementing proactive solutions, manufacturers can safeguard their hydraulic systems against contamination and optimise performance, ultimately driving efficiency and productivity in their operations.
-
PPMA 2025
23 September, 2025, 9:30 - 25 September, 2025, 16:00
NEC, Birmingham UK -
Advanced Engineering Show 2025
29 October, 2025, 9:00 - 30 October, 2025, 16:00
NEC, Birmingham UK