- Home » Editorial » Hydraulics
Advancements in swaging and crimping technologies
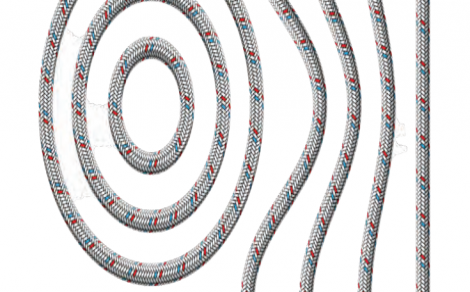
Recent developments in swaging and crimping technologies are reflecting broader trends in engineering and manufacturing, focusing on enhanced performance, greater flexibility, and improved durability. H&P reports
Swaging and crimping, though often used interchangeably, serve distinct functions in the assembly of hydraulic components. Swaging involves deforming a fitting onto a hose using a radial force, while crimping uses a compressive force to achieve a similar result. Both methods are designed to create a tight, leak-proof seal that can withstand the high pressures typically found in hydraulic systems. Recent advancements in these technologies are expanding their capabilities, overcoming previous limitations and adapting to new requirements.
One of the most significant recent developments in swaging and crimping technology is the refinement of machine automation. Modern crimping and swaging machines now feature advanced automation capabilities that enhance precision and efficiency. Automated systems can adjust parameters such as pressure and speed with remarkable accuracy, reducing the risk of human error and ensuring consistent results across large production runs. This level of automation not only improves the quality of the finished products but also speeds up the manufacturing process, meeting the growing demand for hydraulic components in various industries.
The integration of digital technology into swaging and crimping machines has brought about a new era of precision engineering. Many of the latest machines come equipped with sophisticated software that allows for real-time monitoring and adjustment. This digital interface provides operators with detailed feedback on the swaging or crimping process, enabling them to make immediate adjustments if needed. Such advancements ensure that the components meet exact specifications, which is particularly crucial in high-pressure applications where any deviation can lead to system failures or safety hazards.
Versatility
The versatility of modern swaging and crimping equipment is another important development. Recent innovations have led to the creation of machines capable of handling a wide range of hose sizes and types. This flexibility is essential in today’s diverse industrial landscape, where hydraulic systems are increasingly customised to meet specific operational requirements. Machines that can accommodate various hose dimensions and fitting styles streamline the production process and reduce the need for multiple pieces of equipment. This adaptability not only enhances manufacturing efficiency but also helps companies respond more swiftly to changing market demands.
Material advancements also play a key role in the evolution of swaging and crimping technologies. The use of highstrength materials and advanced coatings has improved the durability and longevity of hydraulic components. For instance, new types of fittings and hoses are designed to withstand harsher environmental conditions and more extreme pressure levels. These innovations contribute to the overall reliability of hydraulic systems, reducing maintenance needs and extending the lifespan of critical components.
In addition to material improvements, there is a growing emphasis on the ergonomic design of swaging and crimping machines. The latest models are designed with operator comfort and safety in mind, featuring intuitive controls and adjustable components that minimise physical strain and improve accessibility. These ergonomic advancements are crucial in ensuring that operators can work efficiently and safely, particularly in high-volume production environments.
As hydraulic systems advance in complexity, the need for dependable and high-quality hose and fitting connections becomes ever more critical. Recent strides in swaging and crimping technologies reflect the industry’s dedication to addressing these evolving demands. By integrating automation, digital precision, adaptable equipment, and ergonomic design, manufacturers are not merely improving the functionality of hydraulic components they are also setting the stage for future breakthroughs in the field.
-
PPMA 2025
23 September, 2025, 9:30 - 25 September, 2025, 16:00
NEC, Birmingham UK -
Advanced Engineering Show 2025
29 October, 2025, 9:00 - 30 October, 2025, 16:00
NEC, Birmingham UK