Pushing the limits, preventing problems
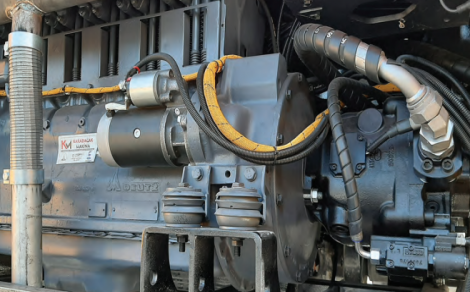
Electrification isn’t just a matter of switching out the diesel engine for an electric motor. It requires a thorough review of connected systems – in particular the hydraulic system. Using the same components in electric machines as those used in conventional machines often requires more battery power or a larger electric motor. H&P reports.
Original equipment manufacturers (OEMs) have quickly discovered the need to rethink efficiency and productivity when electrifying machines. MPG Makine Prodüksiyon Grubu learned this firsthand when designing a truck-mounted electric crane for one of its customers. The Konya, Türkiye-based OEM produces truck-mounted hydraulic cranes with folding and telescopic booms as well as aerial work platforms and tree transplanter machines. MPG prides itself on high quality and advanced technology, a result of the continuous system development studies the company undertakes to produce more capable products and introduce innovative machines to the market.
A stalling problem
One of MPG’s Netherlands-based customers requested an electric truck-mounted crane. The truck’s drivetrain was to remain diesel-powered, while the crane structure would be powered by an electric motor connected to grid electricity indoors and to a generator outdoors. The customer preferred not to use the truck’s diesel engine to power the crane, even for outdoor work, due to increasing maintenance costs.
MPG quickly got to work, conducting a literature review plus field and market research on electrical drive technology for the crane. The project team selected the electric motor and driver by making necessary power requirement calculations and designing the electrical and hydraulic circuit diagrams, then proceeded to testing. That’s when the challenge began.
Veysel Alver, general manager, MPG, described the issue: “To make the machine in the simplest way, we designed it with a 3-phase asynchronous electric motor. When we did our tests with the piston pump we use in existing machines, we could not achieve the performance we wanted, and we also experienced electric motor stalling problems. In this case, we also needed a soft starter and inverter for the electric motor.”
As with hydraulic pumps connected to diesel engines, pumps connected to electric motors can induce stalling conditions when the pump reaches maximum flow and pressure if there is no controlled limit for torque. Stalling an engine or electric motor results in lost productivity and operator frustration.
One potential solution to this problem is increasing the size of the motor, which MPG wanted to avoid as it would mean higher costs and a larger space requirement. Based on their studies, MPG engineers knew a torque-limiting pump could help.
Electronic torque limiting to the rescue
Compared to a standard pressure-compensated load-sensing (PCLS) pump, a hydraulic pump with electronic torque-limiting (ETL) control is a highly featured component ideal for machines with electronic control architectures. ETL pumps feature an electronic controller, angle sensor, and electric proportional relief valve, which together enable active control of how much power or torque the pump is consuming. Software controls the system and the tuning of the pump.
-
PPMA 2025
23 September, 2025, 9:30 - 25 September, 2025, 16:00
NEC, Birmingham UK -
Advanced Engineering Show 2025
29 October, 2025, 9:00 - 30 October, 2025, 16:00
NEC, Birmingham UK