Optimising compressed air systems: Reducing costs and enhancing sustainability
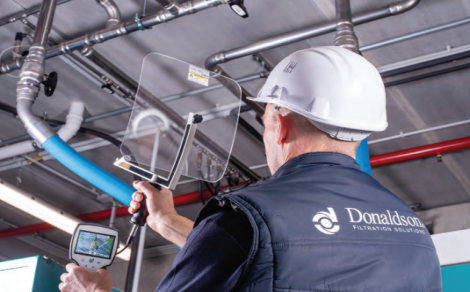
In today’s climate of fluctuating energy prices, the inefficiency of compressed air delivery systems can be a significant financial burden. System leaks and outdated filters exacerbate this issue, but an optimised setup can yield substantial savings. Donaldson, a leader in filtration solutions, has demonstrated this potential through a series of efficiency projects.
One recent initiative involved 12 compressed air efficiency projects across its facilities, resulting in an annual energy demand reduction of 496 MWh. This saving is equivalent to powering 220 electric cars for a year or making nearly 2400 round trips between Land’s End and John o’ Groats. As experts in air filtration, Donaldson’s ability to identify and implement these efficiencies highlights the potential for similar savings in other industries reliant on compressed air.
According to the U.S. Department of Energy, generating compressed air can account for up to 30% of a plant’s electricity costs. Fortunately, these costs can be mitigated through measures like stopping leaks and using high-quality filters and components designed for optimal performance with minimal pressure losses. Donaldson says its filter media and flow-optimised filter housings are key to unlocking these energy-saving potentials.
Advanced filtration technologies
Donaldson’s Ultra-Web fine fibre technology for inlet air filters provides efficiencies of 99.99%, combining superior dust surface loading with a low pressure drop to contribute to energy savings. The company’s advanced oil filters, utilising resin-free Synteq XP technology, trap contaminants effectively while maintaining low pressure drops and extended service life, further reducing the total cost of ownership (TCO).
Once air leaves the compressor, it undergoes several treatment stages. Donaldson’s UltraPleat filtration technology uses coated high-tech fibres to create a pleated filter medium with a surface area over 400% larger than traditional media. This technology achieves oil aerosol separation efficiencies of ≥99.9% while cutting differential pressure by 50%, translating to significant economic benefits. For example, a 300 mbar reduction in differential pressure over 8000 operating hours can save approximately £5650 per UltraPleat filter annually.
To maximise the efficiency of UltraPleat technology, flow-optimised filter housings and continuous monitoring through an economizer are essential. This system not only indicates the most economical replacement time for filters but also provides data for higher-level control of compressed air systems. For larger compressed air volumes, UltraPleat filters ensure a prolonged service life with consistently low differential pressure, vital for achieving energy savings.
Donaldson’s Ultrapac Smart adsorption dryer technology incorporates these filters, along with capacity control and compressor couplings, contributing to substantial savings in regeneration air. Additionally, energy-efficient dryer technologies, such as prefilters with electronic, level-controlled drains, zero purge technology, and energy-saving control systems, enhance overall efficiency.
Addressing air leaks
Even the best filter technology cannot compensate for system leaks. Common sources of leaks include pipe connections, conditioning units, shut-off valves, quick couplers, and terminal equipment. These small leaks can cumulatively lead to significant losses. For instance, a company operating a 150 kW compressor for 6000 hours a year can waste nearly £50,000 annually due to leaks.
Detecting and addressing leaks requires regular servicing and preventive maintenance. Donaldson offers advanced technology and techniques to help customers detect and minimise energy costs, including Air Quality Audits. Its experienced customer service engineers can identify even the smallest leaks while the plant operates normally, providing detailed reports and tailored optimisation concepts.
Optimising compressed air systems can significantly reduce energy consumption and costs while also contributing to environmental sustainability. Implementing advanced filtration technologies and efficiency improvements showcases the potential for substantial savings and enhanced performance in various industries.
For further information please visit: https://www.donaldson.com
https://www.linkedin.com/company/donaldson/
-
PPMA 2025
23 September, 2025, 9:30 - 25 September, 2025, 16:00
NEC, Birmingham UK -
Advanced Engineering Show 2025
29 October, 2025, 9:00 - 30 October, 2025, 16:00
NEC, Birmingham UK