Marine Compressors – guide to shipborne applications, energy efficiency and worldwide
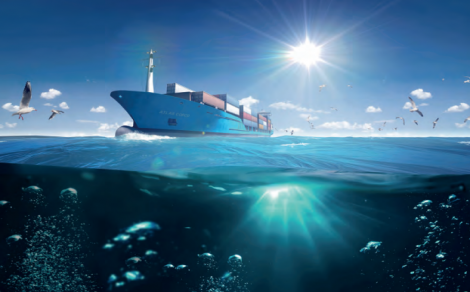
By Paul Clark, business line manager CTS sales and marketing, Atlas Copco Compressors.
In the engine room or on-deck site, marine compressor systems are vital elements that must be specifically designed for multiple duties as an integral part of shipboard operations. They have to be robust machines able to perform reliably within the environmental conditions experienced while operating in mid-ocean, often days or weeks away from landfall and servicing facilities.
As marine compressor solutions become ever more sophisticated, specialised and energy-efficient, it is a wise precaution for ship owners and shipyards making equipment choices to examine the application roles, the equipment options, and the regulatory framework specific to maritime operations − the important factors to be considered in meeting the challenging engineering environment within today’s global shipping operations.
The starting point for these considerations has to be the principal duties of shipboard compressors.
Principal compressor duties
The first and foremost duty for the compressor is providing starting air for the main engines, normally at a pressure of 30 bar. Then follows the need for starting air for diesel generating sets which can be at 10 or 30 bar pressure depending on the starting air method, either direct in the cylinder or by a starting air motor.
High quality, clean, dry, oil-free air at 7-8 bar is an equally essential requirement for consistently accurate performance of vital bridge instruments, such as monitoring and engine control systems. It is also required for cargo pumps turbine governors and LNG/LPG cargo instrument air applications. Also needing clean dry air, is a vessel’s main engine remote control pneumatic systems, tank gauging operations, together with temperature and pressure controls.
At the same time, an efficient supply of low-pressure working air is an essential requirement for a wide range of other important applications − for tools, air-operating lights, air-operated fans, dry bulk handling, nitrogen booster compressor operation, ballast water treatment, soot filtration, exhaust gas cleaning equipment, air for sewage systems − everything from regular maintenance to bulk handling needs a 7 bar-13.8 bar air supply on tap.
And finally, there are specialist applications such as medical air or highpressure air for seismic operations, bubble curtains and for diving or air breathing apparatus bottle filling.
The equipment criteria
Within the practical shipboard constraints of minimum power consumption and restricted installation space, it is vital for shipyards and shipowners to ensure that the performance and build quality of a marine compressed air system can meet the operational criteria for reliability, energy efficiency, stability, safety, and regulatory compliance.
Reliability: That has to be the watchword for all essential shipboard systems. Marine compressors must be fully optimised for shipborne use and be designed and constructed for continuous operational capability within engine room environments of up to 50 degrees C ambient. That means robust, tried and tested components and ancillaries that combine the benefits of long service intervals and energy-efficient whole life performance.
-
PPMA 2025
23 September, 2025, 9:30 - 25 September, 2025, 16:00
NEC, Birmingham UK -
Advanced Engineering Show 2025
29 October, 2025, 9:00 - 30 October, 2025, 16:00
NEC, Birmingham UK