Ensuring reliability and efficiency through comprehensive compressor assessments
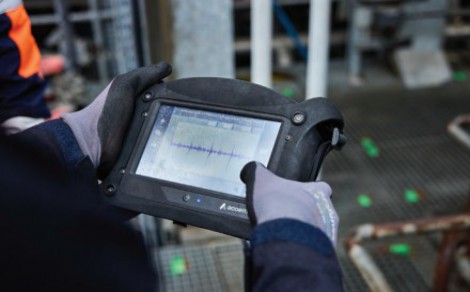
Compressors lie at the heart of countless businesses across countless industries, and those businesses’ success depends on their equipment performing reliably, efficiently and sustainably. When this isn’t the case, they need easy and fast access to engineering excellence to assess and help them improve their compressors. H&P reports.
Correctly assessing any issues with a compressor—or areas for improvement— isn’t always a simple job. It’s a task that must be approached with care and correct planning.
There are three key stages of any highquality assessment process, ranging from taking precise measurements and carrying out technical meetings through to the careful renewal of documentation. Though they may seem ancillary to the process, these steps are vital to achieving engineering excellence, ensuring operators get the most out of their assessments and helping the assessors do their jobs effectively.
The three key elements of a high-quality assessment process:
One: Precise measurements
The foundation of any high-quality compressor assessment relies upon the quality of data collection, and this includes taking relevant and accurate measurements.
This initial phase is critical, forming the bedrock upon which all subsequent analysis and recommendations are built. Measurements, and the collection of instrumentation readings, ensure that the assessment is grounded in objective data rather than subjective judgment, leading to more reliable and actionable insights.
The measurement process involves several key components. Its scope varies depending on the issues operators might be having with specific compressors and includes a wide range of data. This includes everything from standard compressor instrumentation readings, such as pressures, temperatures and gas flow, to measurement of ‘general health indicators’ such as vibration level and temperatures. It also covers more advanced techniques like pV-analysis, time-domain vibration diagnostics and leakage measurements.
Vibration measurements are essential for detecting integrity issues, while comparative thermography is used to identify hotspots and other thermal anomalies within the compressor. Such anomalies often indicate potential problems like leakages, insufficient cooling, excessive friction or inadequate lubrication. These not only cause excess wear but can also result in a drop in efficiency and, therefore, higher emission levels.
Taking this range of measurements for reciprocating compressors allows engineers to gather detailed data on the performance and condition of their components. This includes assessing the integrity of cylinder liners, piston rods, and seals, as well as how the pressure and temperature changes at different stages of the compression process.
These precise measurements offer a data-driven basis for recommendations. This means carefully tailored solutions can address the specific needs and conditions of a system, ensuring that the recommendations are both practical and effective, leading to improved compressor performance, efficiency, and sustainability.
Two: Comprehensive technical meetings
Engaging with the customer’s technical team is crucial for understanding the specific needs and performance targets of a compressor. These meetings aren’t just a way to arrange visits and hammer out details; they form a vital part of the assessment process, as they establish a collaborative environment where detailed discussions can take place and ensure all stakeholders are aligned.
-
PPMA 2025
23 September, 2025, 9:30 - 25 September, 2025, 16:00
NEC, Birmingham UK -
Advanced Engineering Show 2025
29 October, 2025, 9:00 - 30 October, 2025, 16:00
NEC, Birmingham UK