Breathing new life into a CO2 compressor
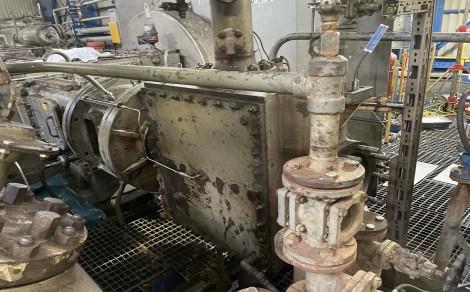
Routine maintenance often highlights items that need repairs, but discovering a major high-pressure asset is severely corroded has the potential to significantly impact operations. One crop nutrition company in Germany identified just such a problem and needed a new compressor cylinder to be installed at the next scheduled shutdown, just six months away. The solution offered by Burckhardt Compression not met the required timeline, and also addressed several other related issues at the same time.
Prevention is always better than cure; avoiding unplanned downtime through proactive maintenance is key to extending reliability and minimising costs. At the same time, recognising the need for expert intervention and appreciating that it doesn’t necessarily come from the original equipment manufacturer (OEM), can support a faster resolution.
The routine maintenance inspection of a CO2 compressor and its 2’410 kW (3’230 hp) motor revealed that the cylinder was heavily corroded. Looking at the history of the machine, the cylinder support had broken repeatedly, causing unscheduled shutdowns. The plant’s maintenance team wanted to achieve a reliable and sustainable solution that would ensure the long-term reliability of the compressor.
The first major challenge was finding the expertise required to resolve the problem, which can be difficult for ageing assets that are no longer supported by the OEM. In this case, Burckhardt Compression, which has a global presence and decades of expertise in compressor engineering, was the first port of call. From the outset, the best solution appeared to be the manufacture of a new cylinder using reverse engineering techniques. This would enable several issues to be resolved at the same time. The new cylinder could be produced using forged steel, rather than cast steel and more robust cylinder supports could be incorporated to improve reliability.
A field service engineer was quickly arranged to visit the site and take the necessary dimensional measurements. Due to operational restrictions, this task had to be completed within one day. The objective was to record all the data required to manufacture a new cylinder that would be a direct replacement as well as achieving improved performance.
Burckhardt Compression’s engineering skills and manufacturing facilities ensured that the replacement cylinder offered the best possible solution. The opportunity to improve on the original design enabled the new cylinder to be optimised for better cooling as well as easier cleaning.
As a result of Burckhardt Compression’s solution, the refurbished compressor has received a new lease of life. Reliability is greatly improved, and the cylinder support has retained its integrity; all of which was achieved within a tight timeframe and in budget.
Matthias Reese, Project Management & Engineering at Burckhardt Compression commented: “The solution we offered was exactly what the customer was looking for. With our systematic approach, our compressor experts not only looked at the obvious issue but wanted to find a holistic solution to improve the reliability and support the customer’s sustainability goals. The compressor has been running without issues for almost two years now and we have received another order for the exact same solution for another compressor.”
For further information please visit:
http://www.burckhardtcompression.com
https://www.linkedin.com/company/burckhardt-compression/
-
PPMA 2025
23 September, 2025, 9:30 - 25 September, 2025, 16:00
NEC, Birmingham UK -
Advanced Engineering Show 2025
29 October, 2025, 9:00 - 30 October, 2025, 16:00
NEC, Birmingham UK