- Home » Editorial » Hydraulics
Keeping food and beverage production moving
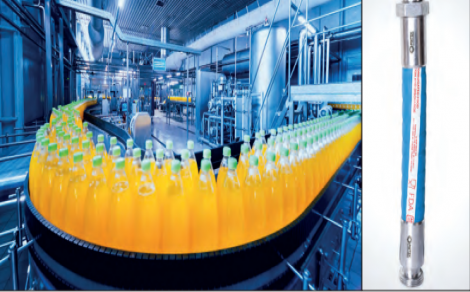
Operating on a complex and dynamic scale, the food and beverage industry relies heavily on efficient processes to the meet the demands of a growing consumer base – this is where hydraulics plays a crucial role. Ian Cochran, national technical support manager at Pirtek UK & Ireland, explains further
The UK’s food and drink industry is the country’s biggest manufacturing sector by turnover, according to the government’s Department for Business & Trade, valued at over £104 billion. It is larger than the aerospace and automotive industries, with market growth expected to continue this year. Operating on a complex and dynamic scale, the industry relies heavily on efficient processes to the meet the demands of a growing consumer base – this is where hydraulics plays a crucial role.
Hydraulic systems, due to their extensive application in heavy-duty machinery, are not typically associated with sectors that require precision and extreme cleanliness such as food & beverage and pharmaceutical. However, the incredible versatility of both hydraulics and pneumatics mean that food production facilities actually rely on them to perform a wide variety of tasks, ranging from processing through to final packaging and even product loading. The extreme temperatures, high pressure, and high speeds at which production lines can often operate mean that hydraulic and pneumatic solutions are often the most viable solutions.
Everything from chocolate to yoghurt, pastry to beer, and biscuits to coffee, all need the assistance of hydraulics and pneumatics to make the final product and both systems will be at work at every stage of manufacturing process. Here are just some of the places they will be in operation:
Chopping, cutting, slicing and dicing systems
The movement of products around the production line
Ingredient dispensing systems for both solids and liquids
Powering mixers and blenders
Blow-moulding and manipulation of food grade packaging
Shaping and forming end products
Sealing of bottles and cans
Keeping the process moving
Hydraulics and pneumatics provide torque, force, displacement, and rotation not just for the product themselves but also for the components of the production line system. They aid in tasks such as the opening and closing of oven doors, the redirection of items along an assembly line and also in the hygienic cleaning and sanitation of processes after food production has ceased.
Pneumatic systems that are driven by air compressors are often used in food production as a reliable way of generating motion; they are also easy to clean which is essential in a food production environment. On the other hand, hydraulic systems are particularly useful where lifting or lowering is involved. Both systems are capable of driving processing, assembly, or packaging lines even in the most difficult work environments. They are often preferable to electric power as they are largely unaffected by extreme dust and moisture.
Consequences of hydraulic failure
If the hydraulics within a food and beverage plant were to fail, it could have several implications depending on the specific processes and equipment involved.
Many food and beverage processing plants rely on hydraulics to operate various equipment such as pumps, conveyers, mixers, and packaging machines. If the hydraulics fail, these machines may not function properly or could completely stop working. This could lead to unwanted downtime due to production delays, decreased productivity, and potentially even product spoilage if ingredients or products are not processed or handled correctly Additionally, failure of a hydraulic system could compromise safety mechanisms such as emergency stops, guards, or interlocks. This could pose a significant risk to operators and other personnel working in the facility, potentially leading to accidents or injuries. And finally, downtime might cause the production line to be halted, resulting in financial losses and poor customer relationships.
If a hydraulic failure should occur, partnering with a hydraulic hose provider that can deliver a quality but quick service can help minimise these implications. To receive a best-in-class service, technicians should understand the strict regulations governing food manufacturing, fitting hoses that are FDA compliant and made from high purity materials. FDA certification means that the hydraulic hose is made from food grade materials that will not impact the odour or taste of the product and are specifically designed for food and agricultural industries. For example, Pirtek supply a corrugated FDA hose that is ideal for the transfer of oily products in full suction and discharge applications. Not only does it meet the sanitary standards of regulatory bodies such as REACH, ADI, FDA, USDA and 3A, but it is also built on special stainless steel mandrels for perfect cleanliness.
Additionally, it is recommended that regular servicing and preventive maintenance is carried out by industry trained technicians to keep machinery and equipment in working order.
For further information please visit: https://www.pirtek.co.uk/market-sectors/food-beverage/
********************************************************************************************************
Case study
A leading UK coffee manufacturer turned to Pirtek to help reduce downtime and increase efficiencies. As the customer operates around the clock, a hydraulic failure could cause significant disruption if it is not attended to rapidly regardless of time of day. One scenario, for example, saw Pirtek technicians called-out to site in the twilight hours to rectify a hydraulic system due to a steel pipe rupturing on the ceiling. While the height for the repair could have caused a challenge, the technician was able to cut and replace the pipe from a hybrid access platform. The job was completed safely and the system was back up and running again quickly. In addition to reactive callouts, Pirtek has also supported the coffee manufacturer with preventive maintenance during planned shutdowns. These shutdowns usually take place a couple of times a year and involve the thorough cleaning of machinery and burners. Taking advantage of closures, Pirtek technicians survey all the hydraulic hoses on site and provide recommendations about which one should be replaced and then carry out the work. No matter the type of job, the technicians always follow strict health and safety rules and regulations and comply with any standards outlined specifically for the food and beverage industry such as wearing the correct PPE. There is minimal disruption to production lines thanks to preventive maintenance and emergency callouts, meaning the business is kept operational at all times. The emergency call outs are then reduced, saving the customer both time and money.
********************************************************************************************************
https://twitter.com/PirtekUKIreland
https://www.linkedin.com/company/pirtek-uk-ltd/
-
PPMA 2025
23 September, 2025, 9:30 - 25 September, 2025, 16:00
NEC, Birmingham UK -
Advanced Engineering Show 2025
29 October, 2025, 9:00 - 30 October, 2025, 16:00
NEC, Birmingham UK