Safeguarding your compressed air assets
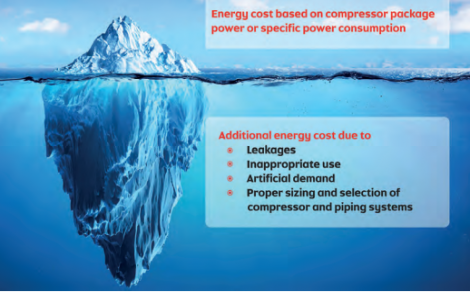
By David De Pril, director, product management and marketing, ELGi
Energy efficiency is increasingly important for us all as it directly relates to costs. Increasing regulatory pressure is also on the horizon in the form of the EU Commission’s proposed revision to the EU Energy Efficiency Directive (EED). The revised EED will make the EU’s energysaving objective legally binding, obliging EU countries to collectively reduce their energy consumption by 9% below 2020 levels by 2030. Additionally, EU countries will likely have to achieve new annual savings of 1.5% of total energy consumption as of 2024, up from the current level of 0.8%.
In manufacturing processes using compressed air, energy efficiency improvements are critical since air compressors consume approximately 12% of electrical energy. What’s more, over the lifespan of an air compressor, 80% of the cost is energy use, and 20% is the cost of the unit. However, do compressed air users have the big picture of where these costs come from and what contributes to them?
Looking beyond the system
There are many technical and economical choices when taking the right approach to reducing the energy intensity of compressed air systems. Not so long ago, the industry focus rightly looked beyond the unit efficiency to the system and system efficiency. Greater awareness of operational needs and the increased pressure to reduce energy use and improve efficiency prompt a closer examination of the system. More granularly, how do we balance operational needs, capital costs, the lifespan of critical assets, and energy use?
The traditional total cost of ownership (TCO) approach looks at the energy cost based on a compressor package’s power or specific power consumption. Whereas a complete operational analysis looks at everything from the compressor to the environment in which it operates, as well as operational demands such as peaks and troughs in air demand and operational expansion planning. A finite analysis of the bigger picture – understanding how even the most minor system elements impact the energy consumption associated with the compressor.
The aim is to strike the right balance in technical and economic choices - in compressor units, capacities, operational parameters, energy efficiency, planning for future air demand changes, and considering energy costs related to leakages, inappropriate use of air, artificial demand, etc.
Compressed air users need to look at their operational demand and see what compressed air is necessary for their specific operation throughout the production cycle. Then they should study how to optimise the compressor room and question the hardware and the settings of the compressed air installation. After this study, compressed air users can truly safeguard their assets, investments, and energy costs and ultimately achieve a new low in compressed air TCO.
Close, but let’s take a wider look at safeguarding your assets
-
PPMA 2025
23 September, 2025, 9:30 - 25 September, 2025, 16:00
NEC, Birmingham UK -
Advanced Engineering Show 2025
29 October, 2025, 9:00 - 30 October, 2025, 16:00
NEC, Birmingham UK