Safeguarding your compressed air assets
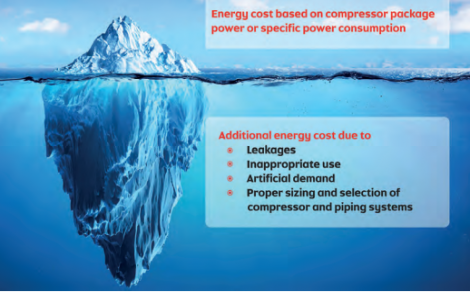
To describe it better, let’s take a look at a hypothetical process when a customer considers expanding its manufacturing site, adding another production line, increasing its manufacturing capacity, etc. In such a case, a typical discussion between the compressed air user and air compressor supplier about the new compressed air demands starts with the customer’s request for more air assuming that an additional or larger compressor is the solution. The thing is, simply adding another compressor is not the answer when the surrounding system stays the same. This can result in too much stress executed on the system’s existing structure and can lead to reduced overall efficiency. Why?
When a manufacturing plant or line is being built, a compressed air system is planned and designed to fit the capacity load of a particular production process. It all works as planned and achieves planned results. When the company’s operations grow, and the plant increases production, the air-demands change. And adding another compressor to fit the increasing needs is not the answer. Before even considering that compressed air users should work with the experts to conduct a detailed analysis of how the current system is performing at a given time and within given demands. Before any decision is made, a holistic analysis of the entire production system, historical and planned air requirements, current piping, and checks for leaks should be done.
Quite often, the expansion of a manufacturing site or production line won’t even require adding another compressor. Finetuning the existing assets to run at proper and adapted loads – not at the highest pressures or extreme duties – can result in lowered pressure on the entire system and reduce energy consumption. It’s an easy route to add another compressor, but taking a holistic approach, analysing and optimising the existing system and its elements, is the key to safeguarding your assets and achieving the desired energy efficiency improvements.
Let’s Audit, Right-Size, and Implement
Before making a decision on what to do, whether to replace a compressor, add another one, or adjust the existing system, an audit of the operations is necessary. A compressed air auditor can check the entire system and establish the input, the state of the compressor units and how they are running, and what exact pressures are required. This will paint a picture of the system with its surroundings, elements, pipework, and critical consumption. With this knowledge, we can move to the next step, which is making an educated decision on how to optimise it to meet the new requirements. Very often, the new, expanded production requirements can be met with the same power but adjustments to the airflow (of course, depending on the size of the expansion). It’s all about rightsizing the air needs.
-
PPMA 2025
23 September, 2025, 9:30 - 25 September, 2025, 16:00
NEC, Birmingham UK -
Advanced Engineering Show 2025
29 October, 2025, 9:00 - 30 October, 2025, 16:00
NEC, Birmingham UK