- Home » Editorial » Hydraulics
How to prioritise quality and efficiency for hydraulic systems post pandemic
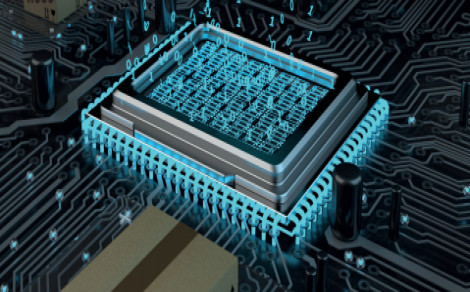
By John Joyce, marketing director, Brennan Industries.
As the pandemic continues to be upon us, manufacturers and suppliers are facing the increasing need to prioritise quality and efficiency. The shock of supply and demand has decreased production volume and stopped operations in 2021. Nevertheless, that doesn’t change the need to have quality along with efficiency post-pandemic.
Shifting to smart technologies, systems and processes
To ensure quality and efficiency are top of mind, it’s imperative to take a close look at processes involving the manufacturer and supplier. By understanding the issues that can happen on both sides, the amount of time, money, resources and frustration will be decreased.
A big part of Industry 4.0 is Industrial IoT (IIoT). A study by the American of Quality found that businesses shifting to digital processes and IIoT have seen an increase in efficiency by 82%. It increases efficiency by enabling automation and the use of robotics. By bypassing manual tasks and making data-driven decisions, errors can be reduced.
Quality and efficiency for hydraulics
Why is this important for hydraulics? Safe hydraulic system design and component placement are crucial to the maintainability and service life of a system. When components are in the correct location, it allows for easy access. Hydraulic systems are only as good as the components, which is why proper design and selection are important for every application.
For example, O-rings can fail in their application because of the surrounding environment. If the O-ring isn’t installed correctly, it can cause serious issues. Look at what happened with the Space Shuttle Challenger disaster. It was caused by the failure of two redundant O-ring seals in a joint in the shuttle’s rocket booster. The environment’s low temperatures decreased the ability to seal the joints.
When it becomes a supply chain issue
Because of the high demand and lack of supply, it’s more important now to make sure quality and efficiency are at an ultimate high in the production process. A failed O-ring or fitting, for example, can cause a line to be down, which in turn prevents production. By having an influx of smarter controls with real-time data, quality and efficiency are increased.
Another common failure in hydraulics is the hose. An intelligent hydraulic-hose-condition monitoring system can detect these kinds of failures. Certain properties in the hose change as it approaches failure, which then causes the system to signal a predictive maintenance notification. Also, there can be sensors in the fittings to monitor the hose. The sensors establish a baseline and if it goes below normal, failure is anticipated, and an alert is processed.
Predictive maintenance relies on data, and IIoT manufacturers can monitor the environmental and systematic conditions surrounding the hydraulic system, thus preventing downtown. Hydraulic systems are sensitive to temperature and pressure; so, it’s important to keep a close eye on them.
-
PPMA 2025
23 September, 2025, 9:30 - 25 September, 2025, 16:00
NEC, Birmingham UK -
Advanced Engineering Show 2025
29 October, 2025, 9:00 - 30 October, 2025, 16:00
NEC, Birmingham UK