Raising the standard for compressor design
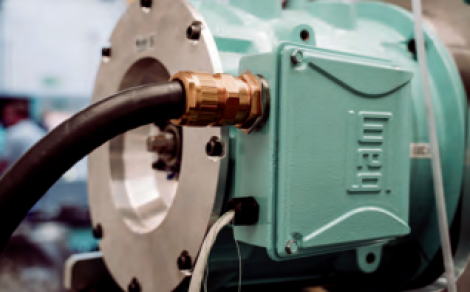
Marek Lukaszczyk, European and Middle East marketing manager at industrial motor manufacturer, WEG, explores what a new type of positive displacement compressor design, combined with a specially designed ultra-premium efficiency permanent magnet motor, means for industry.
Positive displacement compressors are mechanical devices that increase the pressure of a gas by reducing its volume. From bottling plants to pneumatic conveying, compressors are ubiquitous, powering processes and machines, while transferring and blowing things around a factory – be it pasta, cereals or other foods, pharmaceuticals, plastics or even the granular absorbents used in nappies and sanitary products.
In fact, they are considered to be the fourth utility for making products. These four requirements consist of water, gas, electricity and compressed air – the basis behind all manufacturing. And they’re not just found in industry. In public transport, for example, when a bus approaches a bus stop and drops down to the curb, it is running on air suspension from a compressor to let people on. In contrast, compressors are also at the heart of heat pumps to heat houses, ever more so as gas boilers will be phased out of new builds by 2025. Compressors are even in refrigerators to keep them cold.
Simply put, compressors are everywhere, and because of this they consume a lot of energy – typically about 12% and as high as 55% in some manufacturing facilities. However, the potential is yet to be fully realised, and the motors that power these machines can have a big impact on CO2 emissions.
New compressor design
The recent implementation of the new European efficiency regulations, which now cover a wider range of electric motors to deliver an estimated 10-terawatt hour (TWh) of energy savings by 2030, mean that companies need to innovate. However, the industry has been slow to modernise. The first rotary compressor design can be traced back to Italian designer Ramelli’s water pump, from 1588. Despite having been designed as a water pump, its core design is used to this day, such as in vane and rolling piston compressors and in air conditioning systems.
Another machine designed as a water pump, originally made from wood, was re-purposed as the lobe blower back in the 1860s. This made the Roots brothers wealthy and still accounts for most low-pressure air compressor sales. Arguably, the last big change was the screw compressor – invented by a Swedish inventor Alf Lysholm in 1935, originally for a steam turbine. This currently dominates the mid-pressure market.
Lontra therefore decided to transform the industrial compressor landscape. Lontra realised that compressors simply need to get gas in efficiently, compress it without leakage and then let it out again without too much loss. Lontra designed a machine that is inspired by the piston and cylinder found in combustion engine powered cars. Essentially, the Lontra machine uses the piston and cylinder, before wrapping the cylinder around into a doughnut shape, ensuring the two ends meet.
-
PPMA 2025
23 September, 2025, 9:30 - 25 September, 2025, 16:00
NEC, Birmingham UK -
Advanced Engineering Show 2025
29 October, 2025, 9:00 - 30 October, 2025, 16:00
NEC, Birmingham UK