Raising the standard for compressor design
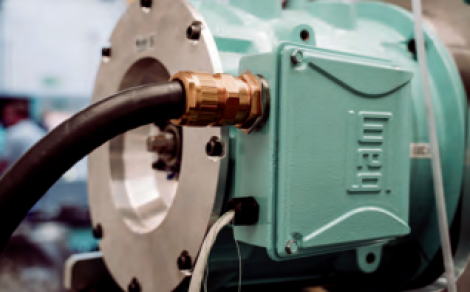
The two ends then separate by a rotating disc, enabling the piston to become a blade. Never seen before, Lontra now have a raft of patents for this new geometry, which does the aforementioned basics well.
Early testing, in the water industry, has showed electricity savings of over 21% against competing machines. Usually, compressors are used in the water industry to blow air through wastewater, feeding natural bacteria and breaking down pollutants. This process alone accounts for 1% of all UK electricity usage.
A recent trial of Lontra’s latest machine for the pneumatic conveying sector – blowing various solids through pipes – has also shown savings of up to 34% against a market-leading competitor
Exceeding energy requirements
To help achieve this, Lontra contacted WEG to be part of this wholly new compressor technology. Since most compressors are powered by electric motors, Lontra called upon WEG, a global manufacturer of industrial motors, to design a special motor for the LP2 Blade Compressor – with maximum international energy (IE) efficiency class standard.
This is Lontra’s first industrial blower, involving WEG supplying and specifically manufacturing a WMagnet IE5 ultrapremium permanent magnet motor, rated at 80kW, 2500rpm, constant torque and with hollow shaft – achieving 97% efficiency levels across the entire speed range. The motor is shaft mounted reducing further losses in the system, increasing the overall efficiency of the compressor.
Under the current European efficiency regulations, electric motors must now reach the IE2, IE3 or IE4 efficiency level depending on their rated power and other characteristics. For instance, three-phase motors with a rated output between 0.75kW and equal to or below 1000kW, must have reached the IE3 level by July 2021. Motors between 75kW and 200kW must also meet the IE4 level as of July 2023. However, Lontra’s new compressor uses a specially designed IE5 electric motor – the highest IE efficiency class – surpassing current requirements. The IE5 permanent magnet motor was chosen not only for its high efficiency, but because it generates less heat in the rotor and has a steadier temperature due to it being liquid cooled, reducing the likelihood of overheating. Still, the industrial market is dominated by induction motors. While these motors are reliable and have acceptable efficiency ratings, the emphasis on global warming has propelled the emergence of electric vehicles and has, therefore, led to research into permanent magnet motors.
As a result, electric vehicles have already moved from induction motors to permanent magnet motors, a switch that is lacking across the industrial landscape. But compressors do not have to absorb huge amounts of energy, as proven with Lontra’s new compressor.
https://www.linkedin.com/company/weg/
https://www.linkedin.com/company/lontra-ltd-/
-
SOUTHERN MANUFACTURING & ELECTRONICS SHOW 2025
04 February, 2025, 9:30 - 06 February, 2025, 15:30
Farnborough International Exhibition Centre, off Aerospace Boulevard, Farnborough GU14 6TQ -
SMART Manufacturing & Engineering Week
04 - 05 June, 2025
NEC, Birmingham UK -
PPMA 2025
23 September, 2025, 9:30 - 25 September, 2025, 16:00
NEC, Birmingham UK -
Advanced Engineering Show 2025
29 October, 2025, 9:00 - 30 October, 2025, 16:00
NEC, Birmingham UK