- Home » Editorial » Hydraulics
The case for electro-hydraulic actuators

Anders Karlsson, product specialist linear actuators, Thomson Industries Inc., offers his view on the benefits of electro-hydraulic actuators over hydraulic cylinders.
System designers have long given hydraulic cylinder-based motion control systems first consideration in applications requiring handling of loads upwards of 1.360 kg, mostly because of the high power density of the cylinders themselves. But when the designer factors in the large space required for the intricate infrastructure needed to achieve that power, that power density becomes much less attractive.
Now, however, thanks to technology that builds hydraulic motion control into an envelope smaller than a conventional electromechanical unit, designers and end-users can enjoy the power conversion advantages of hydraulic fluids without the expense, complexity, and need to clean up after conventional hydraulic cylinderbased systems. Electro-hydraulic linear actuators are fast becoming the motion designer’s choice over hydraulic cylinders for a wide range of heavy load handling in outdoor equipment, marine, military, aerospace and many other applications.
Structural differences
A hydraulic cylinder-based motion control system converts electrical energy into motion using an assembly involving oil reservoirs, electric motors, pumps, oil filters, relief valves, and directional valves. The speed desired and the size of the cylinder dictate the size of the pump needed, which then determines the size of all other components. The higher the required speed, the higher the cost of the system and the greater the operating space needed.
An electro-hydraulic system, in contrast, embeds the equivalent of that infrastructure into an envelope that is about the same size as a conventional electromechanical actuator. (Figure 1) An electric motor rotating clockwise turns a pump that pressurize the hydraulic fluid.
Valves open to draw fluid from both the reservoir and head side, and control delivery to extend the rod. On retraction, the motor runs counterclockwise, reversing the operation, and returning the fluid to the reservoir and the opposite side of the piston. For loads of up to 2.180 kg, miniaturising that infrastructure has significant advantages over hydraulic cylinders in power density, maintenance requirements, location versatility, cleanliness and cost, while handling comparable shock loading. (Figure 2)
Load capacity
By replacing the gear and lead screw assemblies of conventional electromechanical actuators with a compact hydraulic system, electrohydraulic actuators can move up 2.180 kg. Loads of this size have typically been relegated to hydraulic cylinder-based systems. This load range is more than 500 kg greater than the capacity of a conventional electromechanical actuator.
Power density
For raw power density, electro-hydraulic designs have a distinct advantage. While the electro-hydraulic actuator and hydraulic cylinder may not be too much different in size, the support infrastructure needed to operate the hydraulic option consumes significant space.
Cleanliness and safety
Electro-hydraulic actuators also have an advantage in cleanliness and safety. External leaks at pipe and hose fittings of hydraulic cylinder systems occur over time due to vibration and other factors. When these leaks happen, the cylinder leaks a film of oil into the plant environment with every stroke. Internal leaks present an even greater maintenance challenge. Leaks inside the pump, pressure controls, directional valves and cylinder convert pressure and flow to heat or wasted energy, which will reduce actuator speed. In industrial settings, leaks also cause odor and present slipping hazards.
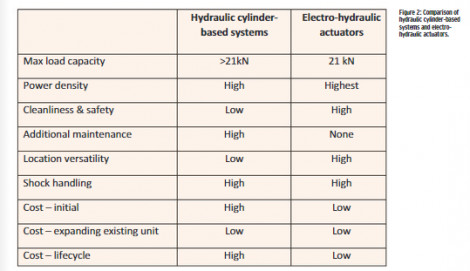
-
PPMA 2025
23 September, 2025, 9:30 - 25 September, 2025, 16:00
NEC, Birmingham UK -
Advanced Engineering Show 2025
29 October, 2025, 9:00 - 30 October, 2025, 16:00
NEC, Birmingham UK