HepcoMotion creates a series of animations to highlight key product benefits
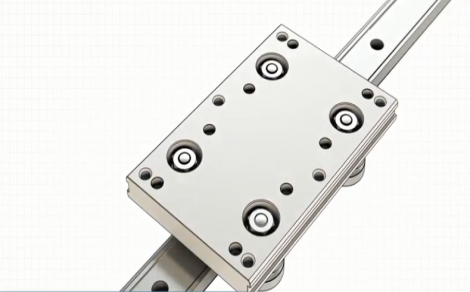
After 20 years, HepcoMotion’s flagship GV3 range is continuing to serve a diverse range of linear and automation applications. With the introduction of new components to the range, and a new product category, Hepco has produced a series of six animations highlighting the major benefits of V Guide technology against ball rail systems.
A useful resource for design engineers, the technical animations showcase the features and benefits of GV3 and highlight how V guide systems can save designers both time and money. Areas showcased include:
Harsh environment
Specifying a linear motion product for a harsh environment can be a challenge. The ability to cope with factors such as extreme temperatures, dust, dirt or chemical exposure is a combination only the toughest systems can survive. Hepco’s V guide systems have a unique wiping action that tends to expel debris – making it perform particularly well in harsh environments. The animation visually shows how the outer diameter of the bearing travels at a faster speed than the inner diameter.
The difference in speed causes particles nearer the centre to move outwards to the periphery, and to be expelled. Due to the geometry of the slide and bearing interface, debris is expelled to the outer diameter of the bearing in a spiral motion, away from the running surface. This complex explanation is effortlessly explained in a graphic way through the visual animation in a clear and engaging way.
Lubrication
Supplying a constant source of lubrication is a key consideration for any design engineer; Hepco has therefore created an animation dedicated to showing how this can be managed using standard Hepco options. This animation shows the different possibilities of lubrication delivery available with Hepco’s V guides, such as the automated bleed lubrication system which delivers lubricant directly to the contact surface between the slide and the V bearings.
The animation shows a cross section of the slide rail with a bleed lubrication hole from the underside, joining with a perpendicular channel which is routed through the V face.
Here, lubricant is pumped up and out at right angles directly to the running face of the bearings and slide – exactly where it is needed. The lubrication source supplies grease constantly, and being remotely located, the system does not need to be stopped at regular intervals for re-lubrication, reducing downtime and increasing machine efficiency.
Ball rail re-lubrication intervals are far shorter than V guide systems, with frequent maintenance and downtime required to keep them running. The animation shows how ball rails will eventually purge any lubrication from within the block, leading to catastrophic failure if not re-lubricated regularly. Re-lubrication intervals are far longer for the GV3 system, and it requires less lubricant to work effectively.
The animation also showcases the ability of GV3 to run completely dry - a requirement for some food, medical and scientific applications. A cross section of the V bearing shows the internal ball bearings continuing to work perfectly well, moving the GV3 up and down the guide without lubrication, and problem free.
-
PPMA 2025
23 September, 2025, 9:30 - 25 September, 2025, 16:00
NEC, Birmingham UK -
Advanced Engineering Show 2025
29 October, 2025, 9:00 - 30 October, 2025, 16:00
NEC, Birmingham UK