Automation is unlocking the future of AM services
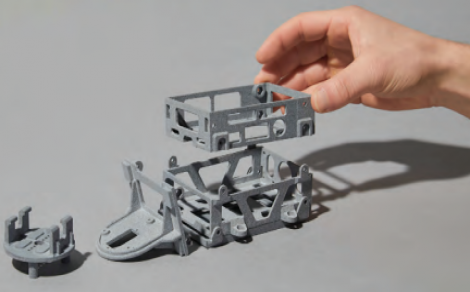
Automation is redefining additive manufacturing (AM), streamlining processes from quoting to post processing. Felix Manley, Co-founder of 3D People, explores how automation enhances efficiency, improves consistency, and delivers faster lead times—ultimately transforming the customer experience and ensuring AM services can scale to meet the growing demands of modern manufacturing.
Across today’s ever-changing manufacturing landscape, automation is no longer a luxury — it’s a necessity. The field of additive manufacturing (AM) is no exception. As co-founder of 3D People, a subcontract AM service bureau, I’ve seen firsthand how integrating automation into our processes has not only improved operational efficiency but also delivered tangible benefits to our customers.
Automation within AM goes beyond just robotic arms on production lines. It starts at the very front-end of service delivery — quoting, ordering, file preparation, and production management — extends across the entire workflow through post-processing and finishing of parts and incorporates the logistics of distribution and delivery. When these stages are optimised through automation, the results are faster lead times, more consistent parts, and a better overall experience for customers.
In this article, I want to dive into the role automation plays in the approach to AM services, highlighting the benefits it delivers to customers, how it drives operational efficiency, and why it’s essential for the future of this industry.
Why Automation matters in AM
One of the most common misconceptions about AM is that it’s an inherently fast process. While it’s true that 3D printing can drastically reduce time-to-part compared to traditional manufacturing methods, many manual steps still exist that can slow down the process. Automation aims to remove these bottlenecks.
From an AM service provider’s perspective, automation at the front-end — specifically in quoting, file handling, and order management — is transformative. For customers, this means faster responses, greater accuracy, and a more seamless experience. Automation in quoting, file preparation, and production management plays a significant role in reducing lead times, improving quality, and ensuring consistent results for customers. Each of these are as brings its own unique advantages.
Automated quoting systems
Gone are the days when customers had to wait for a sales rep on an eternal lunch break. Modern automated quoting systems can provide instant or near-instant pricing based on uploaded 3D files.
With automated quoting, customers benefit from faster decision-making. Instant quotes allow them to make quick decisions and proceed with orders without unnecessary delays. They also receive accurate pricing. Automated systems reduce human error and provide more accurate, consistent pricing across different projects.
And then there’s transparency, customers being able to see the cost breakdown and understand how different factors such as materials, finishes, and quantities affect the final price. This streamlined process enables customers to move from idea to production-ready parts in a fraction of the time it would take with traditional methods.
-
PPMA 2025
23 September, 2025, 9:30 - 25 September, 2025, 16:00
NEC, Birmingham UK -
Advanced Engineering Show 2025
29 October, 2025, 9:00 - 30 October, 2025, 16:00
NEC, Birmingham UK