Keeping production safe and food supply secure
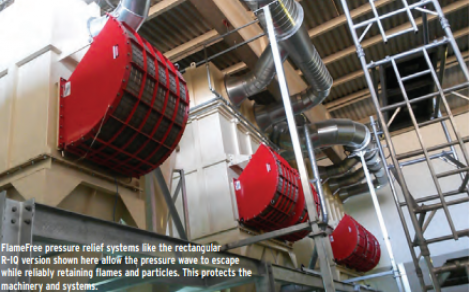
Industrial processes involving dry foodstuffs or animal feed can quickly create an explosive atmosphere due to airborne dust particles. Dust explosions pose significant risks to worker safety, equipment integrity, and production continuity. As the industry faces growing challenges in ensuring food security, robust explosion protection measures are essential to maintaining safe and uninterrupted operations
The effects of the war in Ukraine and the associated energy crisis continue to be felt across all industries in Europe. Companies that make and process foodstuffs and animal feed face major challenges
Maintaining food security has become a major issue in society. One of the keys to a secure and reliable supply of food is ensuring a continuous production process. But the processing or storing of powdered foodstuffs presents a major risk of unplanned production stops. Dust explosions are a pernicious threat with devastating potential due to the massive rise in pressure they create.
Virtually all dry bulk products used in agriculture, such as flours made from grain, pulses and seeds, can form an explosive mixture in the right dust concentration. Other potentially explosive substances include starches, binders, sugars and sweeteners. Even non-powdered materials like feed pellets often create fine, flammable dusts through constant friction.
Critical mixtures of dust and air frequently arise around machines like conveyor systems, mills, dust filters or cyclones, especially if they are operated pneumatically. Excess powder can escape from a bucket elevator and concentrate in the air. The movement means that the dust particles remain airborne much longer than usual. Alongside flames and glowing embers, dust explosions can also be triggered by hot surfaces, static electricity or sparks generated mechanically or electrically. These are too many risk factors that cannot be completely eliminated. Certified explosion protection in design is therefore essential for process managers looking to safeguard production.
Active suppression systems
Fast-acting suppression systems are designed to detect and suppress dust explosions at their earliest stages. Solutions such as the IPD system, developed by Bormann & Neupert by BS&B, use sensors to detect sudden pressure increases in critical areas, such as bucket elevators. In response, the system deploys a food-safe extinguishing agent within milliseconds to suppress the explosion before it can develop into a destructive event.
Explosion isolation
Preventing an explosion from propagating to interconnected systems is another key safety measure. Chemical barriers, such as those used in suppression systems, can stop flames from spreading. Additionally, active mechanical isolation solutions, including Redex active isolation valves and IVE pinch valves from BS&B, act as physical barriers to contain explosions within a specific section of a process.
Pressure relief systems
In areas where controlled venting is an option, pressure relief systems, such as BS&B’s rupture discs and FlameFree pressure relief solutions, provide another layer of protection. These systems activate instantly upon reaching a predefined pressure threshold, allowing pressure waves to escape while preventing flame propagation. Options such as the R-IQ and IQR FlameFree systems incorporate multi-layer stainless steel filters that retain burning particles while ensuring pressure is safely dissipated.
Integrated safety strategies
Given the complexity of dust explosion risks, implementing a combination of suppression, isolation, and pressure relief measures ensures comprehensive protection. Solutions such as the SparkEx spark detection system, which identifies and neutralises ignition sources before they lead to an explosion, further enhance safety.
Process managers must prioritise explosion protection as part of equipment design and operational safety protocols. Certified solutions, such as those offered by Bormann & Neupert by BS&B, provide industry-compliant protection while supporting long-term operational efficiency. By integrating these measures, manufacturers can mitigate risks, maintain regulatory compliance, and ensure the continuous and safe production of foodstuffs and animal feed
-
PPMA 2025
23 September, 2025, 9:30 - 25 September, 2025, 16:00
NEC, Birmingham UK -
Advanced Engineering Show 2025
29 October, 2025, 9:00 - 30 October, 2025, 16:00
NEC, Birmingham UK