- Home » Editorial » Pneumatics
Key considerations when buying air lines
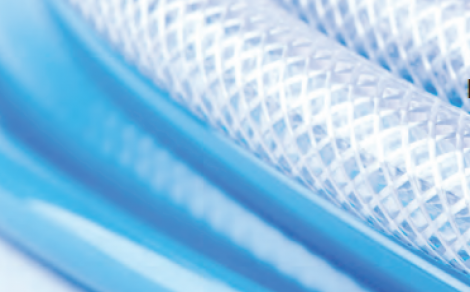
Efficiency and reliability in industrial pneumatics hinge on quality air lines. Often overlooked yet crucial, they ensure smooth operation, minimise downtime. Whether setting up or upgrading, selecting the right air lines is paramount for optimal performance. H&P takes a closer look.
When it comes to industrial pneumatics, the efficiency and reliability of your pneumatic system depend significantly on the quality and suitability of the air lines. These often-overlooked components play a crucial role in ensuring smooth operation and minimising downtime. Whether you’re setting up a new pneumatic system or upgrading an existing one, here are some key factors to consider when selecting air lines for industrial use.
Durability and material composition
One of the foremost considerations when choosing air lines is their durability. Industrial environments can be harsh, with exposure to dust, chemicals, and mechanical stress. Opting for air lines made from robust materials such as reinforced polyurethane or nylon ensures resistance to abrasion, corrosion, and degradation over time. Additionally, consider factors like flexibility and resistance to kinking, which can affect the longevity of the air lines in demanding applications.
Size and diameter
Selecting the appropriate size and diameter of air lines is crucial for maintaining optimal pneumatic performance. Larger diameter lines can accommodate higher flow rates and reduce pressure drops, which is essential for systems requiring rapid actuation or operating over long distances. Conversely, smaller diameter lines are suitable for low-flow applications or where space is limited. It’s essential to match the diameter of the air lines with the airflow requirements of your pneumatic components to prevent inefficiencies and ensure consistent performance.
Pressure rating
Another critical factor to consider is the pressure rating of the air lines. Different pneumatic systems operate at varying pressure levels, and using air lines with a pressure rating below the system’s requirements can lead to leaks, ruptures, and safety hazards. Ensure that the selected air lines can withstand the maximum operating pressure of your pneumatic system, taking into account potential pressure spikes during operation or fluctuations in supply pressure.
Temperature range
Industrial environments often experience fluctuating temperatures, from extreme cold to high heat. It’s essential to choose air lines capable of operating within the expected temperature range of your application to prevent premature failure or performance degradation. Look for air lines with a wide temperature tolerance and consider factors like thermal expansion and contraction to ensure reliable performance across varying environmental conditions.
Compatibility and fittings
Compatibility between air lines and pneumatic fittings is paramount for seamless integration and leak-free connections. Ensure that the air lines you choose are compatible with standard pneumatic fittings commonly used in your industry or application. Additionally, consider factors like thread size, thread type, and sealing mechanisms to ensure a secure and reliable connection between components. Investing in quality fittings and connectors can prevent costly leaks and maintenance issues down the line.
-
PPMA 2025
23 September, 2025, 9:30 - 25 September, 2025, 16:00
NEC, Birmingham UK -
Advanced Engineering Show 2025
29 October, 2025, 9:00 - 30 October, 2025, 16:00
NEC, Birmingham UK