Exploring the potential & challenges of electro-hydraulic systems in manufacturing
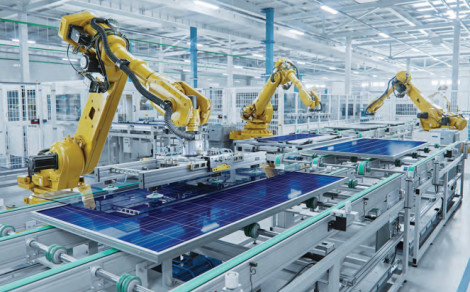
Manufacturers are considering electro-hydraulic systems to boost efficiency and precision. Yet, challenges like integration complexities must be tackled for these systems to deliver on their promise in manufacturing. H&P reports
Many businesses within the manufacturing industry are currently considering the adoption of electro-hydraulic systems, which are believed to offer improvements in efficiency, precision, and versatility by leveraging the combined strengths of electrical and hydraulic technologies. While these systems hold promise for transforming manufacturing processes, their widespread adoption faces notable challenges that need to be addressed to fully understand and harness their potential benefits.
Advantages
Electro-hydraulic systems present a range of advantages. Recognised for their highpower density, they offer robust performance in compact forms, which proves beneficial for applications necessitating precise control and substantial force, including robotics, CNC machines, and heavy machinery. The amalgamation of electronic control with hydraulic power facilitates highly accurate movements and adjustments, particularly crucial for manufacturing processes requiring stringent standards, as seen in the automotive and aerospace sectors. Additionally, these systems contribute to enhanced energy efficiency by utilising variable-speed drives and advanced control algorithms to align power output with demand, thereby curbing waste and operational expenses. Their adaptability, catering to a broad spectrum of applications from small-scale automated systems to large industrial machinery, positions them as a versatile solution for varied manufacturing requirements.
However, alongside these advantages, there are notable challenges in integrating electro-hydraulic systems into manufacturing processes. A prominent hurdle is the considerable upfront cost associated with their implementation. This includes not just the acquisition of advanced equipment, but also the expenses related to installation and integration into existing systems. This financial burden can be particularly daunting for many manufacturers, especially small and medium-sized enterprises (SMEs), potentially deterring them from pursuing this technology.
Integration
The integration of these systems into current manufacturing processes poses a significant challenge due to the need for substantial modifications to existing machinery and control systems. Ensuring interoperability between new and old systems can be complex and requires careful planning and execution. Additionally, operating and maintaining electro-hydraulic systems requires a workforce with specialised skills in both electronics and hydraulics, leading to the necessity for comprehensive training programmes. However, the shortage of skilled workers in the labour market exacerbates this issue. Furthermore, while these systems are designed to be robust, their sophisticated nature can present maintenance challenges, necessitating regular, skilled maintenance to ensure reliability and minimise downtime, which can incur logistical and financial strains.
Strategic approach
To address these challenges effectively, manufacturers may consider adopting a strategic approach. One potential method involves implementing electro-hydraulic systems gradually rather than all at once. This phased approach allows for necessary adjustments and learning opportunities, thereby reducing disruptions and spreading costs over time. Collaboration among manufacturers, technology providers, and educational institutions is crucial for developing training programs and support services. Such partnerships can help bridge the skills gap and offer ongoing technical assistance.
Additionally, government and industry bodies can provide policy support and incentives to alleviate the financial burden and promote innovation. Measures such as grants, tax breaks, and subsidies can make the initial investment more feasible for manufacturers. Highlighting the long-term return on investment is also important. Despite the initial high costs, the potential efficiency gains, reduced operational expenses, and improved product quality may result in substantial savings and competitive advantages over time.
The introduction of electro-hydraulic systems in manufacturing presents both opportunities and challenges. While these systems offer benefits in terms of efficiency, precision, and versatility, concerns such as cost, integration complexity, and the need for specialised skills must be addressed. Through a collaborative and strategic approach, supported by various stakeholders, the industry can successfully transition to this innovative technology, unlocking its full potential and ushering in a more efficient and advanced manufacturing landscape
-
PPMA 2025
23 September, 2025, 9:30 - 25 September, 2025, 16:00
NEC, Birmingham UK -
Advanced Engineering Show 2025
29 October, 2025, 9:00 - 30 October, 2025, 16:00
NEC, Birmingham UK