- Home » Editorial » Pneumatics
Achieving ATEX approval for pharmaceutical manufacture fluid control automation
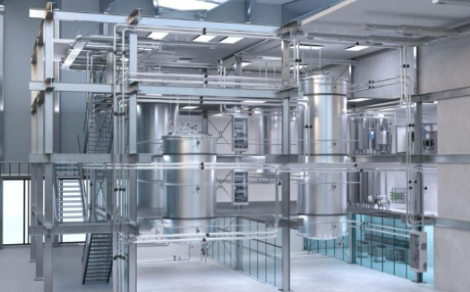
H&P looks at the challenges of creating new production lines or expanding existing ones.
Pharmaceutical plants and those creating active pharmaceutical ingredients (APIs) face many challenges in delivering end products to the highest standards. With a variety of solvents and other combustible ingredients used for manufacturing, many production areas are classified under ATEX/Ex regulations, which stipulate rigorous build specifications for all equipment installed in zoned areas.
Creating or expanding a production process within a pharmaceutical environment offers a number of challenges. From the creation of an automation concept and developing it into a physical model to sourcing all the components, connecting them together and integrating the new process with the wider infrastructure, the whole process requires considerable expertise.
Decentralised and distributed automation
Process automation predominantly uses either a distributed pneumatic control concept or a decentralised one. The former uses control cabinets that are positioned close to the process, usually within the zoned area, and therefore they must also be certified for their location together with all the control valves and sensors.
When there is a more wide-ranging project, such as modifying an existing control system or building a completely new one, the task of delivering a fully certified installation is more complex and requires special skills and expertise. In such situations, it is important to select partners that understand process control design and have the ability to deliver bespoke solutions using the latest technology – all certified to the standards in force locally.
Systems can only realise the expectations of the client if they are conceived, designed and manufactured by a single, dedicated team with the experience to appreciate the fine detail involved.
Damien Moran, pharmaceutical industry specialist at Bürkert Fluid Control Systems explains that his company’s Systemhaus concept uses expert teams of designers, project managers and engineers that work together to produce innovative solutions.
Custom cabinets
One of the first decisions is the size of cabinets required for the project, which may be restricted to a few ‘standard’ sizes from some suppliers. Cabinets can occupy too much space, which can be a very limited resource in pharmaceutical environments.
A custom control cabinet that is destined for Zone 1/21 must be built using ATEX certified components, but the enclosure itself does not automatically receive ATEX approval, it will have to be independently certified after the build has been completed. This can cause delays for installation and commissioning, unless the manufacturer is approved to supply a declaration of conformity.
For the components and pipework inside the cabinet, every item must be correctly specified for the application, with documentation to support it. The control equipment within the cabinet can be quite complicated and include valve islands, intrinsically safe valves, remote I/Os, components for filtration and pressure regulation as well as electrical connections and switches.
-
SMART Manufacturing & Engineering Week
04 - 05 June, 2025
NEC, Birmingham UK -
PPMA 2025
23 September, 2025, 9:30 - 25 September, 2025, 16:00
NEC, Birmingham UK -
Advanced Engineering Show 2025
29 October, 2025, 9:00 - 30 October, 2025, 16:00
NEC, Birmingham UK