Four ways to make your vacuum system more efficient
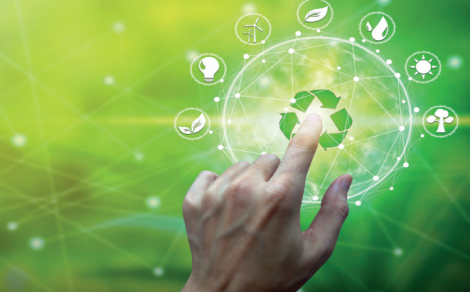
By Martina Höller, electrical technology product manager CEE, SMC Austria.
With energy prices surging across Europe, efficiency has become a high priority for all manufacturing and process plants using vacuum handling systems. Fortunately, based on decades of experience and knowhow, SMC can outline four simple ways that you can reduce the energy consumption of your vacuum system. Using less energy per lift/transfer will provide a direct contribution to your bottom-line profitability while simultaneously supporting industry’s drive to net-zero carbon emissions.
The latest energy-saving technology and process engineering can make a genuine difference to vacuum handling applications, whether the sector is packaging, metalworking, automotive, healthcare or any other. Simply follow these four steps to see a notable improvement in your system’s efficiency.
It’s possible to generate vacuum centrally by means of a vacuum pump or de-centrally (directly on the machine) using vacuum ejectors. SMC’s extensive range of vacuum ejectors – from super compact inline ejectors up to ultra-high efficiency multi-stage ejectors with high-performance silencers – are suitable for vacuum flows up to 600 Nl/min, thus meeting the needs of almost any industrial application.
Specific parameters
Every type of ejector has its specific parameters, which are dependent on one another. These include: standard supply pressure (the amount of compressed air you need to achieve the highest possible vacuum pressure); maximum suction flow rate (volume of air taken in by the ejector); maximum vacuum pressure (maximum value of the vacuum pressure generated by the ejector); and air consumption (the amount of air consumed by the ejector when operating with the standard supply pressure).
4 bar: the optimal supply pressure (on average) for SMC ejectors Ask yourself, do you really need the maximum vacuum pressure to handle your workpiece? You need to pose this question because the level of vacuum pressure will relate directly to your air consumption and your costs. By way of example, if you use of 0.5 MPa (5 bar) main line supply pressure to operate our ZL112A ejector (with valves), your air consumption will total around 78 l/min (4680 l/hour) to achieve a maximum vacuum pressure of - 84 kPa.
However, by choosing to operate the ejector at a reduced 0.35 MPa (the standard supply pressure for this type of ejector), you can cut air consumption to 57 l/min (3420 l/hour) and still achieve the same maximum vacuum pressure (-84 kPa). A significant 27% energy saving.
As a point of note, while many manufacturers have yet to transition from 7 bar standard shop pressure, optimal vacuum operation takes place at an average of 4 bar, so reducing from 7 bar to 4 bar not only benefits your bottom line and the future of the planet, it will have no impact on the effectiveness of your operations.
-
PPMA 2025
23 September, 2025, 9:30 - 25 September, 2025, 16:00
NEC, Birmingham UK -
Advanced Engineering Show 2025
29 October, 2025, 9:00 - 30 October, 2025, 16:00
NEC, Birmingham UK