- Home » Editorial » Hydraulics
Understanding phantom particle counts
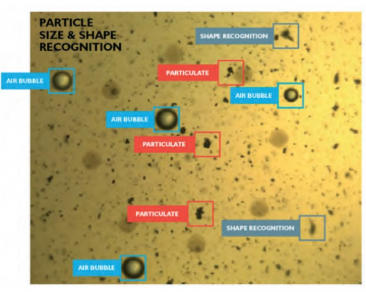
The increased use of siloxane based anti-foaming agents is causing issues with laser counter technology, writes Richard Price, managing director, Filtertechnik Ltd.
Imagine this: You have been filtering 150 litres of hydraulic fluid off-line with staged 5 and 1 micron filter elements at a rate of 25 litres per minute (1,500 litres per hour). You have been using a laser light-blockage method (LBM), automatic particle counter to verify the fluid cleanliness. The starting cleanliness per ISO 4406:2017 was 25/22/15. After eight hours, the cleanliness has only dropped to 22/20/13. You’ve checked that the filter element is not clogged and not in bypass. You even went through the trouble of making sure there was an element actually in the filter. How is this possible? What you are likely experiencing is a classic case of ‘phantom’ particle counting.
Demystifying phantom particle counts
Phantom particle counting is a documented problem, encountered when using laser-based LBM particle counters to verify the cleanliness of mineral based fluids containing certain insoluble additives. Silicone-based antifoam agents such as polydimethylsiloxane are common additives causing problems. Fluids used in mobile fluid power systems are typically formulated to contain high antifoam concentrations. Research has suggested that through differential surface tension, the silicone-based antifoam additive agents adhere to the inner wall of microscopic-entrained air bubbles, resulting in micelle-like encapsulations of the additive agents that then take on the apparent shape characteristics of a water droplet. The micellelike antifoam agent encapsulations typically range in 4-10µm in size. Once the encapsulations rise to the fluid surface, the agents quickly pierce the air bubble and return back into the fluid.
In a related study on the effects of a variety of nonsolid contaminants and additives on LBM particle-counting accuracy, it was found that a base stock mixture containing 0.02% (by weight) of a silicone antifoam agent increased the particle count by a minimum factor of three. The erroneous particle accounts were particularly evident in the 4µm and 6µm channels of the ISO 4406 cleanliness standard.
Limitations of Laser LBM particle counts
LBM particle counters are useful in many applications and the principle of the method is fundamentally simple. Fluid flows through a measurement cell containing a light source on one side and a receiver (photodetector) on the opposite side. The light source becomes partially blocked as particles pass through the measurement cell, creating a light radiation differential (a shadow) – corresponding to the circular cross-sectional size of the passing particles. Because of this fundamental operating principle, LBM particle counters suffer from a key drawback: the inability to discern solid contaminates from other contaminates like water, air bubbles, phantom particles, and so on. So, how can the phantom particles be overcome using automatic particle-counting technology? There is an alternative solution.
Digital imaging particle counting
Digital imaging particle counting uses size and shape-recognition technology, based on advanced algorithms to distinguish contaminants. For example, a direct imaging particle counter can distinguish contaminants into fatigue, cutting and sliding wear, as well as fibre and air bubble categories based on shape characteristics. It can also recognise water droplets (though water droplets are typically not recorded). The distinction of contaminants allows for more accurate particle counting, by negating nonsolid particles like entrained air bubbles and water droplets.
The S120 digital imaging particle counter can recognise solid particles and summarize them into 4, 6, 14, 21, 38, 70 and >100 micron ranges. It can also recognise shapes and give individual shape recognition counts as sliding, cutting and fatigue wear particles. Bubbles are also recognised and removed from the counts.
Therefore, digital imaging particle counting technology can negate the micelle-like antifoaming additive encapsulations as water droplets – phantom particles – allowing users to understand the condition of their fluids with confidence. Two case studies demonstrate how the Particle Pal Pro a fluid condition monitoring solution with digital imaging particle counting technology, can overcome phantom particle counting.
Laser vs digital imaging particle counter test
In a lab-based test conducted on base oil with no additives, Filtertechnik ran 2 particle counters feeding from the same oil warmed to 40degC. A PC9001 laser counter and an S120 digital imaging particle counter. Filtertechnik then dosed in exactly 100ppm polydimethylsiloxane anti foaming additive. The results were immediately apparent in the laser counter, affecting the 4 and 6 micron counts by up to 3 ISO codes, the 14 micron count slightly less so, but still an increase of 1 ISO code. The digital imaging counter remained unaffected by the additive.
Particle Pal Pro
The Particle Pal Pro is equipped with the S120 digital imaging particle counter and, together with water and oil degradation sensors, delivers a powerful on-site oil analysis instrument. Advanced software reports all the readings in a clear, easy-to-read format. Long term trending of assets is built in, as well as image capture of contamination for reporting purposes.
● New Digital imaging particle counting gives broad micron counts
4, 6, 14, 21, 38, 70 and >100 microns
ISO, NAS, SAE counts
Shape recognition
Particles are categorised as Sliding, Cutting and Fatigue Wear as well as Fibres
Air bubbles are counted and removed from the counts
● High resolution images are stored for reporting
Particles can be sized on the screen via the software to aid reporting
● The ability to self-prime, pump and measure oil up to 2,400cst
● Self-contained unit with battery and internal stepper motor pump
Accessory case with measurement flasks, vacuum thief pump etc. included
● Additional sensors included:
Water sensing %RH (tracked against temperature)
Remaining life of the oil via a TanDelta sensor
● A database of over 500 oils are included with calibrated degradation curves
Ability to self-calibrate any oil not on the database
● Export data to .xls, pdf and .jpg for the images collected
Case study
An OEM of large off-highway equipment was experiencing continuous particle counter inaccuracies at a verification stage of assembly. The rejections due to fluid condition were mounting, causing delayed shipments and significant related costs. The average holding time delay due to rejection was seven days, which incurred a holding cost of £1000-a-day per unit. At the consultation phase of the case study, eight units had been delayed.
The diagnosis was in: the existing laser light-blockage-type particle counters were providing inconsistently high and erroneous particle counts. The ISO 4406 cleanliness would frequently measure 23/22/19, despite a strong fluid-maintenance and conditioning regime. Third-party fluid analysis reports and fluid datasheets suggested that the synthetic hydraulic fluid contained a high concentration of a siloxane (silicone derivative) antifoaming additive, known to cause phantom particle measurements in LBM automatic particle counters.
Filtertechnik provided an extensive on-site demonstration that proved the advanced digital imaging technology of the Particle Pal Pro portable fluid contamination monitoring solution, which measured an average ISO fluid cleanliness of 15/14/10. This allowed the customer to successfully process the fluid and pass six units during the first day of demonstration. The two remaining backlogged units passed early on the second day of demonstration. The savings evidenced by the demonstration equated to approximately 35% in cost savings and an 81% reduction in holding time.
For more information:
https://twitter.com/FiltertechnikUK
https://www.linkedin.com/company/filtertechnik/about/
-
PPMA 2025
23 September, 2025, 9:30 - 25 September, 2025, 16:00
NEC, Birmingham UK -
Advanced Engineering Show 2025
29 October, 2025, 9:00 - 30 October, 2025, 16:00
NEC, Birmingham UK