- Home » Editorial » Hydraulics
The benefits of heat regeneration in heat exchanger systems
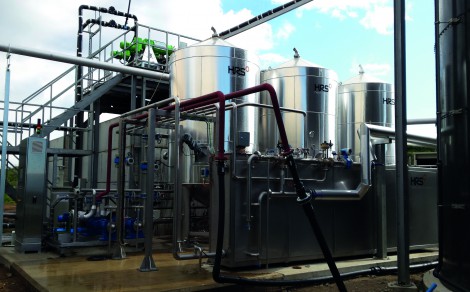
By Matt Hale, international sales and marketing director, HRS Heat Exchangers.
Heat exchangers are devices that transfer heat from one medium to another. As such, they are highly versatile and can be used for a range of heating and cooling operations. A classic example of heat recovery can be seen in food pasteurisation. If we imagine a factory producing pasteurised cream; the cream needs to be heated to the necessary temperature to achieve pasteurisation, then rapidly cooled to maintain shelf life and quality.
This is achieved through the use of two heat exchangers. The first uses hot water to raise the temperature, while the second uses chilled water to cool the cream down again. In the second process, the temperature of the cooling water is increased significantly. There are three options for dealing with this heated water: discard or discharge it elsewhere; cool it again for re-use; or cool it again for re-use, but use some of the heat it contains towards the heat required for the pasteurisation phase. This third option utilises heat recovery or heat regeneration, reducing the amount of new energy required for the subsequent first heating phases.
A second example shows how heat left over from one process can be recaptured to be used elsewhere. Many anaerobic digestion (AD) plants use heat exchangers to pasteurise the digestate produced during the AD process, so that it can be sold as an agricultural fertiliser. The ‘surplus’ heat which is generated after the system has been running for two hours is used to preheat the digestate, reducing total heat load and improving overall plant efficiency by increasing the amount of generated energy which is available for export or other uses, as opposed to being required for pasteurisation.
Combination
However, the greatest benefits of heat recovery can be seen where multiple heat exchangers are combined – for example, in a multi-effect evaporation system such as the HRS DCS Digestate Concentration System. This uses heat exchangers and evaporation to reduce the volume and increase the concentration of sludges and digestate. The first evaporation stage heats liquid digestate and uses a cyclone separator; the steam produced from this first cycle (usually available at 70degC) is then used as the heating media for the second effect, whereby the process is repeated.
The subsequent steam (usually available at 60degC) is then used as the heating media for the third cycle. The number of effects is determined by the level of dry solids required and the amount of surplus heat available, up to a maximum of four cycles. After the final stage the steam is condensed back to water and this heat is used to pre-heat the incoming product before the first stage of evaporation.
Heat recovery is not limited to systems dealing with liquids. HRS recently supplied a large G Series gas-to-gas heat exchanger to recapture heat from the high temperature exhaust gases leaving a large chemical reactor. This recovered heat is then used to help pre-heat the chemicals entering the reactor to around 500degC. As well as helping to improve energy efficiency at the plant, the new unit has been designed to cope with challenging operating conditions in order to provide a suitable working life.
-
PPMA 2025
23 September, 2025, 9:30 - 25 September, 2025, 16:00
NEC, Birmingham UK -
Advanced Engineering Show 2025
29 October, 2025, 9:00 - 30 October, 2025, 16:00
NEC, Birmingham UK