- Home » Editorial » Hydraulics
Pump energy efficiency and risk mitigation
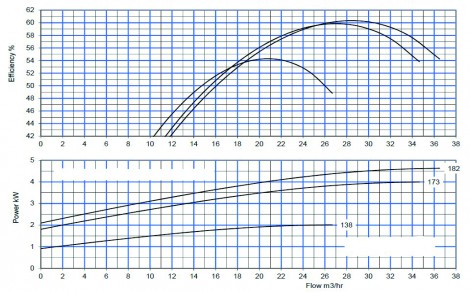
Ian Peel, technical manager, and Jason Butler, group commercial director, Pumptec Engineering, consider the benefits of adopting an ‘as new’ approach to pump maintenance and replacement.
Pause a while and think how many of your production processes require pumps to be available 24-7 in order to work. The efficient transportation of fluids is critical to most production sites, with the cost of energy, manufacturers must keep their pumps in near optimum performance in order to be efficient and reduce the risk of costly downtime related maintenance issues. While this starts with the selection criteria to ensure that the optimum pumping solution is provided, it must carry on as the plant evolves and the pumps wear.
The below article applies to all pump types but, for the purpose of illustration, follows the path of a baseplate mounted process pump as used in an industrial setting. As such, this article is not manufacturer-specific and is written from an independent expert point of view.
For a replacement pump the most obvious route is to look at the existing pump’s manufacturer and serial number to establish what is the most appropriate and nearest match. This is simple enough but only in the unlikely event that your plant and your processes have remained constant since the pump’s installation. Therefore, it is considered best practice to adopt a review akin to a new pump installation. To get the most out of a pump the following list of conditions of service should be considered and presented to the maintenance partner.
a. The pump’s role in the process: Is the duty cycle likely to be continuous or intermittent operation, and what are the suction conditions (i.e. always flooded or is it to work on a suction lift)? Most pumps work on flooded suction. There are, however, situations where the application dictates the pump must be self-priming; for example, removing process effluent from a sump or for loading and offloading tankers.
b. The liquid to be pumped: Is the liquid clean or are there solids present? If solids are present it is important to know the concentration, size and shape, (sharp or smooth) to determine the materials of construction and impeller design. For long-term reliability in a process with varying concentrations of an abrasive product, the materials of construction could range between hard metal, duplex stainless steel and 300 series stainless steel. Closed impellers are normally selected for handling clean or small solids or low % fibrous slurries, whereas a variety of open impeller designs are available for high viscosity liquids, low pressure pulse applications, high % concentration fibrous slurries, and liquids containing small and large solids of all shapes and sizes. Pumping temperature, SG or density and viscosity are key elements when deciding the best pump for the application. In some processes these can vary and that is why it is essential to have ‘maximum and/or minimum’ values as well as ‘normal’. Viscosity dictates pump type, where high values rule out a centrifugal pump making a positive displacement pump a better option
c. Net Positive Suction Head (NPSH): Pumping liquids at near boiling point triggers the question ‘how much NPSH is available?’. In some cases, the pump data sheet issued with the enquiry will state a figure. For others it is a case of understanding the phenomenon and what information is needed to calculate NPSH available in the system. The first thing to understand is ‘flooded suction’ and NPSH are not one and the same. Flooded suction (or suction head as it is sometime referred to) is simply the vertical height of the liquid level above the pump minus losses in pipework and fittings, whereas NPSH available is a function of pumping temperature, vapour pressure at pumping temperature, SG and arrangement of the suction pipework and fittings. In simple terms NPSH available in the suction system must always exceed NPSH required by the pump at the duty point, preferably by at least 1.0m. Pump performance curve show NPSH required from minimum to maximum flow. The simplest example is probably between a pump handing water at just below boiling point where the vapour pressure is almost atmospheric and, as a result, the NPSH available is the is the static suction head i.e. the vertical height of the suction tank above the pump centreline, minus losses in the suction pipework and fittings, versus a pump handling cold water where the vapour pressure is negligible so there is (in most cases) atmospheric pressure (10.0m NPSHA) as a starting point.
d. Design Standards and standardisation: As an engineer, you should also have a view on design standards. Nowadays, pumps are designed in accordance with either International Standards Organisation (ISO) or American National Standards Institute (ANSI). As ISO pumps are metric and ANSI Pumps imperial means users with both end up having to duplicate inventory of mechanical seals and bearings. By standardising on centreline heights and fixing dimensions for each size of bareshaft pump, the end user can change manufacturer, materials, or construction, without having to modify baseplates or pipework. It is important to note, however, that ISO and ANSI pumps are not dimensionally interchangeable, and a check needed to make sure the existing motor is suitable.
Once the pump type and design standard are settled, pump selection comes into play. Good practice for a fixed speed application is to select a pump with a mid-range diameter impeller with the duty point at the left-hand side of the best efficiency point. This means a bigger diameter impeller could be fitted within the range of the power of the installed motor for a change in the process or a reduced impeller diameter for the same reason. However, the ever-increasing use of variable speed drives to save energy and reduce running cost means selecting a maximum diameter impeller and varying the pump speed to achieve the duty conditions.
Electronic selection programme
Up to the 1990s, pumps were selected from coverage charts and individual performance curves. Nowadays, most manufacturers have an electronic selection programme which will select pumps on either price or performance. Once the user has selected the best pump for the application, data sheets, curves, and dimensions are available on the press of a key
The other major consideration is how to prevent leakage along the shaft into the product or bearings. Although gland packing is still the preferred option for certain applications when the pump is handling solids, mechanical seals are normally standard. The variety and combination of materials and arrangements make them ideal for both clean and solids handling applications.
The introduction of cartridge seals made life easier by the end user not having to dismantle, re-assemble and re-set the mechanical seal each time the pump was overhauled. When quoting the manufacturer will recommend which ‘piping plan’ to use for flushing the seal. The purpose of the ‘plan’ is to create the best working environment for the seal. These plans, of which are more than 70 covering many arrangements, were originally prepared by the American Petroleum Institute (AP1). Two of the more common are ‘API Plan 11 single seal – internal flush’ and API Plan 53A – dual seals, pressurised external reservoir pressurised liquid barrier’. Dual seals are now the norm for most solids handling applications. In the past the barrier fluid was water which was simply allowed to drain. Nowadays a self-contained ‘seal support’ system is the norm. Sealless magnetic drive pumps are a good option for liquids which solidify on contact with the atmosphere (e.g. sodium hydroxide), acids or valuable liquids (e.g. demineralised water) where leakage cannot be tolerated.
Whilst pump type, materials and construction are driven by understanding the process and having full details of the conditions of service there are other areas to consider when selecting a pump to deliver long term reliability and cost savings. The most important is the bearing arrangement and the method of lubricating the bearings. A ‘heavy duty’ combination of a roller bearing at the pump end and a back to back pair of angular contact bearings at the drive end is designed to deliver bearing life well in excess of that specified by industry standards. The bearings can be grease or oil lubricated depending on the end user’s preference.
Whole life costing should be the driver rather than initial purchase price. Why, because lowest initial cost does not always represent best long-term value for money. You need to consider running costs, cost of spares, mean time between repair over time. Equally the supply chain will have an effect, availability of spares and lead time for repairs will dictate if you should mitigate potential issues by having critical spares to hand. Again, this drives you towards a more standardised strategic standard for your pumps.
OK so you have your pump, your review has made sure it is fit for role, time now for the installation. It is usually worthwhile to get professional pump installation in order to ensure you are not having to replace due to alignment issues. While pumps are aligned at the manufacturer they must always be checked after installation both with pipework loose and with pipework connected. Please make sure that your pumps have not become pipe supports! It is always recommended that a suction compound gauge and discharge pressure gauge be fitted to the pump or in the adjacent suction and discharge pipework so ‘actual’ performance can be compared against ‘quoted’ performance and any problems identified and resolved. Keeping the plants pumps optimised through Planned Preventative Maintenance now comes to the fore.
Vibration analysis
Vibration analysis is the process used for measuring the vibration levels and frequencies of pumps (and other machines such as fans) and then uses that information to analyse how healthy the pumps and their components are. A data collector attached to the pump records the signal, the information is loaded into a PC for the Vibration Analysis Engineer to determine the health of the machine and identify possible impending problems with misalignment, lack of lubrication and bearing failure. A vibration analysis report (see panel) is issued the Maintenance Planners. The report shows the collection date, items that were within the alarm settings (green) and those outside the alarm settings (red) which require attention before they fail. For these items, an exception report (see below) trends performance over recent times and the Vibration Analysis Engineer makes recommendations as to what is required e.g. grease the bearings and take another reading.
Improving MTBF (Mean Time Between Failure) is always the aim. Allocating and tagging each pumps with a unique serial number is good practice and where the repairer maintains a record of plant item number, unique serial number, and dates between repairs as a way of measuring performance.
Assistance
We hope that this article has allowed you a greater degree of insight into the process of optimising the efficiency and lifespan of your pumps. As ever, Pumptec Engineering is available to assist you through this process and to be onsite, by your side, to keep these critical items of infrastructure off your risk register.
Pump repair and reporting
When the time comes for repair or overhaul the end user should receive a detailed inspection report with photos and recommendations (for evidence-based repairs and avoidance of unnecessary cost). Generally, the repair should include as a minimum:
• Shot blasting components covered in ‘hard’ product
• Replacing bearings
• Replacing gland packing and shaft sleeve
• Refurbishing or replacing the mechanical seal
• Dynamic balancing the rotating assembly (when impeller diameter is greater than 150mm)
• Hydrotesting to ensure no leaks

-
PPMA 2025
23 September, 2025, 9:30 - 25 September, 2025, 16:00
NEC, Birmingham UK -
Advanced Engineering Show 2025
29 October, 2025, 9:00 - 30 October, 2025, 16:00
NEC, Birmingham UK