Where to install a compressor and associated infrastructure
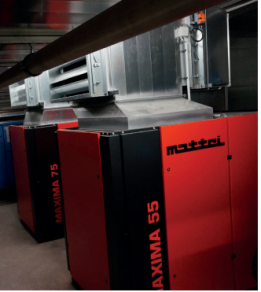
Historically, air compressors were housed well away from the production area due to their noise. Modern compressors are much quieter and can be located much closer to or even on the factory floor. Nevertheless, businesses should bear in mind how and where compressors are installed on their premises. Martin Chitty, business development manager at Mattei UK, outlines what the considerations are and how they can optimise compressor performance, maximise the return on investment and ensure compliance with environmental controls.
Particles and pollutants
Many manufacturing environments are plagued by a high concentration of airborne, small particles that are a side effect of the actual manufacturing process itself. These particles can block up vital parts of a compressor such as the cooler and intake filters. Furthermore, the compression process also makes the impurities more concentrated, which can significantly reduce the quality of your compressed air.
Rotary vane compressors cope better than screw compressors in many aggressive environments due to a greater tolerance to contamination by air borne particles. Nevertheless, it is still best practice to avoid locations with excessive airborne pollutants, such as loading and unloading areas.
Adequate ventilation
Air compressors move a considerable amount of air during their operation. A poorly ventilated area would cause a compressor to run unnecessarily hot, resulting in reduced efficiency, more frequent service intervals and ultimately, shortening its life span.
Proper protection
If the compressor needs to be housed in an enclosed area where the only way to get fresh air to the unit is to cut an opening in the wall, weather louvres should be considered to protect the compressor and the intake air from harsh weather. In the winter during sub-zero temperatures, a compressor will not start if its oil temperature falls below the minimum threshold. So, in addition to weather louvres, consideration should be given as to whether or not internal heaters should be installed if there is only one compressor, with no other form of maintaining a minimum temperature. Where there are multiple compressors, some of the waste heat could be redirected back into the compressor house rather than being expelled to atmosphere
Cheap heat
Up to 95% of a compressor’s kilowattage is discharged as heat. Typically, 80% of this waste heat is recoverable. So as a minimum, it’s worth using it for space heating, or more effectively as a method to heat water, which can be used as part of a production process, for heating or sanitary purposes. One significant advantage of using the heat for the latter is that the demand is year-round. On the other hand, demand for space heating is seasonal which should be taken into account when calculating the value of this recoverable heat.
Considerate cooling
Whilst rotary vane compressors run significantly slower than screw compressors and produce less noise, it is still essential toensure that any noise associated with the heat discharge process complies with local environmental controls. With this in mind, it is best practice to direct ducting used to expel heat away from noise-sensitive areas. Where this is not possible, noise attenuation measures within the ducting will be required.
Pipework pattern
The distance between the compressor and where the compressed air is used can have important implications in terms of system efficiency. Excessive lengths and bends in the pipe run lower efficiency. Where bends are unavoidable, use swept bends as these reduce pressure loss. You can also design the pipework to accommodate changes to the factory floor layout in the future. Correctly designed ring mains can be used so that sections of the pipework can be isolated to make modifications without disrupting the whole system.
Mattei offers a turnkey solution for the installation of its range of rotary-vane air compressors.
-
PPMA 2025
23 September, 2025, 9:30 - 25 September, 2025, 16:00
NEC, Birmingham UK -
Advanced Engineering Show 2025
29 October, 2025, 9:00 - 30 October, 2025, 16:00
NEC, Birmingham UK