Choose the correct servo motion control algorithms for your application
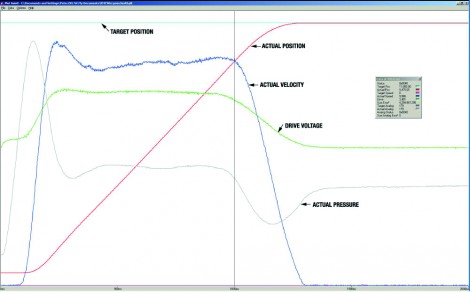
I-PD is another form of PID
Sometimes the target position is not generated by the motion controller. Instead, it may be generated by a joystick or the outer loop of another PID, or some other external source (see Figure 1c). In these cases, the target position is not guaranteed to move smoothly from one point to the next one. A PID control algorithm will try to follow the 'noisy' target resulting in 'noisy' actuator motion. In order to smooth the output to the actuator, the target position or the error can be filtered. Another technique is to use a form of PID called the I-PD.
This form of the PID uses the error only for calculating the integrator term. The P and D terms use only the negative feedback from the actual position. Since the P and D terms do not depend on the error between the target position and actual position, the controller will not generate large changes in the control output in response to 'noisy' target signals or when there are step changes in the target position (Figure 1c and 1d). Another way of describing the result in terms familiar to control system experts is to say that a well-tuned I-PD system effectively turns the controller, actuator and load into a multiple-pole low pass filter.
Of course, since the target position is not followed precisely when using filters or the I-PD algorithm, it limits the precision of profile tracking or synchronisation. So, while this algorithm is not suitable for every application, I-PD should be considered when the target positions, velocities or accelerations are not smooth.
Active damping
Active damping includes several methods of using feedback and a controller to electronically remove unwanted motion or oscillations. Active damping is normally required on systems that have a low natural frequency (i.e. they can be modeled like a mass on the end of a spring) and a high static to dynamic friction ratio. In these applications, the force builds up across the piston until the static friction force is overcome and the piston starts to move. When the piston moves, the force across the piston falls below the dynamic friction force and the piston stops. Figure 2 contains the motion plot of an actively damped system running an I-PD control algorithm. Any system that suffers from this stiction or chatter when running in open-loop mode will also do the same in closed-loop mode. Borderline systems also tend to exhibit the same stiction action when in closed-loop mode. The solution is to limit the acceleration, or the rate-of-change of the force on the piston.
This is problematic as calculating the instantaneous acceleration from position transducers is usually not feasible. Instead, some method of obtaining acceleration feedback is needed. The most direct way to do this is to attach an accelerometer to the carriage or actuator that is moving the load, but this can put the accelerometer in a nasty environment, which may not be practical.
Alternatively, the differential force across the piston can be used to estimate the acceleration. This requires a controller with the necessary analogue inputs to connect to the two pressure sensors and the ability to calculate the differential force on-the-fly. This technique is not as accurate as the accelerometer approach but is commonly used and very effective at solving the stiction or chattering problem described previously. Active damping reduces the rate of force buildup across the piston and works best where the objective is to get from one point to another as smoothly as possible. Of course, active damping also limits the maximum acceleration and deceleration, which in turn limits the ability to follow a motion profile. If this is the primary objective, then larger diameter cylinders should be considered in order to increase the natural frequency, which reduces the effects of any stiction.
-
Smart Manufacturing & Engineering Week
05 - 06 June, 2024
NEC, Birmingham -
HILLHEAD 2024
25 June, 2024, 9:00 - 27 June, 2024, 16:00
Hillhead Quarry, Buxton, Derbyshire UK