Choose the correct servo motion control algorithms for your application
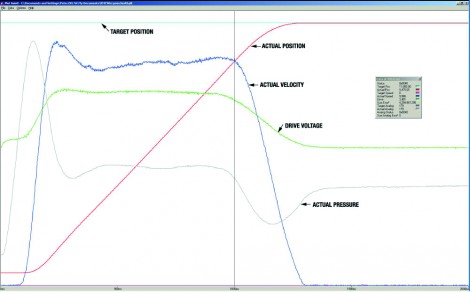
Another method of setting up an active damping control algorithm is to use a model-based control system that can internally estimate accurate accelerations. The advantage is that no extra hardware is required. The disadvantage is that the system must be relatively linear so that an accurate model can be developed. This explains why non-linear valve spools and pneumatic systems do not model well.
For best performance, it is better to design a hydraulic motion axis to have a high natural frequency and a linear response. But when extremely large masses must be positioned, at some point the extra expense of making the system hydraulically ‘stiff’ may become too great and electronic means are required to dampen the system.
Pressure/force control
Since fluid power is so well suited for applying pressure, a mention of pressure/force control is valuable. Today, pressure/force control (P/F) and dual-loop position-pressure/force control (P-P/F) algorithms are often used. Other systems may only need closed-loop for P/F and use open-loop for position. In some pressure applications, position PIDs can be used for pressure/force control. Other applications may need special features for combining open-loop position and single-loop P/F PID.
Dual-loop P-P/F algorithms offer more flexibility than single-loop algorithms. Since a controller cannot simultaneously fully control position and pressure, two PIDs are used, a position PID and a P/F PID, referred to together as a P-P/F PID. Both PIDs must be tuned and some method (such as a pressure threshold) used to transfer between the modes, so only one PID is operating at a time.
For many applications, a pressure limit mode is the best solution (see Figure 3). In this case, both PIDs run simultaneously, and the minimum output is used. Much can be discussed about P-P/F control and future articles will cover this topic in more depth.
Summary
Machine designers need to know that one size doesn't fit all in terms of hydraulic motion control. There are many control algorithms used in hydraulic applications, and the right one to use depends on the control needs of the application (see the table in Figure 4 for a summary). Some applications can benefit from combining two or three of the control algorithms discussed, depending on what part of the machine cycle is running. Discussing your application with the motion controller manufacturer early in the design process will help ensure that the controller has the algorithms you need.
-
Smart Manufacturing & Engineering Week
05 - 06 June, 2024
NEC, Birmingham -
HILLHEAD 2024
25 June, 2024, 9:00 - 27 June, 2024, 16:00
Hillhead Quarry, Buxton, Derbyshire UK