- Home » Editorial » Hydraulics
Seven reasons to monitor hydraulic flow on mobile machines
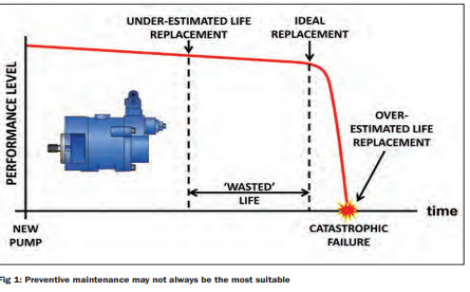
Fig 1: Preventive maintenance may not always be the most suitable
Cuthbert comments that preventive maintenance is a useful and practical procedure wherever there is robust documentation of component service life data and operating conditions are predictable. However, the reality for most on-and off-highway mobile machines is somewhat different. Factors such as vibration, temperature swings, shock and unstable power supply can lead to unexpected events and sudden failures.
Practicality, says Cuthbert, therefore suggests that continuously monitoring hydraulic performance via a permanently mounted flow meter will immediately detect any sudden deterioration and prompt appropriate action. Furthermore, with the right flow monitor it becomes possible to transmit data to the cloud via the vehicle’s CANbus network. Users can subsequently record and analyse performance data remotely and predict problems before they arise, with alarms highlighting any sudden changes.
Cuthbert highlights that Webtec’s newly developed CTA series turbine-type flow monitor with CAN bus interface fulfils this exact purpose. Developed in close collaboration with customers, the CTA series monitors both flow rate and temperature at high operating pressures, transmitting data via an SAE J1939 CAN bus found commonly on many vehicles. IP69K-rated for use in harsh operating conditions and fully EMC compliant, this compact, rugged flow monitor is an invaluable instrument that enables maintenance engineers to monitor system performance and schedule remedial service only when necessary rather than at estimated intervals.
Importantly, the new CTA is easy to integrate with IoT solutions and is currently in use at over 10 customers in sectors that include mining, municipal, agriculture and screening/crushing, deploying many different CAN buses and controllers.
2. Track cycle time to indicate machine health
With the CTA flow meter permanently installed, Cuthbert says that a number of further benefits arrive from the continuous monitoring of machine health and operational parameters. Monitoring cycle times, in particular, can highlight a gradual loss of productivity long before this becomes an issue or leads to a catastrophic failure.
Cuthbert says that assuming an overall machine cost of £300 per hour, a 5-hour job will cost £1500 at 100% efficiency. However, a machine that is only 80% efficient means the same 5-hour jobs now needs 6.25 hours, suddenly costing £1875. A machine operating 5-10% slower is hard to see without monitoring the pump’s power output. For OEMs, this tactic supports the provision of a ‘health monitoring’ subscription service and provides extra detail and confidence around scheduling future maintenance.
3. Reduce warranty costs
Combining flow and pressure data, says Cuthbert, permits the calculation of hydraulic power, which in turn can indicate how ‘hard’ a machine is working – whether due to operator behaviour or the ‘hardness’ of the earth or rock. These usage patterns relate directly to wear and can feed into a ‘power by the hour’ business subscription model. This type of data can also prove invaluable when deciding warranty claims.
-
SMART Manufacturing & Engineering Week
04 - 05 June, 2025
NEC, Birmingham UK -
PPMA 2025
23 September, 2025, 9:30 - 25 September, 2025, 16:00
NEC, Birmingham UK -
Advanced Engineering Show 2025
29 October, 2025, 9:00 - 30 October, 2025, 16:00
NEC, Birmingham UK