- Home » Editorial » Hydraulics
Seven reasons to monitor hydraulic flow on mobile machines
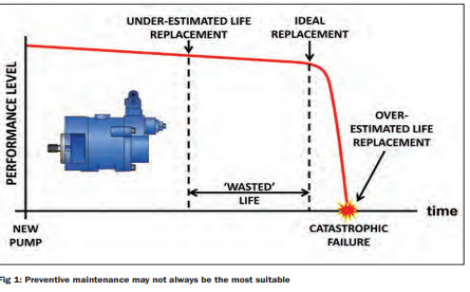
Martin Cuthbert, Webtec’s Managing Director says there are seven good reasons why it makes sound business sense to monitor hydraulic flow on mobile machines. H&P reports.
Such are the advantages available to both OEMs and end users from the permanent installation of flow monitoring equipment that Martin Cuthbert, Webtec’s Managing Director, sees it as the ‘missing link’ in on- and off-highway hydraulic condition monitoring.
By listening to a large number of customers in the mobile machinery market over the past five years, Cuthbert says Webtec was able to identify seven clear challenges that set the premise for the development of a new hydraulic flow meter which meets the needs of modern hydraulic condition monitoring and delivers considerable business gains. Specifically, the challenges were: minimising unscheduled downtime to save costs, monitoring cycle times to stay abreast of machine health, reducing warranty costs by understanding machine usage patterns, improving energy efficiency to save on fuel, optimising actuator control to enhance certainty, improving machine safety to protect workers and supporting the elimination of live work (ELW).
1. Minimise unscheduled downtime
Installing a flow meter is one of the best ways to monitor pump and actuator performance, allowing engineers to schedule service requirements before the onset of catastrophic failure and enormous costs. Cuthbert explains that a day of downtime for a municipal vehicle could amount to £15,000 a day, while for mining in the precious metals industry, costs can sometimes top £50,000 an hour.
Sure enough, hydraulic machine condition monitoring is not new, but in historical terms many considered ‘flow’ too difficult, so most machines rely on pressure measurement as it is relatively simple to perform. However, pressure is not always useful in locating a fault. For example, suppose a cylinder in normal operation takes 5 seconds to travel full stroke and the applied load creates an operating pressure of 60 bar. If a fault occurs, caused perhaps by a loss of pump flow or circuit leakage, the reduced flow would cause the cylinder piston to move slowly, but it would still lift the load. If the load lifts then the pressure must still be 60 bar, so the pressure gauge would read the same as normal.
Instead, to diagnose a problem with actuator speed (too much or too little) it is necessary to measure flow rate. Such an approach can help pinpoint situations such as: insufficient flow caused by pump wear; excessive return or drain line flow prompted by increased component leakage; or a mismatch between actuator flow rate and speed (indicating a loss of volumetric efficiency of the actuator).
As a result, hydraulic flow testers and data loggers are ideal tools says Cuthbert in preventative maintenance strategies. Here, scrutinising pump health periodically helps to estimate remaining life and ensure replacement before catastrophic failure, while simultaneously avoiding the waste of any useful pump life.
Fig 1: Preventive maintenance may not always be the most suitable
Cuthbert comments that preventive maintenance is a useful and practical procedure wherever there is robust documentation of component service life data and operating conditions are predictable. However, the reality for most on-and off-highway mobile machines is somewhat different. Factors such as vibration, temperature swings, shock and unstable power supply can lead to unexpected events and sudden failures.
Practicality, says Cuthbert, therefore suggests that continuously monitoring hydraulic performance via a permanently mounted flow meter will immediately detect any sudden deterioration and prompt appropriate action. Furthermore, with the right flow monitor it becomes possible to transmit data to the cloud via the vehicle’s CANbus network. Users can subsequently record and analyse performance data remotely and predict problems before they arise, with alarms highlighting any sudden changes.
Cuthbert highlights that Webtec’s newly developed CTA series turbine-type flow monitor with CAN bus interface fulfils this exact purpose. Developed in close collaboration with customers, the CTA series monitors both flow rate and temperature at high operating pressures, transmitting data via an SAE J1939 CAN bus found commonly on many vehicles. IP69K-rated for use in harsh operating conditions and fully EMC compliant, this compact, rugged flow monitor is an invaluable instrument that enables maintenance engineers to monitor system performance and schedule remedial service only when necessary rather than at estimated intervals.
Importantly, the new CTA is easy to integrate with IoT solutions and is currently in use at over 10 customers in sectors that include mining, municipal, agriculture and screening/crushing, deploying many different CAN buses and controllers.
2. Track cycle time to indicate machine health
With the CTA flow meter permanently installed, Cuthbert says that a number of further benefits arrive from the continuous monitoring of machine health and operational parameters. Monitoring cycle times, in particular, can highlight a gradual loss of productivity long before this becomes an issue or leads to a catastrophic failure.
Cuthbert says that assuming an overall machine cost of £300 per hour, a 5-hour job will cost £1500 at 100% efficiency. However, a machine that is only 80% efficient means the same 5-hour jobs now needs 6.25 hours, suddenly costing £1875. A machine operating 5-10% slower is hard to see without monitoring the pump’s power output. For OEMs, this tactic supports the provision of a ‘health monitoring’ subscription service and provides extra detail and confidence around scheduling future maintenance.
3. Reduce warranty costs
Combining flow and pressure data, says Cuthbert, permits the calculation of hydraulic power, which in turn can indicate how ‘hard’ a machine is working – whether due to operator behaviour or the ‘hardness’ of the earth or rock. These usage patterns relate directly to wear and can feed into a ‘power by the hour’ business subscription model. This type of data can also prove invaluable when deciding warranty claims.
4. Monitor drive motor efficiency to save fuel
Cuthbert also explains that for actuators that operate continuously over long periods, such as those found on conveyor or mixer drives, comparing the actuator flow rate to the actuator speed will establish its volumetric efficiency. He adds that any deterioration in efficiency will therefore signal the need for remedial action. In addition, this approach takes into account any leakage from the inlet port to the outlet port that would not be obvious simply by monitoring the case drain flow.
Such a strategy is also applicable to the overall machine. If the engine is only driving hydraulics, then measuring the hydraulic power output will reveal the power output of the entire machine, which indicates how long the fuel/battery will last.
5. Improve certainty with closed-loop speed control
Using closed-loop feedback will help to optimise flow control, says Cuthbert, particularly where an actuator is operating in a hostile environment. Where actuators function in challenging conditions, possibly subject to rain or salt water, electrical discharges or lightning strikes, or extreme temperatures, monitoring and transmitting the actuator speed by electrical sensors and cabling may prove problematic.
Instead, Cuthbert comments that a feedback signal proportional to the actuator speed is obtainable by monitoring the actuator flow rate, which is then suitable for use in the closed-loop speed control system of the actuator. This signal can relay back to the proportional hydraulic flow control valve, with flow adjusted accordingly.
6. Enhance safety
Cuthbert highlights that any mobile machine with hydraulic flow presents a safety risk if someone inadvertently opens a cover, for example. Normal practice here is the use of trip switches, but these are not tamper-proof. Flow monitoring is a good back-up strategy.
By monitoring pump flow, the system designer has a built-in secondary safety function with real-time feedback. It is possible to see whether the pump is delivering flow or not by witnessing whether oil is returning to tank or the motor drive. The set-up can subsequently enable/disable other functions to keep operators safe.
7. Elimination of Live work (ELW)
In a continuous drive to improve safety in the heavy machinery industry, Cuthbert comments that OEMs, dealers and operators in the construction & mining industry are increasingly focussed on how such machines can be maintained and repaired without a person having to enter the machine while its operating, hence the phrase Elimination of Live Work. Traditionally, he says, to test a hydraulic pump on a machine you would need two technicians to attend to fit the flow meter into the circuit, and then for one to run the machine while the other monitors the pump performance. By using a permanently installed flow monitor, no additional equipment needs to be installed, so only one person is required to carry out the job and flow rates can be monitored remotely thus removing the technician from a potentially dangerous environment.
*******************************************************************************************************
Webtec is a hydraulic measurement and control company that designs, manufactures and distributes a world-class range of hydraulic components and hydraulic test equipment for the mobile and industrial machinery markets.
The company, whose headquarters are based in St Ives, Cambridgeshire, UK is privately owned and employs around 70 people in the UK, North America, Germany and Hong Kong.
*******************************************************************************************************
For further information visit www.webtec.com
https://twitter.com/webtec_products
https://www.linkedin.com/company/webtec-products-limited/
-
SMART Manufacturing & Engineering Week
04 - 05 June, 2025
NEC, Birmingham UK -
PPMA 2025
23 September, 2025, 9:30 - 25 September, 2025, 16:00
NEC, Birmingham UK -
Advanced Engineering Show 2025
29 October, 2025, 9:00 - 30 October, 2025, 16:00
NEC, Birmingham UK