- Home » Editorial » Hydraulics
Fluid power faux pas
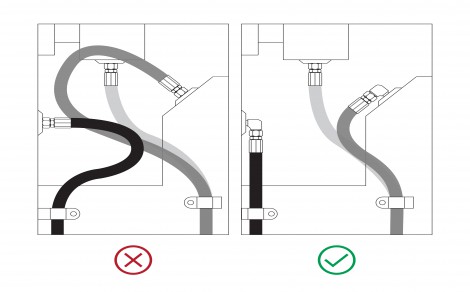
Ignoring signs of wear
Hydraulic assembly inspection should be included in any system preventive maintenance schedule. These inspections should monitor hydraulic assemblies for signs of wear, including cover damage like cracking and abrasion. Ideally, the system design would reduce the likelihood of damage, but when this damage is found to reach the hose reinforcement, the assembly must be replaced.
Cover cracks can be caused by several issues. Exposure to extreme heat, particularly in engine compartments, can cause the exterior cover of the hose to become brittle and crack. Exposure to ozone, either from the sun or from high electrical charges, such as in welding equipment applications, can cause micro-cracks to appear on the surface of the hose. This is similar to ‘weathering’ that is seen in the sidewalls of tires. Ozone damage is typically seen first on the exterior of hose bends where the rubber compounds see their highest stresses. Once these cracks reach the hose reinforcement, the reinforcement is compromised because of potential damage due to moisture and debris. This damage can be mitigated by protecting hoses from high-electrical exposure and by choosing hoses with materials that are resistant to ozone.
Cover abrasion is a constant challenge – particularly in congested hydraulic systems where it is challenging to isolate one hose from others or the machine frame in dynamic applications. The most obvious way to mitigate abrasion damage is to choose hose covers that are specially formulated with abrasion resistance. Specialised nitrile rubber compounds offer a mid-grade level of abrasion resistance, and extreme resistance to abrasion can be realised with a hose cover made of ultra-high molecular weight polyethylene film. It is also possible to assemble the hose in an abrasion-resistant sleeve or hose guard, but this option considerably increases the assembly costs and can complicate hose installation in the application. In addition to selecting abrasion-resistant hose covers or accessories, the hose routing can also have an impact on hose abrasion. Use clamps to support long hose runs or to keep hoses away from moving parts, taking special care to allow for volumetric expansion. Hoses that bend around a portion of the machine frame should be assembled with enough length to avoid rubbing over a machine corner. And it’s worth noting that hoses should never be clamped to the machine frame, which could restrict expansion in the curves when the hose is pressurised.
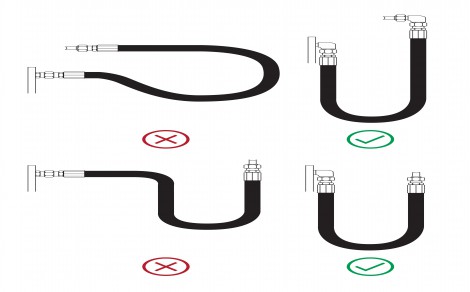
Proper assembly
A user can procure the most premium and highest performing hoses and couplings in the world, but if they’re not assembled correctly then they’ll never realise the value. Proper assembly has several components – qualified hose-coupling interface, assembled by a trained technician, and with a verified crimp diameter.
By qualified hose-coupling interface I mean that the specific hose and specific coupling are verified to work together. The verification is more than just crimping to a certain crimp diameter – it should be verified by burst and impulse testing across a range of crimp diameters to account for hose and coupling manufacturing variation as well as crimper and die tolerances. The testing should mimic the intended application, particularly the temperature. A hose-coupling interface may work well at standard 100degC operations and then not perform at all at elevated temperatures above 120degC. Further, hoses are not all the same. Even though hoses from different manufacturers may meet the same performance criteria, the properties of the compound affect the robustness of the hose-coupling interface.
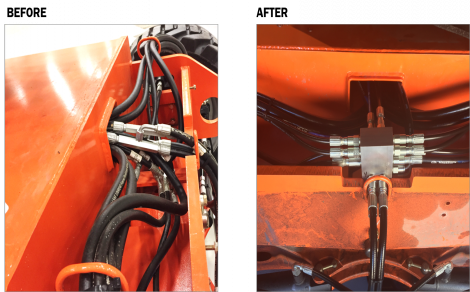
-
PPMA 2025
23 September, 2025, 9:30 - 25 September, 2025, 16:00
NEC, Birmingham UK -
Advanced Engineering Show 2025
29 October, 2025, 9:00 - 30 October, 2025, 16:00
NEC, Birmingham UK