- Home » Editorial » Hydraulics
Fluid power faux pas
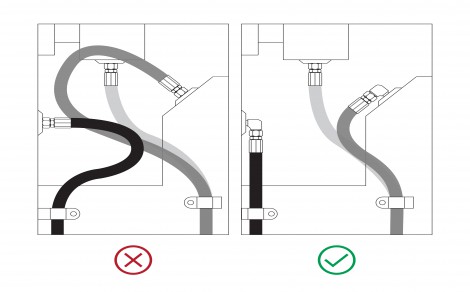
The fact that hoses are flexible is a common reason a hose is chosen instead of a rigid tube, but that doesn’t mean that hoses are ultimately flexible. Common issues arise where hoses must bend – particularly bends near the coupling. Optimised hose routings will avoid hose bends near the coupling by using angled adapters, or alternative coupling options, to alleviate hose flex requirements. If a bend radius is below the recommendation for that particular hose, get creative with angled adapters and/or revisit your coupling selection to avoid sharp bends.
Proper routings also mitigate hose abrasion, whether against other hoses or against machine components, which also extends system life and minimises the risk of premature failures. Return lines are another component of the hydraulic system where we often see problems – although these lines are typically low pressure, they are a necessary component to return fluid to a reservoir, but they are often the last component considered when designing a system. To mitigate the risks of challenging routings, consider a flexible, corrugated hose design that has a tighter minimum bend radius, like Gates Multi Master GMV MegaFlex.
Finally, hose routings can minimise the likelihood of leaks in a hydraulic system with proper termination selection. Always avoid stacking adapters to both minimise system cost and the risk of system leaks. To further demonstrate the value in optimised system routings, the product application engineers at Gates provided case studies to illustrate these points. In this first example, the customer asked for Gates’ help because they were having difficulty routing hoses through a channel in the Rear Drive. Upon further inspection, Gates engineers found a few opportunities:
What Gates Engineers Observed Optimised Solution
Tee grouping created challenges routing hoses through the channel Replace Tees with a manifold.
Manifold design provided fixed points of reference for routing and improved aesthetics on the machine, plus they eliminate abrasion concerns from bundled tees.
Bundled Tees were creating abrasion concerns
4+ connections at the same point were difficult to install. Gates QuickLok connections minimise leaks and enable fast and easy assembly.
The before-and-after photos (3 and 4) show a cleaner system with improved performance and fewer leak points.
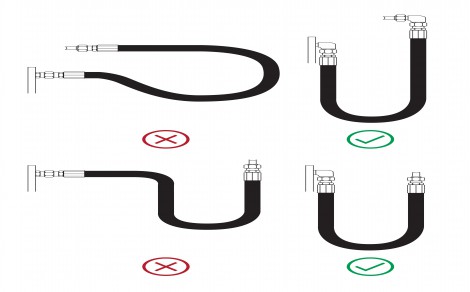
Forgetting about safety
Mistakes with high-pressure hydraulics can lead to critical injuries or even death. Here are some critical safety reminders about hydraulic systems and hydraulic hose assemblies:
1. Never touch a pressurised hydraulic hose. Rubbing your hand along a hose as a leak-detection technique, for instance, is just asking for trouble.
2. Similar to electrical systems, hydraulic systems can be energised even when the system appears to be in the ‘off’ setting. Therefore, always de-pressurise a hydraulic system prior to handling or replacing any system components.
3. When replacing a hydraulic assembly, always ensure the replacement assembly can meet the system performance requirements, including working pressure, temperature and fluid being conveyed.
4. For hydraulic hand tools, never carry the hand tool by the hose. This can lead to pinching and pinholes.
5. For line-of-sight hydraulic lines where an operator is working near the pressurised hydraulic assembly, line-of-sight sleeving should be used to protect the operator in the case of hose or assembly failures.
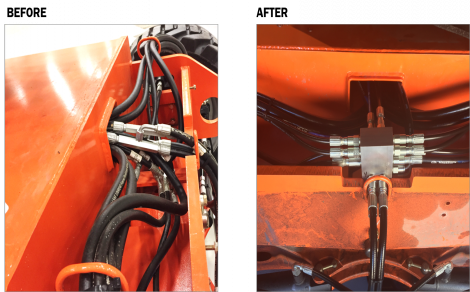
-
PPMA 2025
23 September, 2025, 9:30 - 25 September, 2025, 16:00
NEC, Birmingham UK -
Advanced Engineering Show 2025
29 October, 2025, 9:00 - 30 October, 2025, 16:00
NEC, Birmingham UK