Multi-axis motion controller synchronises press operation
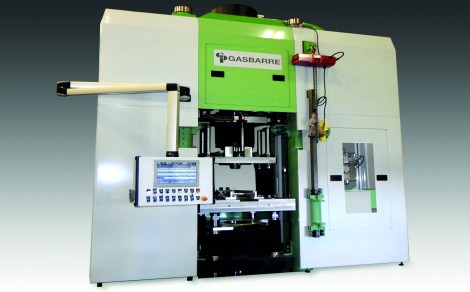
Gasbarre designed the hydraulic circuits to provide high flow to the cylinders for speed but allow a smaller valve to be used for very accurate positioning. The main upper cylinder is able to achieve speeds of 14 inches per second during a rapid move and still position within .0002”. To control the hydraulic circuits on this machine requires 15 separate tasks running simultaneously to smoothly handle the throttling of the various hydraulic valves.
Selecting the motion controller
When selecting a motion control solution to perform these functions, Gasbarre’s management wanted to use just one multi-axis controller. “Using a single motion controller makes system development and troubleshooting much easier,” said Larry Shindledecker, Gasbarre engineer. In addition, Gasbarre needed a controller with high performance and high precision operation. “We are travelling at 10 inches per second and we need to establish our target position to +/- .0005in.,” said Shindledecker.
Gasbarre has been using controllers from Delta Computer Systems, Inc. of Battle Ground, Washington for fifteen years. “We started with the RMC100 and migrated to the RMC150,” said Shindledecker. “When we needed more axes than we could fit into the eight-axis RMC150, we switched to the RMC200, which can handle up to 32 axes.”
A strength of the RMC200 (Figure 3) is the ability to connect to a large number of input transducers. In the case of the new Gasbarre press design, the motion controller connects directly to 17 high-precision pressure transducers and seven linear position transducers with SSI (synchronous serial interfaces) and .5 micron resolution. It also connects to one rotary SSI transducer and one load cell. Sixteen of the pressure transducers are paired one on either side of the piston in each of the eight cylinders to measure the force that is being applied (the difference between the pressure readings corresponds to that cylinder’s force). “In addition to measuring force, we are monitoring pressures for diagnostics,” said Shindledecker. “The Delta controller makes a great tool for troubleshooting when everything can be recorded and graphed together.” “With the added monitoring we will have more data available to assist in future upgrades and better utilisation,” adds Heath Jenkins, President of Press and Automation Business at Gasbarre.
Besides the pressure transducers, the upper cylinder is fitted with a load cell for the purpose of reading the compaction force that it delivers. Gasbarre’s experience is that the load cell provides more accurate force readings than using pressure transducers in cylinders, without needing to worry about external influences like seal friction.
Programming the motion
The motion programming and tuning was done using Delta’s RMCTools interface. The software uses drop-down menus and fill-in boxes on screen to program the motion sequence for each axis. “The Delta synchronization commands are straightforward and easy to work with,” said Shindledecker. “Most of the other motion controllers I have used are less intuitive.” For example, developers can work directly with gear ratios, timing and rates of acceleration and jerk (i.e, the rate of change in acceleration) without needing to do low-level machine programming.
-
PPMA 2025
23 September, 2025, 9:30 - 25 September, 2025, 16:00
NEC, Birmingham UK -
Advanced Engineering Show 2025
29 October, 2025, 9:00 - 30 October, 2025, 16:00
NEC, Birmingham UK