Multi-axis motion controller synchronises press operation
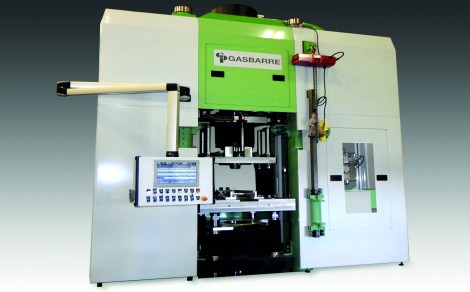
Gasbarre Products, Inc. of Dubois, PA, USA makes powder compacting presses in a variety of sizes, capable of exerting compaction forces from 1 to 750 tons. Most of the company’s customers are suppliers to the auto, lawn and garden, hand tool, and recreational vehicle industries. Gasbarre’s presses are used to form complex shapes from metallic and ceramic powder compounds, which are hardened through a high-temperature sintering process after forming.
The size of a press is determined by the part face area and the compaction force of the material, but a common requirement is a need for multiple motion axes to accomplish the compression operation. For example, the following table contains an accounting of the axes involved in a new powder compacting press design (Figure 1) developed by Gasbarre:
Axis Function
Upper Ram The upper cylinder that creates the primary downward pressing force.
Upper #2 Second upper punch used for creating a hub or counter bore on the top of the part.
Die Table Contains the die for the outside diameter of the part. It will move up for die filling, down during the molding process, and down to eject the part.
Lower #1 Holds the first of three lower punches. The lower punches create different features on different levels on the bottom of the part. It will move up for filling, down during the molding process, and down to eject the part.
Lower #2 Same function as Lower #1
Lower #3 Same function as Lower #1
Core Rod An additional lower punch for creating a counter bore or thru hole from the bottom of the part.
Filler Shoe Controls a servo motor for this application which is used to deposit material into the die. An SSI rotary encoder is used to coordinate motion between the filler shoe and the die table.
Press operation
Figure 2 shows a manufactured part produced by the new press. Though it requires multi-axis compression to form, it is not as complex as parts which could be produced by the machine. During a compression cycle the axes will typically switch between geared, synchronised, and independent motion control at various times. This is all in an effort to consistently move the powder material into the machine and then transfer it within the die, so that when the part is molded, the density of each level stays within design specifications.
When decompressing the part, deflection compensation must be done on the various tool members because, depending upon the surface area of the punches, they will deflect differently. Without deflection compensation, as the tooling decompresses, the punches could spring back at varying rates, causing cracks in the part.
The next challenge is to extract the part from the die. The machine must have enough flexibility in speed, position control, and sequencing to eject the part from the die without creating any stress on the part which would result in cracks.
Gasbarre designed the hydraulic circuits to provide high flow to the cylinders for speed but allow a smaller valve to be used for very accurate positioning. The main upper cylinder is able to achieve speeds of 14 inches per second during a rapid move and still position within .0002”. To control the hydraulic circuits on this machine requires 15 separate tasks running simultaneously to smoothly handle the throttling of the various hydraulic valves.
Selecting the motion controller
When selecting a motion control solution to perform these functions, Gasbarre’s management wanted to use just one multi-axis controller. “Using a single motion controller makes system development and troubleshooting much easier,” said Larry Shindledecker, Gasbarre engineer. In addition, Gasbarre needed a controller with high performance and high precision operation. “We are travelling at 10 inches per second and we need to establish our target position to +/- .0005in.,” said Shindledecker.
Gasbarre has been using controllers from Delta Computer Systems, Inc. of Battle Ground, Washington for fifteen years. “We started with the RMC100 and migrated to the RMC150,” said Shindledecker. “When we needed more axes than we could fit into the eight-axis RMC150, we switched to the RMC200, which can handle up to 32 axes.”
A strength of the RMC200 (Figure 3) is the ability to connect to a large number of input transducers. In the case of the new Gasbarre press design, the motion controller connects directly to 17 high-precision pressure transducers and seven linear position transducers with SSI (synchronous serial interfaces) and .5 micron resolution. It also connects to one rotary SSI transducer and one load cell. Sixteen of the pressure transducers are paired one on either side of the piston in each of the eight cylinders to measure the force that is being applied (the difference between the pressure readings corresponds to that cylinder’s force). “In addition to measuring force, we are monitoring pressures for diagnostics,” said Shindledecker. “The Delta controller makes a great tool for troubleshooting when everything can be recorded and graphed together.” “With the added monitoring we will have more data available to assist in future upgrades and better utilisation,” adds Heath Jenkins, President of Press and Automation Business at Gasbarre.
Besides the pressure transducers, the upper cylinder is fitted with a load cell for the purpose of reading the compaction force that it delivers. Gasbarre’s experience is that the load cell provides more accurate force readings than using pressure transducers in cylinders, without needing to worry about external influences like seal friction.
Programming the motion
The motion programming and tuning was done using Delta’s RMCTools interface. The software uses drop-down menus and fill-in boxes on screen to program the motion sequence for each axis. “The Delta synchronization commands are straightforward and easy to work with,” said Shindledecker. “Most of the other motion controllers I have used are less intuitive.” For example, developers can work directly with gear ratios, timing and rates of acceleration and jerk (i.e, the rate of change in acceleration) without needing to do low-level machine programming.
“Initially, I had some concerns with utilising the more complex features of the RMC like camming and advanced gearing,” said Shindledecker. “But I made a trip to the Delta factory and worked with a Delta engineer for a week on this project. This was very helpful.”
The same RMCTools environment supports all of Delta’s current RMC motion controllers. “The software compatibility between the RMC150 and the RMC200 work out very well,” said Shindledecker. “It helped us reduce the programming time required for this product by letting us re-use motion steps in newer machines that we’ve used before.” RMCTools is also useful for troubleshooting, with a key component of the package being the Plot Manager. This is a tool that allows various motion parameters such as axis position, velocity, and hydraulic pressure to be plotted in real time and compared with target values produced by the control algorithm. The output is displayed on the screen of an attached PC or saved in a file for later review or archiving purposes.
Besides actively controlling motion axes, Delta motion controllers can connect to additional transducers for the purpose of monitoring other status points on the machine. “The RMC200 has now given us what we have been asking for,” says Jenkins. “With up to 32 axes available we can now control all of our hydraulic axes plus gather diagnostic information.”
“The functionality of this machine would be extremely difficult to accomplish without the use of the Delta RMC200,” concludes Shindledecker.
-
PPMA 2025
23 September, 2025, 9:30 - 25 September, 2025, 16:00
NEC, Birmingham UK -
Advanced Engineering Show 2025
29 October, 2025, 9:00 - 30 October, 2025, 16:00
NEC, Birmingham UK