Retrofitting pumps for a new role
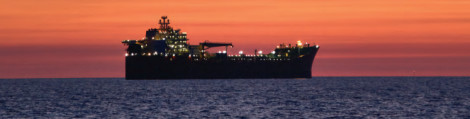
Retrofits offer significant benefits over pump replacement. Financial savings equate to approximately 10% of the cost of a new pump. However, money isn’t everything, time is often the priority. With its global engineering facilities, Sulzer says it delivers a pump retrofit in around six weeks.
Double duty
Equally important are pump efficiency and reliability. To attain optimum application performance, pumps need fine-tuning. In this case, two duty points were required – flows between 330 m3/hr and 387 m3/hr with a differential head of 1750 m as well as a low flow, high pressure point of 104 m3/hr at 1960 m head.
To achieve the best solution, Sulzer proposed a pump de-staging, removing four of the eight stages. Super Duplex stainless steel de-staging tubes will guide the flow between the remaining impellers, preventing turbulence and maintaining efficiency.
The reduction in output also equates to lower power input. Here, the original fixed-speed, 11 kV, 5.5 MW motor could be replaced with a 3 kV, 3.5 MW unit controlled via a variable speed drive. Power will be reduced from 4.5 MW to 1.8 – 2.0 MW, depending on operating conditions, while motor efficiency will increase from 96.4% to 96.9%, providing considerable energy savings. This reduces carbon footprint, important when governments are imposing environmental taxes based on carbon emissions.
Measure twice, fit once
The reduction in motor power and discharge head enabled many original components to be retained, but a new lateral analysis of the de-staged unit was conducted, confirming the pump rotor stability throughout the operating speed range.
Due to the reduced speed of the new electric motor, the lube oil system output had to increase. A modification of the lube oil pump increased output by 30%, satisfying the demand of the pump, gearbox and motor.
Pipework also needs to be approached carefully to avoid costly reworks on site. This can be achieved cost-effectively by using pipework with ‘green ends’ allowing it to be cut and welded in position on site, achieving a perfect fit. An alternative is to deliver the pipe and fittings to all the pipework to be fabricated on site.
Taking advantage of retrofit
Using updated equipment that fits back into the original footprint and performs at the best efficiency point has clear benefits.
In many cases, time is of the essence and with refits being completed in dry docks, it’s important to minimize the project time. A well-planned retrofit project can be completed within six weeks and minimizes changes to surrounding pipework and infrastructure.
There are also environmental advantages. Retaining most of the components means the original asset isn’t disposed of, producing less waste. In the previous case study, the electrical motor was the only major item that wasn’t reused and instead recycled. Moreover, retrofits require much less energy and materials, maximising sustainability and contributing to environmental, social and corporate governance (ESG) goals.
https://www.linkedin.com/company/sulzer/
-
PPMA 2025
23 September, 2025, 9:30 - 25 September, 2025, 16:00
NEC, Birmingham UK -
Advanced Engineering Show 2025
29 October, 2025, 9:00 - 30 October, 2025, 16:00
NEC, Birmingham UK