Retrofitting pumps for a new role
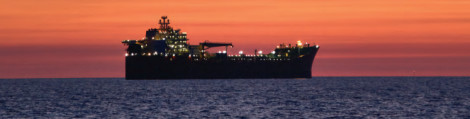
Floating production storage and offloading (FPSO) vessels are used for processing oil and transferring it to tankers or pipelines. Positioned close to an oilfield, they remain there until the field is exhausted. Originally designed with a service life of over 20 years, FPSOs represent a huge investment for international oil companies (IOCs) and to maximise their potential, they are refitted and relocated once a project is completed. H&P reports.
With sustainability paramount for modern industry, refurbishment projects support corporate goals by enabling the reuse of components, rather than installing all-new equipment, which requires more resources and investment.
Research carried out by a major IOC compared the investment value for new equipment with the final value of the project, and found that for offshore locations, project costs were five to seven times the investment. Therefore, the final cost of installing a new USD 5 million pump on an FPSO could be between USD 25 and 35 million.
In contrast, retrofitting existing equipment would equate to approximately 60% of the new pump price. Considering that it will be reinstalled without further modifications, there are no additional costs. Comparing total project costs makes the retrofit investment just 10% of the whole project to install a new pump in an offshore situation.
Extending equipment life while realising carbon reductions
Relocation projects begin with establishing a scope of works for vessel upgrades. Improvements can be achieved via new equipment or modifying existing assets. However, every solution must be capable of delivering a service life dictated by the contract – typically 20-25 years.
Central to an FPSO are the water injection pumps which pressurise the well and maximise its productivity. It’s imperative that all pumps and auxiliary equipment are refurbished to the highest standard.
Sulzer research has shown that within the upstream business, production platforms account for 82% of CO2 emissions and of these, water injection pumps are responsible for 50% of the power requirement. Therefore, optimising equipment for the new application and upgrading pump efficiency can significantly impact carbon footprint and operational costs.
Case Study
In one project for example, Sulzer says that an FPSO is being prepared for relocation to the North Sea. When the vessel was built, the company supplied three water injection pump packages: 8-stage pumps designed to deliver 3’500 m head with a flow rate of 350 m3/hr using a 4.5 MW motor.
Before relocation, the vessel must undergo a refit. For example, an additional 20 m of height will be added to the bow to handle waves in the North Sea. All work will be carried out in a dry dock and as the original equipment manufacturer (OEM) of the pumps, and a leading retrofit expert, Sulzer is contracted to deliver the modifications.
-
Smart Manufacturing & Engineering Week
05 - 06 June, 2024
NEC, Birmingham -
HILLHEAD 2024
25 June, 2024, 9:00 - 27 June, 2024, 16:00
Hillhead Quarry, Buxton, Derbyshire UK