- Home » Editorial » Hydraulics
Reasons for the growing interest in Zero Liquid Discharge technology
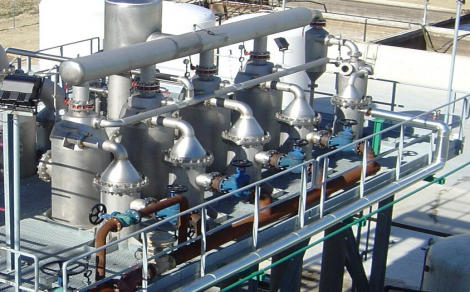
1 https://www.prnewswire.co.uk/news-releases/zero-liquid-discharge-market-is-estimated-to-rise-at-a-cagr-of-11-95- during-the-forecast-period-notes-tmr-study-866877417.html
2 Tong, T. & Elimelech, M. (2016) The Global Rise of Zero Liquid Discharge for Wastewater Management: Drivers, Technologies, and Future Directions in Environmental Science & Technology. Available at https://pubs.acs.org/doi/ 10.1021/acs.est.6b01000
*******************************************************************************************************
Depending on the product to be concentrated, HRS says it can select from a series of technologies for designing the most optimal ZLD process. Energy optimisation methods (multistage, TVR, MVR) can be combined with several types of heat transfer technologies (plate evaporators, corrugated tube evaporators, scraped surface evaporators). Whatever the technology applied, the overall process can be separated into three steps:
1. Evaporation / concentration: The product is concentrated to just below its maximum concentration (saturation). The evaporation plant is usually a multistage evaporator setup.
2. Cooling: if the maximum solubility curve is steep (large concentration at high temperature, low concentration at low temperature), the product obtained in step 1 is cooled, provoking immediate precipitation of dissolved solids.
3. Crystallisation: Crystallisation / sedimentation of the solids produced in step 2 occurs in specially designed crystallisation tanks. A supernatant layer of concentrated solution remains after this stage and is returned to step 1 for reprocessing.
For products without a steep solubility curve, it is necessary to concentrate inside the evaporator to above the maximum solubility. This means that the step 1 process is equipped with a final evaporator stage (finisher) that is specially designed to work with suspended solids. The fluid with suspended solids is then transferred directly to the crystallization tanks in step 3.
The brine cooler and evaporator finisher work with solids in suspension and often this means dealing with fouling products. A typical HRS evaporator / finisher will use Unicus scraped surface evaporators that are self-cleaning and maintain optimal evaporation rates. Typically, our R series scraped surface coolers are used for cooling the saturated brines that are sent to the crystallisation tanks. The result is an efficient process which can work continuously without requiring scheduled downtime
*******************************************************************************************************
https://www.linkedin.com/company/hrs-heat-exchangers/
-
PPMA 2025
23 September, 2025, 9:30 - 25 September, 2025, 16:00
NEC, Birmingham UK -
Advanced Engineering Show 2025
29 October, 2025, 9:00 - 30 October, 2025, 16:00
NEC, Birmingham UK