- Home » Editorial » Pneumatics
Five ways to optimise pneumatic systems design for food & beverage packaging applications
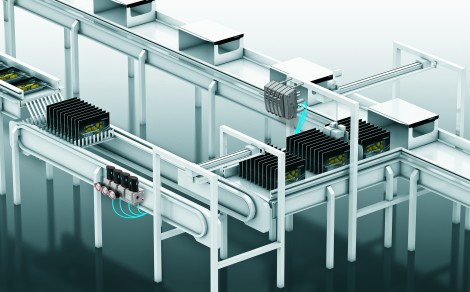
Tip 3: Do not exhaust valves over the food zone
Exhausting a valve over the food zone is similar to holding a blow gun and blasting unfiltered air directly into the food or packaging. The only difference is that rather than the air coming directly from the compressor, air exhausted from the valve has also passed through the valves, into and out the cylinder, and back through the valve, which risks picking up contaminants along the way. Either mount the valves below the food/packaging zone or mount them above and duct the exhaust below the food zone.
Check valves are often overlooked in the food zone. While check valves can help improve machine cycle time because the air does not exhaust back to the valve, this means the air is exhausting over the food zone. If a check valve must be used, the exhaust should be ducted below the food zone.
Tip 4: Shorten tube length between valve and cylinder
One of the most important developments of the last several years has been machine mountable valve manifolds rated at IP69K washdown that, like washdown cylinders, conform to clean-design principles. The elimination of cracks and crevices reduces cleaning time for faster changeover and improved machine availability
The new ability to move the manifold from the control panel to the machine in the food zone cylinder delivers advantages, not the least of which is energy savings. Figure 1 shows the dramatic energy cost saving of moving a manifold out of the panel and closer to the cylinder: 50% in this example.
The shorter the tubing length between valve and cylinder, the faster and more repeatable the cylinder’s cycles. Faster cycles improve performance (see Figure 2). In many applications, such as filling, more precise cycles achieve better control of the process leading to higher consistency in product volume and weight and less waste.
The trend today is for smaller machines. Mounting valve manifolds on the machine allows control cabinets to be smaller or eliminated altogether, which can significantly reduce both cost and footprint. Moving the valve manifold outside of the control cabinet also eliminates pneumatic connections installed into the wall of the control cabinet, lowering machining costs in materials and labour as well as reducing the number of components required.
Tip 5: take advantage of new technologies
There are new opportunities for achieving both the benefits of on-machine mounting and greater control flexibility. The Festo MPA-C IP69K-rated manifold, for example, can be configured with supply and exhaust ports on each valve slice. All ports for every position can be completely independent of the valve next to it. For complex pneumatic situations where several different pressure zones are used, this can be one of the most cost-effective solutions.
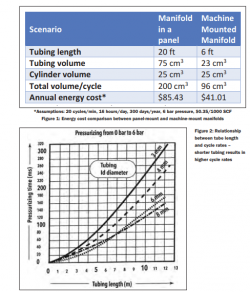
For some applications, the designer may face the choice of either locating an adjustment point for easy access in a panel or on the machine where it may be difficult to adjust. The latter means losing all the advantages of machine mounting. The MPA-C allows the OEM to plumb each valve slice to a pressure regulator. This solution achieves both objectives: easy adjustment and machine mounting.
Final thoughts
There are other design considerations for food and beverage packaging applications such as selecting tubing materials that withstand harsh chemicals and resist plastic transfer to food. Hydrolysis-resistant polyurethane (PUNH) and Polytetrafluoroethylene (PTFEN) tubing are ideally suited for use in the food and beverage industries. Both resist cleaning agents, microbes, and hydrolysis and are FDA compliant. PUNH is more flexible and economical, while PTFEN is ideal for the harshest environments.
Designers can use one of the many free online tools offered by Festo to size the pneumatic system appropriately so that the system runs as energy efficiently as possible. And of course, specifying air filtration units to achieve 0.01 µm filter with 99.9999% efficiency is a must. It is the five tips, however, that lay the foundation for compliance, utilisation, and performance in food and beverage packaging applications.
https://www.linkedin.com/company/festo-uk-ireland/
-
Farnborough International Airshow
22 - 26 July, 2024
Farnborough International Exhibition & Conference Centre