Selecting the right pneumatic conveying equipment
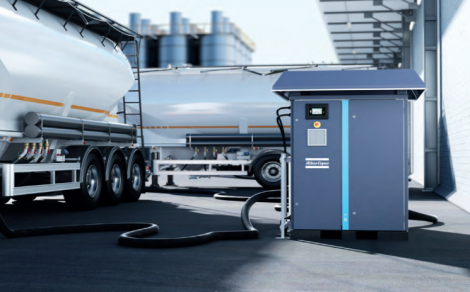
Secondly, in the dense phase, the material is pushed (or sucked in the case of negative conveying) through the pipeline. That means it moves more slowly and requires higher pressure, usually above 2.5 bar. The dense phase is, therefore, more complex, expensive, and requires more energy. Finally, the transient phase is between the dilute and dense phases. Some material is ‘flying’ through the pipeline, and some are moved along the sides - again, impacting pressure requirements.
These phases are critical because powders, granules and dry bulk come in various forms with varying compositions. By fully understanding the make-up of the specific material – whether flour, sand, sugar, grain, plastic, cement, or fly ash - it is possible to select the correct technical specification for the pneumatic conveying system, ensuring it is rightsized for the task at hand. Getting the selection right can guarantee product quality, avoid blockages, minimise the risk of combustion, and reduce operating costs.
Choosing the right equipment
Once the primary material for transportation is identified and its composition fully understood, it is time to select the required compressed air components for the pneumatic conveying system. This process involves a grasp of how blowers, aftercoolers, dryers, and filters work together to optimum effect.
The starting point is the blower or compressor. As previously mentioned, dilute phase conveying is a low-pressure application requiring only an air pressure of 2.5 bar or less. On the other hand, a higher pressure would be required for dense–phase conveying, but sometimes this can still be met by a lowpressure compressor. Indeed, this is an area where many organisations make costly mistakes. Oversizing the compressor or blower will increase initial capital outlay and will result in higher energy usage over time, hurting the bottom line. It is, therefore, crucial to request accurate sizing from an equipment supplier before selecting the type of compressor.
Blowers and compressors also come in many different types. These include oil-free lobe blowers, oil-free screw blowers, oilfree claw blowers, oil-free screw compressors, and oil-injected screw compressors. Again, each type of equipment offers its performance, size, and cost benefits. Oil-free configuration is a critical specification for the food and beverage sector because it reduces the risk of compressed air contamination. This technology ensures that no oil used as a lubricant can enter the airflow and contaminate the food being pneumatically conveyed.
Then there are ancillary components to be considered. Aftercoolers protect pneumatic systems by keeping the air temperature below a specific limit. This factor is significant when conveying products that could be burned, such as sugar, or combusted, such as grains. In addition, some organisations might also be subject to local and national safety standards for high explosion-risk areas or processes. Here, the compressed air must be kept below a specific temperature to avoid combustion. While some compressors have integrated aftercoolers, blowers generally do not, so they must be installed separately. To meet this requirement, air-cooled and water-cooled aftercoolers are available – but an additional consideration comes into play. If a water-cooled model is selected, there might also be a need for a chiller, which lowers the temperature of the cooling water to a consistent level.
-
PPMA 2025
23 September, 2025, 9:30 - 25 September, 2025, 16:00
NEC, Birmingham UK -
Advanced Engineering Show 2025
29 October, 2025, 9:00 - 30 October, 2025, 16:00
NEC, Birmingham UK