Mastering fluid power efficiency with industrial IoT
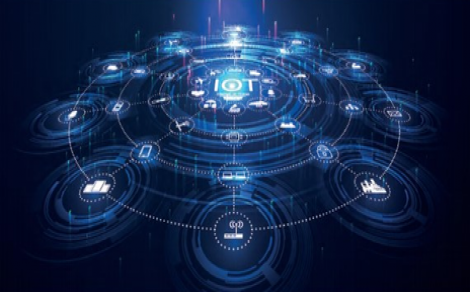
What we see with the IoT is the more that we generate that information back to the OEMs, they can continue to engineer out why this stuff fails in the first place. Because engineers can’t get out into the field and understand how equipment works in the highly varied environments of traditional off-highway or factory floor level machines, generating post installation information back to them allows them to make the smarter design decisions around how their products work.
Establishing real filtration efficiency
Hydraulic filtration preventative maintenance is usually based on a schedule or based on the pop-up indicators that tell you a filter is nearing the end of its life – that as the element continues to collect dirt and water particles, it gets less and less effective and then it ceases to be effective before you need to go into bypass. In this case, the filters could have been used past their effectiveness, thus reducing efficiency. Or, all filters are simply changed out on a schedule, so you’re going to have filters that probably didn’t need to be replaced and you’re wasting money.
What if your filter was actually able to tell you at the exact moment, or maybe 10 or 5% before it reached peak efficiency? If you use smart filtration, you will be replacing the filter at the right time, every time. This has generated at least 33% cost savings for organisations that are deploying system-wide filtration management with the IoT.
What Is lubrication efficiency?
Up next is lubrication – is your fluid working for you as well as it should? There are always opportunities to gain more information around your fluid health. You may take a fluid sample or a color patch test and send it to a lab, and a report is generated. Testing and labs are important pieces of the lubrication management puzzle. But the problem is you can’t just look at one piece of that fluid. The baseline for hydraulic fluid is that it should be clean, cool and dry.
You can keep contaminants out, keep water out, and keep your fluid at the right temperature. But depending on what industry you’re in, you may need to understand more about your additive packages, metal ingress, fluid oxidation, etc. Here, viscosity index is not the only answer. It’s important to consider all factors when trying to achieve lubrication efficiency.
This is why the narrative starts to change when you have more efficient data coming in and you have a bigger, better, broader picture on how to manage your equipment, fleet, factory, floor, whatever it may be. Backing out to this narrative allows you to question you system reliability, preventative maintenance plans, lubrication management, vibration monitoring and even the commodities you use. Stack those on top of each other and you start to get more and more insightful information.
For more information:
https://www.linkedin.com/company/iot-diagnostics/
-
PPMA 2025
23 September, 2025, 9:30 - 25 September, 2025, 16:00
NEC, Birmingham UK -
Advanced Engineering Show 2025
29 October, 2025, 9:00 - 30 October, 2025, 16:00
NEC, Birmingham UK