- Home » Editorial » Hydraulics
The case for electro-hydraulic actuators

Maintenance requirements
In addition to maintenance issues related to the hydraulic fluid itself, hydraulic cylinder systems have additional maintenance demands, which increase as the cylinders begin to wear and leak around the piston. Pumps are also affected by wear, internal leaks and pressure losses of each component, including the conductors, hose and pipes. Electro-hydraulic actuators are selfcontained units which require no maintenance.
Location versatility
Because they don’t need an elaborate support infrastructure, electro-hydraulic actuators make it more effective to move control closer to the point of application. Hydraulic cylinders are far less than ideal for any application that is hard to access. If a cherry picker vehicle designer wants motion control to tilt the bucket, for example, it would be far easier to run electrical wire to up the boom than hydraulic fluid transport tubing. This solution also removes potential concerns about fluid dripping into the environment. A designer of a tractor-hauled seeding unit might output hydraulic lines to the rear of the tractor to control the depth into which the planter cuts to deposit the seed. Replacing that fluid hose with an electric cable has many advantages, such as avoiding costly infrastructure and fluid leakage into a food crop.
Shock loading
Historically, hydraulic technology has been better able to handle sudden shocks, such as the impact of a snow-covered concrete barrier on a cylinder-guided plow blade. However, embedding this technology into electro-hydraulic actuators gives them shock-loading benefits on par with hydraulic cylinders, countering any advantage they might have previously had in this area. Another example of shock handling would be a mower deck running into a large rock. As with the snowplow example, the electrohydraulic actuator would absorb the sudden energy spike instantly by redistributing the fluids throughout the internal valves and pump housing.
Cost effectiveness
Conventional hydraulic systems are most cost effective when they are already specified into a design already containing hydraulic elements, and it is just a matter of adding cylinders to the initial design. Otherwise, there is a cost in designing the support infrastructure and incorporating that into the overall system design. Eliminating fluid handling and storage, leak and spill management, and additional maintenance costs of identifying and repairing leaks can also reduce lifecycle costs for end-users. These benefits are marketable for OEMs and can easily be communicated as advantages to their customers.
Conclusion
For new application designs requiring handling of loads up to 2.180 kg and speeds up to 100 mm (4 inches) per second, electro-hydraulic actuators have significant advantages over hydraulic cylinder-based systems in power density, cleanliness of operation, versatility and lifecycle costs. They also match hydraulic systems in load and shock handling performance.
For morwe information
https://twitter.com/Thomson_Ind
https://www.facebook.com/ThomsonIndustriesInc/
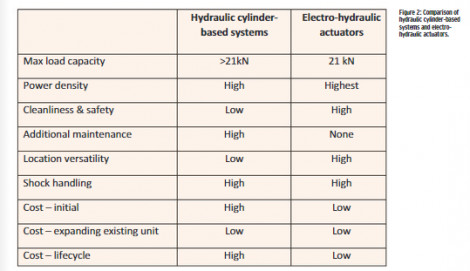
-
SMART Manufacturing & Engineering Week
04 - 05 June, 2025
NEC, Birmingham UK -
PPMA 2025
23 September, 2025, 9:30 - 25 September, 2025, 16:00
NEC, Birmingham UK -
Advanced Engineering Show 2025
29 October, 2025, 9:00 - 30 October, 2025, 16:00
NEC, Birmingham UK