Boardroom Report - Challenges and opportunities
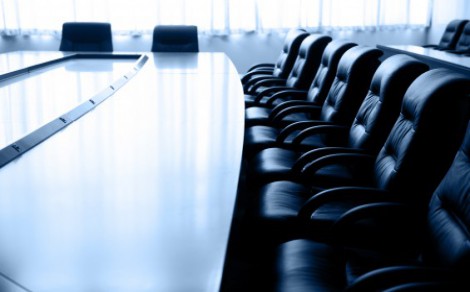
Digitalisation
Andy Parker-Bates, product marketing manager, Festo UK, comments that over the past few years there has been much discussion around Industry 4.0 technologies and the digitalisation of manufacturing detailing how the factories of tomorrow will be seamlessly connected across their supply chains and through their processes and systems. “Customers will be able to configure their unique product and place orders directly on the factory in real-time,” he says. “Autonomous systems will then order raw materials, schedule the build, allocate resources and start the production line running. For much of the UK’s manufacturing industry, this is a utopian future which bears little resemblance to today’s factory floor. It is seen as too difficult to implement and the preserve of large multi-national corporations with huge R&D budgets. What this pandemic has shown, however, is that the principles embodied in digitalisation are more relevant now than ever before and apply equally across the whole of the manufacturing sector.
“Take the FMCG sector as an example. At the start of the pandemic in the UK, we saw supply chains disrupted, a surge in demand and empty supermarket shelves. Many manufacturers responded by reducing the number of varieties they produce to enable them to concentrate on volume production of a smaller range of products, with reduced complexity, fewer changeovers and often with reduced numbers of staff. While this produced the immediate boost the country needed, it demonstrated an inherent lack of flexibility and agility in the manufacturing sector and shows just how far we need to develop to reach the Industry 4.0 vision of the ‘factory of the future’.
“Fortunately, technological shifts already taking place within automation are offering machine builders an ever-increasing range of newer, better connected, more intelligent fluid power products. Products such as IO-link enabled sensors and valves deliver greater operating flexibility and diagnostic insights than ever before and finally bring historically ‘dumb’ field-level devices into the machine control architecture. Access to relatively basic information such as the number of switching cycles of a valve enables maintenance to be scheduled to avoid busy production runs, or manufacturing can be routed to a parallel machine to avoid potential breakdown scenarios. Similarly, an optical sensor with the ability to report the cleanliness of its lens can give advance warning of degradation before it hits production.
“Announcements of the last few weeks hopefully signal some light at the end of the tunnel with respect to COVID-19, and as manufacturers reflect on the events of the past nine months many will be concluding that a greater use of already available automation technologies within their processes could have mitigated many of the challenges that they faced in terms of staff shortages and capacity issues.”
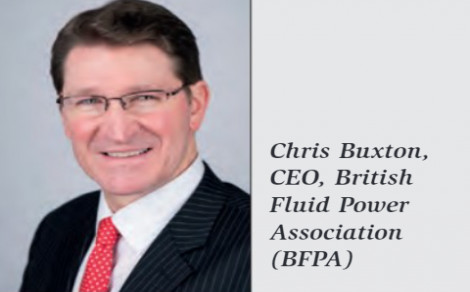
Alexander Pavlov, general manager, Atlas Copco Compressors UK, believes these largely remain energy efficiency and connectivity, on top of reliability. “I believe these days we can also speak about the shift towards green aspects of energy efficiency rather than only financial benefits,” he says. “The latest revolutionary innovation from Atlas Copco is a new generation of oil-free screw compressors (ZR VSD+). Those new compressors consist of two drive trains – low- and high-pressure stages, where each train has a frequency inverter, PM motor and directly coupled oil-free screw element. The controller within the compressor makes sure that the two drive trains run in perfect balance and always at the most efficient operating point. This new generation delivers even more energy savings to our customers, and I am happy to confirm that some of those brand-new models are already installed and running by UK customers.”
As for connectivity, Pavlov states that this is an incredibly exciting journey the company is going through; with more than 3000 Atlas Copco compressors connected in the UK currently. “This provides an enormous amount of intelligence data on how our products are running, and we apply many AI algorithms on that data to prevent technical problems and highlight potential improvements,” he says “Recently, we also introduced a new communication device which can work with any compressor make, not only Atlas Copco units. The current pandemic highlighted the importance of remote connectivity solutions, and we also experienced more high-speed track projects where the time between RFQ and commissioning was incredibly short, for medical and PPE sectors for example.”
Brexit
How is Brexit impacting on the fluid power equipment and systems marketplace? Buxton believes the fact that the EU–UK Trade and Cooperation Agreement (TCA) was announced at such a late stage did little to help companies trying to prepare for the end of the transition period – especially against a backdrop of the COVID-19 Pandemic. “We were all expecting a ‘skinny deal’ but when it was announced it was certainly short on detail in many areas,” he
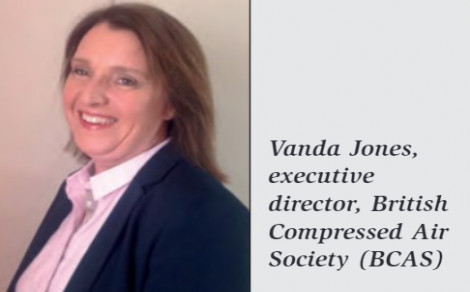
-
PPMA 2025
23 September, 2025, 9:30 - 25 September, 2025, 16:00
NEC, Birmingham UK -
Advanced Engineering Show 2025
29 October, 2025, 9:00 - 30 October, 2025, 16:00
NEC, Birmingham UK