Achieving contaminant-free compressed air in food and beverage operations
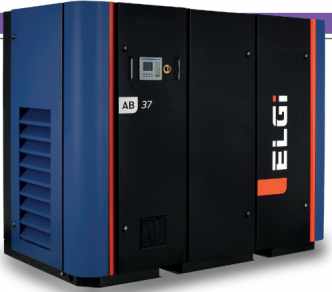
For example, there are very few compressor companies that design their own oil-free air-ends and even less that make them along with their own pressure vessels, castings, motors while also conducting complete machining and compressor assembly. With in-house technology and manufacturing capabilities of all these various elements, compressors can now be engineered to deliver maximum uptime and reliability, leading to an optimised compressed air system for operators.
Designing compressed air for the operational situation = lower life cycle cost + contaminant-free compressed air
The technology exists to affordably cater to the dual demands of contaminant-free air and improved life cycle cost. But we can and should do more. As my example at the beginning of this article highlights, Food and beverage operational leaders need not only the best and most reliable compressors, but also expert support in designing and optimising the complete compressed air system – a trusted partner that will understand and tailor their needs to further improve their twin goals.
Plant leaders should consider a ‘bird’s eye view’ of the compressed air system – understanding the supply and demand sides, and starting in the point of generation, through transmission and finishing, where the air is used at the end of the line. A solution-focused, comprehensive approach building on the components but holistically looking beyond just the compressor room is essential to lowering the life cycle cost.
Cheers to our food and beverage sector
The food and beverage sector must contend with increasingly demanding regulatory challenges regarding quality, safety and energy efficiency while addressing the need to feed a growing population sustainably. Given that compressed air is often referred to as the ‘fifth utility’ in acknowledgement of its vital role in manufacturing, the compressed air industry must continually innovate so as to support food and beverage operations in meeting these challenges. With the advance of energy efficient oil-free compressed air, this technology is set to grow in relevance not just for the food and beverage industry but for all applications. Oil-free air will become more prevalent supported by design initiatives to further improve cost and efficiency, data will serve as a key enabler and with this the evolution of change will speed up delivering ever increasing savings and improvements for this vital energy source in manufacturing.
-
PPMA 2025
23 September, 2025, 9:30 - 25 September, 2025, 16:00
NEC, Birmingham UK -
Advanced Engineering Show 2025
29 October, 2025, 9:00 - 30 October, 2025, 16:00
NEC, Birmingham UK