‘Fit and Forget’ actuators provide low maintenance solution for bread manufacturing
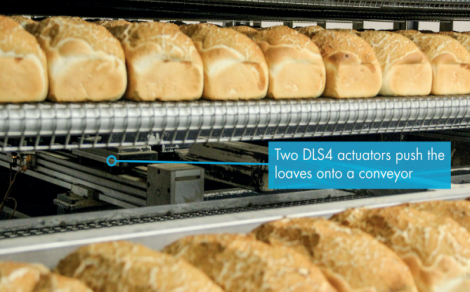
Another advantage with Hepco’s DLS4s is that they can be specified to a bespoke length to the nearest mm, up to8m as standard. This offers customers greater flexibility as they can specify the stroke length to suit the production line, rather than having to design around a standard stroke length. This was an advantage for David Wood Foods as they could easily have variable stroke lengths to suit the different processes the DLS4s are used for. Hepco’s DLS modules can also be supplied as joined sets to fulfil longer stroke requirements.
After the loaves have baked in the oven, they are transported to the cooler where they spend 2 hours rotating on a cooling rack. Cooling is a key part of the bread manufacturing process to prevent the bottom crust becoming moist and soggy. David Wood Foods has approximately 9kg of loaves in the cooler at one time. Working in parallel with a single motor and attached to a pusher arm, one set of DLS4s push 22 loaves onto the rack, while the other set of actuators push the loaves from the rack onto the conveyor to get transported to slicing and packaging.
Breadcrumbs are a recipe for disaster
As with all food industry applications, the resulting breadcrumbs and dust at David Wood Foods creates a hostile, challenging environment. If particles of dirt and debris find their way beyond the seals of any linear motion component, or if they become damaged, the system will become jammed and motion will be impeded.
This can result in catastrophic failure – meaning excessive downtime, and a complete system change. DLS4, however, is ideally suited to this harsh environmentthanks to its V guide system that functions on the basis of tight geometrical control over matching slide and bearing V’s. In turn this provides a wiping action that expels debris, keeping machines running and reliable. This self-cleaning action eliminates contamination of the slide – a key benefit for David Wood Foods working with extensive breadcrumbs.
As small, but central parts of an enormous production system, low maintenance is a core requirement of these actuators. If one part of the system goes down, the entire production line is affected. With a high throughput of 420k loaves a week, any unplanned maintenance is going to have a big impact.
A big advantage of Hepco’s V guide systems is claimed to be that they have long re-lubrication intervals. Saving valuable downtime and cost, Hepco’s cap seals need re-lubricating every 1000km, compared with every 100-150km with ball rails.
-
PPMA 2025
23 September, 2025, 9:30 - 25 September, 2025, 16:00
NEC, Birmingham UK -
Advanced Engineering Show 2025
29 October, 2025, 9:00 - 30 October, 2025, 16:00
NEC, Birmingham UK