- Home » Editorial » Hydraulics
The case for aluminium
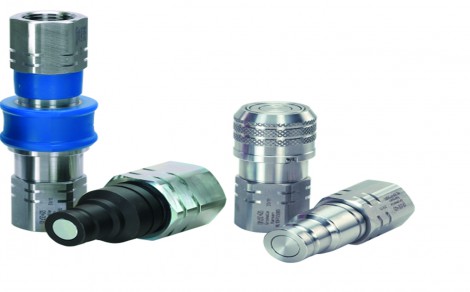
Leakage
Leaks are a common pain point for users of electrical systems that rely on liquid cooling. Due to their lower resistance to chemical attack from water-glycol cooling agents, users of thermoplastics couplings can sometimes experience leaks. Moreover, any leaked agent can prove difficult to clean, an activity that frequently leads to prolonged system stoppages.
To combat the situation, well-specified aluminium couplings offer a number of defence mechanisms against leaks. For instance, specifiers should look for couplings that provide flat-face, non-spill functionality (dry break with no liquid loss), which makes them particularly suitable for use in electrical environments. This functionality reduces the risk of technical failure and safety concerns, promoting higher effectivity in the field.
Seal selection
Another factor that influences leakage resistance is selecting the optimum seal. Here, EPDM seals are known to provide high levels of water-glycol compatibility. However, engineers should look out for coupling suppliers able to provide a host of different seal compounds, not simply EPDM alone.
The driver behind this issue is the requirement for many manufacturers to build several cooling system types, in a multitude of different formats. Here, customers will benefit from utilising a single source to maximise production efficiency, with seals able to handle different cooling agents as liquids or gases.
-
SMART Manufacturing & Engineering Week
04 - 05 June, 2025
NEC, Birmingham UK -
PPMA 2025
23 September, 2025, 9:30 - 25 September, 2025, 16:00
NEC, Birmingham UK -
Advanced Engineering Show 2025
29 October, 2025, 9:00 - 30 October, 2025, 16:00
NEC, Birmingham UK