Poor education and advice must not let down tomorrow’s engineers
It may not come as a surprise to learn that the parents of thousands of talented teens offer their full support in order for their young ones to have the best opportunity of becoming the UK’s future engineering talent. Indeed, according to new research announced to mark the start of the recent Tomorrow’s Engineers Week, three quarters of parents would recommend a career in engineering to their children. Moreover, nearly half (47 per cent) of secondary school children would consider a career in engineering, with 29 per cent of them being girls. However, it would appear that many young people lack the support in schools needed to fulfil their career ambitions, and only a third (34 per cent) say they know what to do next in order to become an engineer. Disappointingly, schools may not have the information needed to support the engineering ambitions of their students. More than half (56 per cent) of GCSE science, technology, engineering and maths (STEM) teachers surveyed have been asked for advice about engineering careers by their pupils in the last year, yet only a third (36 per cent) felt confident giving such advice. The findings reveal further disparities between teacher attitudes and pupil ambitions. Some 42 per cent of teachers believe pay is the most important factor to pupils when making career choices, when in fact only 15 per cent of pupils cite pay as most important. Choosing a career in something that they are interested in is the biggest influence for teens’ career choices (42 per cent), and parents agree (24 per cent). In a separate study of young engineers under 30 by EngineeringUK, a quarter (23 per cent) of those surveyed said they didn’t consider engineering as a possible career choice when they were at school or college and 15 per cent were discouraged by a teacher. Some 42 per cent of those that didn’t consider an engineering career would have changed their mind if they had received better careers advice, information or inspiration and 21 per cent if they had known what engineering careers involve. Paul Jackson, chief executive of EngineeringUK, recently stressed that engineering makes a significant contribution to UK GDP growth and engineering companies will have over 2.5 million job openings between 2012 and 2022 across a diverse range of disciplines. “We’re delighted to see that parents are so supportive of their children’s engineering ambitions at a time when their talents are much-needed; however, the findings reveal a worrying lack of school support for young people,” he said, adding that EngineeringUK urges schools to use the Tomorrow’s Engineers careers resources and website to inspire their students. The Tomorrow’s Engineers Week research showed that team work, working in a creative or inventive environment and bringing new ideas to life are what young engineers enjoy most about their job. Three quarters (76 per cent) of then felt positive about how quickly and how far they will progress in their careers. Two-fifths (41 per cent) enjoyed a pay rise within the first year of employment and 19 per cent got a promotion or increased responsibilities within 6 to 12 months of starting. Leading the industry charge is Shell, which has announced a three-year investment in the Tomorrow’s Engineers schools outreach programme of over £1 million. Chairman of Shell UK, Erik Bonino, said the energy company wanted to support and inspire a new generation of world-leading engineers and scientists who will fly the flag for British innovation. “The school children of today can create the technical solutions of the future, but only if we show them the vast range of opportunities that STEM subjects and careers can offer,” he said. As Business Secretary, Vince Cable, has observantly said, whether it’s the cars we drive, the houses we live in or the clothes we wear, engineering is everywhere. This being the case, we simply cannot permit poor support at school to hinder what is potentially a vast pool of talent and ambition just waiting for the chance to grasp a successful, lifelong career – A career that can not only prove to be rewarding and enriching for the individual, but also for the rest of us through greater invention and innovation.Speculate to accumulate

British manufacturers are ramping up the amount they spend on a wider range of more sophisticated assets to determine their business strategies. This is a key finding in a new report by EEF, the manufacturers’ organisation and Lombard Asset Finance. In addition to investing an average of £1million each year on plant and machinery, the report illustrates that British firms are increasing essential and complementary investment in ‘intangibles’. These include staff training, recruitment, R&D, software and marketing in order to clinch a competitive advantage. However the survey also shows that, despite the majority of companies saying they plan to maintain or increase their expenditure on new plant and machinery in the next two years, this is only at moderate levels and, mainly to replace obsolete technology. A significant number of companies also continue to struggle to raise required levels of funding. According to EEF, raising the UK’s level of investment will be essential in tackling its longstanding position as an underperformer compared to competitors. Looking forward, one in three companies are planning to invest the same on plant and machinery over the next two years as they did in the previous two, although these spending plans are moderate in scale. Nevertheless, the EEF/Lombard report shows 70 per cent of companies plan to increase their investment in staff training and recruitment, with one in six targeting a significant increase. Furthermore, three in five companies plan to increase expenditure on marketing and branding and a similar proportion on R&D, highlighting the need for government to continue to support applied research. The increasing role of intangible investment is highlighted by the fact 60 per cent of companies plan to increase investment in three or more categories. Investment in these business priorities is becoming more important for more than half the companies in our survey, but the value of plant and machinery investment is greater for a balance of 25 per cent manufacturers. Where companies were cautious about investing, uncertainty over demand was given as a primary reason by one in three companies, with a similar number citing constraints on internal finance. One in eight companies identified the availability of external finance, the majority of whom were SMEs. While some supportive measures have been introduced, such as the extension of the R&D tax credit and temporary increase in the Annual Investment Allowance, Government could go further by putting in place the following EEF recommendations: 1. Setting out a clear vision for the economy towards 2020 and the policy and spending priorities that will achieve cross government growth objectives. 2. Increasing the diversity of the finance landscape by creating a more competitive and dynamic banking environment, especially for SMEs. 3. Ensuring the British Business Bank has a long term future and is able to invest in new and innovative funding options such as patent growth capital, mezzanine finance and those supporting supply chain expenditure. 4. Implement a consultation on the UK capital allowance regime to ensure there is a competitive and stable regime in place by 2016. 5. Maintain funding for the Technology Strategy Board in real terms over the next spending review period. 6. Increase funding for the Catapult Centres. 7. Maintain the stable and broad definition of qualifying expenditure for the R&D tax credit. Solving the problem of long-term hurdles regarding acceleration in investment growth will require concerted and continuous efforts to bring down the two main stumbling blocks to more ambitious investment plans; the need for more confidence and greater levels of funding. An individual company’s roadmap for growth is largely something that is discussed in the boardroom. However, without Government providing the right environment and incentives for appropriate levels of investment to take place, hurdles to making the most successful growth plans will remain. Government, the next move is yours. The survey was conducted between 30 April and 14 May with 173 companies responding.
Minding the gender gap (August 2014)
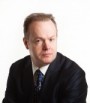
The recently announced A-level results show a welcome increase in the take-up of STEM (science, technology, engineering and mathematics) subjects, although the gender gap still remains a concern, according to EEF, the manufacturers’ organisation. Verity O’Keefe, education policy adviser at EEF, commented that, with more and more vacancies to fill, manufacturers will be breathing a sigh of relief that the take up of STEM subjects at A-level has increased for the fifth year in a row. “Without a doubt, students who have achieved top grades in these subjects have significantly boosted their employability and their chances of enjoying a successful and sustainable career,” she said. However, O’Keefe added that the overall increase in the take-up of STEM subjects disguises a mixed bag. While the EEF welcomes the fact that the number of girls studying physics has increased by 4.7 per cent year-on-year it is mindful that there is still a significant gap between the number of boys taking this subject compared with girls. Earlier in the year, a report from the Science and Technology Committee took a similar tack, arguing that universities must do more to retain women in scientific careers. Andrew Miller MP, chair of the Committee, said it was “astonishing” that women still remain under-represented at professorial levels in academia across every scientific discipline. “It’s time for universities to pull their socks up,” he insisted. In his view, some universities are doing a good job at improving working conditions for women scientists, while others are not. “The system of short-term contracts is hugely off-putting for many women scientists,” he said, adding: “More standardisation is required across the whole higher education sector and that is why we have called for Government, universities and research councils to review the academic careers structure, so that talented women, and men, can have more stable career pathways.” However, according to statistics from Cambridge Occupational Analysts (COA) earlier in 2014, campaigns to boost girls’ enthusiasm for science and engineering are beginning to bear fruit. The research showed a rise in the proportion of female pupils who are actively considering university courses in STEM subjects. Interestingly, the study shows the proportion of girls expressing an interest in civil engineering, general engineering, combined sciences, chemical engineering, mechanical engineering, electrical engineering, chemistry and biochemistry has shown a bigger increase over the past seven years than their male counterparts. COA said the figures provide additional evidence that efforts to redress the imbalance are having an impact, as suggested by the findings of a recent study gauging interest in engineering among 11-14 year-olds, commissioned by the Department for Business Innovation and Skills (BIS). The COA survey asked around 20,000 sixth formers in hundreds of schools across Britain completing Centigrade, a university choices questionnaire, which subjects they were interested in studying. Responses collected over the past seven years reveal a significant rise in interest among female pupils in the vital STEM subject areas of civil engineering, general engineering and combined sciences. The percentage of girls expressing an interest in civil engineering rose by 10 per cent between 2006/07 and 2012/13 – double the percentage rise of male pupils. General engineering was considered as a possible choice by over a fifth (22 per cent) of female respondents last year – a 16 per cent increase compared with 7 years ago. Over the same period, the proportion of boys expressing interest in the subject rose by just 5 per cent. Figures for combined sciences show a 19 per cent rise in the proportion of girls expressing enthusiasm for the subject, compared to an 11 per cent rise for sixth form boys. As EEF’s O’Keefe states, “we’re heading in the right direction”, however what is really needed is a concerted effort between Government, industry and the education sector not just to continue driving students into STEM but to also close the gender gap as tightly as possible.
Move to the next level with IT (June 2014)

Sometimes, companies become so engrossed in their daily core competencies – for example, designing, making or distributing things – that they stay a step or two removed from points of leverage that could propel them to the next level of growth. Take information technology, for example. Things have moved on at an almost overwhelming pace in the IT world over the past few years; we now have everything from cloud computing and related Software as a Service applications, social computing, big data and mobility devices that make communication and the relaying and accessibility of date so much easier and quicker whether you are inside the four walls of the warehouse and shop floor or out in the field. This technology can improve a business’s operations at so many levels; it can make a company’s activities faster, more accurate and more cost-effective; it can even improve a business’s standing in the eyes of the end customer due in some cases to marked improvements in customer service and communication concerning, for instance, the current status of an order. The CBI’s director-general John Cridland picked-up on this theme during a speech he gave at a recent technology event where he addressed an audience of 200 businesses comprising some of the UK’s best-known and most entrepreneurial companies to debate the global impact and influence of technology on business. At the #DaisyWired14 event held Heythrop Park in Oxfordshire, Cridland began by calling on the Government to give more help to growing businesses, saying that mid-market companies have often been overlooked by Government policy in favour of small businesses, even though they were the true engines of future economic growth in the UK. He then called on the entrepreneurial community to take advantage of the ubiquity of technology available to deliver a steady growth period. “Some businesses, with a turnover of £100 million to 200 million, have the potential for gazelle-like growth and could be worth £500 million in about five years’ time,” he said. “They are our true national champions – but we don’t have enough of these companies making that growth spurt in Britain. We need to concentrate on nurturing the £20 million, £40 million or £100 million turnover businesses so that they become the future national champions we can be proud of.” Cridland continued: “We cut off the support for businesses when they get to around £10 million turnover, but why are we doing that? We need to focus on this ‘forgotten army’ of entrepreneurs and help them make that progression. This medium sized group makes up less than 10,000 of the 3 million businesses of the UK but it is worth 23 per cent of the UK economy.” The director-general went on to draw a contrast with Germany, which he said had managed to support the continued growth of a much larger number of mid-size businesses, contributing significantly to real strengths in its economy. “All industries have the potential, particularly in the exports market, to make this decade the UK’s, just as the previous one belonged to Germany,” he remarked. “We need to nurture these companies with capital and management systems to help them break into the markets around the world which want to buy our products and services, but are not particularly easy to get into.” Cridland also called for the term SME to disappear, claiming that it now describes an obsolete concept. Small businesses and growing businesses that have become medium-sized businesses have different policy requirements. By taking a leaf or two from the German business support model, and by harnessing the huge potential offered by the types of modern information technology solutions cited above, many UK businesses have a very real opportunity to grow into the future national champions Cridland speaks of. Taking a little time out to survey the types of IT technology currently available could reap dividends you never know were possible. Happy shopping.
The right people (October 2013)
For any business, it is important to have all the components of a business and operational infrastructure in place for things to run smoothly and for customers to continue knocking on the door. Systems, processes and strategies of various kinds are naturally of vital importance to any company; but, of course, it is people that make these assets work. Therefore, the end game would be to ensure not only the retention of existing talented and motivated staff at all levels and within all roles, but also to sleep soundly in the knowledge that, when new personnel are required, this is going to be a fairly smooth process. However, as many readers of this journal will be all too aware, things are not quite that straightforward. New analysis of the engineering sector in both the UK and Germany has suggested that the UK must copy Germany’s recruitment approach in order not only to alleviate the current people crisis, but also to prevent further talent shortages. According to the research, which was carried out by specialist technology recruiter European Recruitment, the strategies are: • Adopting a long-term talent attraction strategy: Unlike the UK, Germany’s engineering sector has historically taken a long-term approach to its talent acquisition strategies. According to the research, the UK must forget its short-term policy of only taking action to fill skills gaps when they present themselves. • Not adopting a ‘boom or bust’ approach to recruitment: What appears to have worked well for German engineering firms is their commitment to hire in times of both austerity and prosperity. The UK must move towards this or continue to face a people crisis. • Equipping employees not only with technical skills, but also commercial acumen: Educational institutions play a pivotal role in developing the commercial skills of Germany’s workforce. ESMT European School of Management and Technology in Berlin, for example, has recently launched a Master’s in Management aimed at providing graduates with, not only the technical skills they require for their job, but also business acumen and international orientation. Students are also offered an internship as part of the course to secure on the job training. UK universities should follow suit. • Develop and maintain a strong Employee Value Proposition (EVP): Germany’s Siemens, for example, has spent decades devising a strong EVP not only to attract staff, but also to retain them on a long-term basis. By training its people the ‘Siemens way’, and offering strong development opportunities, the company has some of the best talent in the engineering space. European Recruitment’s managing director, David Wicks, has commented that the analysis of both engineering sectors clearly shows UK companies and education establishments need to mirror the strategies that have been prevalent in Germany for so many decades. “The UK education system is home to many talented STEM professionals,” he said, “however for too long it has got talent acquisition strategies wrong.” So, in order to avoid the sight of gifted people packing their bags for foreign climes, more attention needs to be given to the career packages many UK firms have to offer, together with increased levels of motivation that must also come into play. Let’s get the wheels in motion before things get any worse.Honing the relationship (November 2013)
Businesses in the UK may largely be focused on providing their goods and services on time, to the right specification and to the right standards. And this ‘focus and get on with it’ attitude seems to be paying off, with encouraging economic signals peppering the business press over recent weeks. However, home-grown firms, while being ‘in the zone’ concerning their core competencies, are far from complacent when it comes to the European Union, and the role they consider UK plc should play within it. While it appears that most businesses want to remain in the EU, they also want specific powers transferred back to Westminster. The British Chambers of Commerce’s (BCC’s) EU Business Barometer Q3 2013, which recently gathered responses from more than 3200 businesses of all sizes and within all sectors across the UK, tested five scenarios for Britain’s future relationship with the EU. Companies were asked to give their view on the potential impact of each scenario on Britain’s business and economic prospects. The results showed that businesses want more decisions made in the UK. More than half (57 per cent) of respondents believe that remaining in the EU while transferring specific powers back to Westminster would positively impact the UK’s business and economic prospects. These have previously included health & safety law, and employment law. Also, firms feel that fully withdrawing from EU membership would harm UK business interests. A majority (58 per cent) of responding firms believe that leaving the EU would damage the UK’s business and economic prospects. This is up from the 53.6 per cent seen in Q2. However, further integration is also viewed poorly. Only 7.7 per cent of businesses feel that it would benefit the UK if there was no change to the current relationship, while a plurality (41 per cent) believe that it would hinder the UK’s economic prospects. John Longworth, director general of the BCC, commented that British businesses continue to remain pragmatic in the face of ever-escalating confusion from politicians and the media over Europe. “The majority of UK firms are determined to see a revamped relationship between the UK and the rest of the European Union, with more powers exercised from Westminster rather than Brussels,” he said. For the quiet majority of companies, the status quo is simply not an option, believes Longworth. Nor, in his view, are the increasingly shrill noises from the hard-line pro- and anti-lobbies. “Ministers must pursue reform and renegotiation as a priority,” he remarked, “and ensure that a firm timetable is in place for renegotiation and for any referendum to follow.” For all the public bluster, Longworth maintains that the BCC survey shows that business continues to support the Prime Minister's objective of a renegotiated settlement with safeguards for the future and a reformed Europe. For this to be successful, he believes the European Union must believe that the UK is serious in its desire for change. “The Prime Minister should be given the support, time, space and patience required to negotiate a credible deal in Britain’s national interest,” said Longworth. But within this context of any proposed changes, clarity should always be sacrosanct. It is largely behind a backdrop of greater lucidity that UK firms would be in a better position to think about how they can develop their business – not only in terms of continuing to satisfy, and expand within, UK/European markets, but also further afield; for example, into the BRIC countries and beyond. As Horace Walpole once wrote: “When people will not weed their own minds, they are apt to be overrun by nettles.”Seeing red (January 2014)
As most businesses know only too well, their primary focus has to be on providing the best possible service or products for end customers. In so doing, there is of course is a greater likelihood that customers will continue to knock on the door over the long term, confident in the knowledge that the efficiencies they have come to associate with their provider of choice will continue to impress for years to come. And through this remaining a mutually beneficial supplier-customer relationship over the long haul solutions or service providers stand the best chance of remaining profitable while also protecting and even enhancing their brand image. However, there can be issues that consistently and incessantly take management’s eye off this fundamental matter of importance. Several are often referenced in this journal – for example, all matters concerning regulations and standards (see our Annual Boardroom Report beginning on page 29 for more on this topic), part of which involves negotiating the reams of legal documentation a firm is expected to keep abreast of on a regular basis. This, I would stick my neck out and say, can often not only prove to be a rather vexing and time-absorbing exercise for just about every company in the UK but also one that can endanger that all-important level of concentration needed to keep a company operating effectively. Government is often blamed for this onerous overkill concerning many things ‘red tape’-related, however it would appear that the current Coalition is about to give a considerable level of its attention to this very issue, recognising much of it to be, as Prime Minister David Cameron recently described it, “crazy”. Speaking at the Federation of Small Businesses (FSB) conference, he said the coalition intends to scrap or alter more than 3000 regulations from the "serious to the ridiculous". The Prime Minister added that 80,000 documents of environmental guidance will be substantially reduced; this includes some 380 pages on waste management and 286 pages of regulations on hedgerow maintenance. Approximately 100 house-building standards will also be reduced to fewer than 10. David Cameron commented that the current Coalition will be the first Government in modern history to reduce the overall burden of red tape, saving in excess of £850 million per annum. He continued: “We will scrap over-zealous rules which dictate how to use a ladder at work or what no-smoking signs must look like…We've changed the law so that businesses are no longer automatically liable for an accident that isn't their fault…And the new Deregulation Bill will exempt one million self-employed people from health & safety law altogether.” Reassuringly for UK firms, especially it would appear for SMEs, the Prime Minister went on to say he recognised that the future of Britain's economy depends on Britain's small businesses – “on those with the courage to strike out and start their own thing, who work all hours to succeed, who through love, sweat and tears make their business grow”. He continued: “We need you to keep on creating good private sector jobs, so that more people can earn a living for their families and have financial security for the future.” With such emphasis on red tape reduction, and in light of what the Coalition has already achieved in some quarters with regard to reducing the legislative burden on UK business, this sounds promising indeed. As Mike Cherry, the FSB’s national policy chairman, said at the conference, “…small firms are central to the UK's economic recovery. Having support from the Prime Minister and policymakers from all parties is critical to ensuring small business issues are front and centre of the economic debate around rebuilding and rebalancing our economy." Let’s hope red tape doesn’t get in the way of the Government delivering on its promises.Early start (March 2014)
The rationale behind apprenticeship schemes makes sound sense from so many different vantage points. On the one hand, it’s good for companies who want to ensure they have the right skill sets executed, in part, by a young, highly motivated and enthusiastic workforce, and to nurture this new talent early on in order to ensure as best as possible that the individual concerned will feel a valued part of the business, become attached to its business values and ethos of employee support and therefore want to stay around for the long haul. Apprenticeships are also good for the UK economy in general. After all, with an increasing need for stronger engineering skills to bolster UK manufacturing and engineering both at home and in terms of business ventures oversees, the need for an enthused young workforce is the only sure way of boosting our reputation for engineering excellence globally over the longer term. This journal has often written in encouraging terms about the value of apprenticeships in the world of engineering, even when it sometimes felt a little as if we were swimming upstream. However, some very positive news comes in the form of an announcement by the Institution of Engineering and Technology (IET) that more than double the number of young people are now choosing engineering apprenticeships as degree courses. Figures from the Skills Funding Agency show that in 2012/13, 66,410 young people started an apprenticeship in engineering and manufacturing technologies, more than double the 27,155 young people accepted onto engineering higher education courses in 2013, according to UCAS figures. Overall, in 2012/13, there were 510,200 apprenticeship starts compared to 495,595 accepted places for degree courses in 2013. Nigel Whitehead, BAE Systems’ group managing director, programmes & support, has recently commented that apprenticeship programmes create a pipeline of exceptionally talented young engineers. “In tough economic times it is even more important that businesses plan for the long term and continue to invest in skills and developing talent in the workplace,” he remarked. More good news comes from the EEF, the manufacturers’ organisation, which points out that UK manufacturing and engineering companies are becoming more dependent on recruitment through apprenticeships to bring young, fresh talent into the sector. The EEF has found that six in ten UK manufacturers have taken on an engineering and manufacturing apprentice in the past 12 months or so. Looking ahead to the next 12 months, the picture is even more encouraging, with over two thirds of manufacturers planning to recruit engineering and manufacturing apprentices into their companies. These findings support previous research conducted by EEF, which showed a growing need within the sector for R&D, design, technical, project management and technician skills. This is primarily due to manufacturers’ strategic outlook to develop new markets, launch new products and new services, and introduce new processes – all of which can only be done with the right workforce. With three-quarters of manufacturers saying they generally recruit apprentices aged between 16 and 18, companies are clearly seeing apprenticeships as a way to boost the pipeline of talent into the industry. These latest research findings marked the start of National Apprenticeship Week, which took place between 3 and 7 March. Now in its seventh year, the week is all about raising the profile of the importance of apprenticeships to the UK economy. Statistics from The Data Service further highlight the importance of apprenticeships within the manufacturing sector, with 66,410 young people beginning an Engineering and Manufacturing Technologies Apprenticeship in 2012/13. This represents 13 per cent of all apprenticeships starts. It’s a delight to report such highly encouraging news and these latest findings bode very well for the continued economic wellbeing both of UK Plc in general as well as the manufacturing and engineering industry’s continuing growth and development. Long may this healthy trend continue.Something in the air (April 2014)
There seems to be an almost palpable feeling of optimism within business and industry at the moment. Speaking with visitors and exhibitors at DFA Media’s co-located exhibitions Fluid Power & Systems, Air-Tech, Drives & Controls, Plant and Asset Management and European Offshore & Energy at Birmingham’s NEC earlier this month, this buoyant mood certainly came to the fore. Indeed, it was the organiser’s most successful event yet, with an official attendance figure of 12,793. This was an increase of nearly 15 per cent on 2012 (for a more detailed review of Fluid Power & Systems and Air-Tech 2014, see pages 38 to 46 in this issue). Recruitment specialist Reed has similarly good tidings to share. Increasing job opportunities and job security, combined with an optimistic outlook for the economy, is giving more than a third (37 per cent) of engineers the confidence to search for new jobs, it claims. The new Reed Engineering Salary Guide and Market Insight 2014 and Market Insight Report 2014 canvassed the attitudes of around 2500 workers and employers working in a variety of industry sectors and job levels. It found a largely happy workforce, with eight out of ten (87 per cent) workers in engineering firms feeling secure or very secure in their roles, up 13 per cent on 2012, with nearly seven in 10 (69 per cent) satisfied in their current role. However, with more than a third of workers expected to be looking for a new role within a year, two thirds (62 per cent) of employers are concerned about losing talented individuals from their organisation in this candidate-driven market. The research also highlighted a shortage of skills in the engineering sector, with more than a third (38 per cent) of engineering firms saying they have a skills gap in their organisation and 89 per cent saying this gap is having a negative impact on their business. To resolve this, 46 per cent of engineering firms are investing in training, and 50 per cent are promoting internally. Mark Blay, UK senior divisional director at Reed Engineering, made the point that UK industry has enjoyed a strong start to the year, with CBI figures showing the fastest rate of growth in new orders since 2011. “We’re seeing a burgeoning pipeline of job opportunities across all areas of industry, with predictions showing that between now and 2020, UK industry will need 830,000 new Science, Engineering and Technology (SET) Professionals and 450,000 new SET Technicians,” he remarked. Blay added that Reed is finding there is a shortage of qualified candidates in the engineering sector, and across all areas of industry there is evidence that demand for graduate engineers is outstripping supply. “With this shortfall of skilled candidates, most employers will have to take a close look at how they present themselves to the labour market to make sure they stand out and so the jobseeker chooses them,” he said. The Reed Engineering Salary Guide and Market Insight 2014 and Market Insight 2014 report can be obtained by visiting www.reedglobal.com This research was compiled using the results of the Reed 2014 Salary and Market Insight and Talent Management reports, conducted with a representative sample of 2500 employers and employees, as well as data from reed.co.uk’s monthly Job Index. When more positive economic days arrive it becomes apparent just how critical it is to encourage training and education at all levels within the engineering sphere, as well as in all others. In this regard it’s encouraging to know that almost half of engineering firms are investing in training, and half are actively promoting personnel with their organisation; which can only be good for staff morale. When qualified people are hard to come by in more bullish times many companies risk finding it a challenge to achieve their true business potential, and this naturally can have a negative knock-on effect for UK Plc. Let’s all continue to fly the flag for training and education wherever opportunities arise.
-
Smart Manufacturing & Engineering Week
05 - 06 June, 2024
NEC, Birmingham -
HILLHEAD 2024
25 June, 2024, 9:00 - 27 June, 2024, 16:00
Hillhead Quarry, Buxton, Derbyshire UK