Pushing the limits, preventing problems
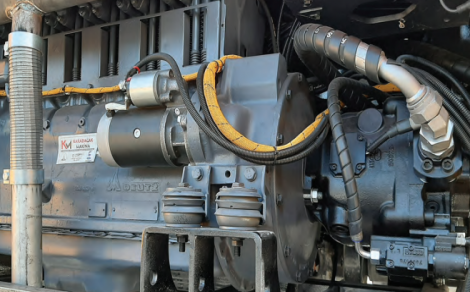
Electrification isn’t just a matter of switching out the diesel engine for an electric motor. It requires a thorough review of connected systems – in particular the hydraulic system. Using the same components in electric machines as those used in conventional machines often requires more battery power or a larger electric motor. H&P reports.
Original equipment manufacturers (OEMs) have quickly discovered the need to rethink efficiency and productivity when electrifying machines. MPG Makine Prodüksiyon Grubu learned this firsthand when designing a truck-mounted electric crane for one of its customers. The Konya, Türkiye-based OEM produces truck-mounted hydraulic cranes with folding and telescopic booms as well as aerial work platforms and tree transplanter machines. MPG prides itself on high quality and advanced technology, a result of the continuous system development studies the company undertakes to produce more capable products and introduce innovative machines to the market.
A stalling problem
One of MPG’s Netherlands-based customers requested an electric truck-mounted crane. The truck’s drivetrain was to remain diesel-powered, while the crane structure would be powered by an electric motor connected to grid electricity indoors and to a generator outdoors. The customer preferred not to use the truck’s diesel engine to power the crane, even for outdoor work, due to increasing maintenance costs.
MPG quickly got to work, conducting a literature review plus field and market research on electrical drive technology for the crane. The project team selected the electric motor and driver by making necessary power requirement calculations and designing the electrical and hydraulic circuit diagrams, then proceeded to testing. That’s when the challenge began.
Veysel Alver, general manager, MPG, described the issue: “To make the machine in the simplest way, we designed it with a 3-phase asynchronous electric motor. When we did our tests with the piston pump we use in existing machines, we could not achieve the performance we wanted, and we also experienced electric motor stalling problems. In this case, we also needed a soft starter and inverter for the electric motor.”
As with hydraulic pumps connected to diesel engines, pumps connected to electric motors can induce stalling conditions when the pump reaches maximum flow and pressure if there is no controlled limit for torque. Stalling an engine or electric motor results in lost productivity and operator frustration.
One potential solution to this problem is increasing the size of the motor, which MPG wanted to avoid as it would mean higher costs and a larger space requirement. Based on their studies, MPG engineers knew a torque-limiting pump could help.
Electronic torque limiting to the rescue
Compared to a standard pressure-compensated load-sensing (PCLS) pump, a hydraulic pump with electronic torque-limiting (ETL) control is a highly featured component ideal for machines with electronic control architectures. ETL pumps feature an electronic controller, angle sensor, and electric proportional relief valve, which together enable active control of how much power or torque the pump is consuming. Software controls the system and the tuning of the pump.
Electronic torque-limiting controls are either reactive or proactive. Reactive ETL identifies changes in the system, such as droop of the engine or reduction in shaft speed of the electric motor and then makes an adjustment to compensate. Proactive ETL control systems are preprogrammed with the actual torque or power curve of the prime mover. As speed or other conditions vary, ETL proactively sets itself for that condition.
The benefit of proactive ETL is faster-responding control. In fact, OEMs can be more aggressive with oversizing the pump because it’s able to capture more of the operating envelope than a slower-reacting solution. Adding more flow within the same boundaries of the duty cycle is beneficial because it enables the machine to move faster or undertake more simultaneous movements, thereby boosting productivity.
Mechanical torque controls are also available. These provide some of the power management functionality that ETL provides, with some compromises. There are certain performance areas of the map these solutions won’t be able to cover.
Testing reveals redundancies
MPG tested several of the torque control solutions on the market. “We tried a hydraulic torque-controlled pump, but it was difficult to make the torque-limiting adjustment manually,” Alver said. “Some torque-controlled pumps did not also allow adjustments other than the factory setting.”
MPG then tested the Danfoss Series 45 pump with electronic torque limiting. The pump proactively and automatically maximizes system pressure in milliseconds for the available torque while preventing stalls. The speed-torque graph of the engine or motor to which the pump is connected is loaded into the controller of the ETL system. The PLUS+1 GUIDE software modulates the pump’s control for a given engine speed according to the available torque.
Based on system requirements and sizing, a 130cc Series 45 ETL pump was selected, along with an MC012-112 controller. Danfoss quickly provided a prototype and helped MPG carry out system testing. Through the testing, MPG determined that they didn’t need to upsize the motor and they could eliminate several components of the system.
Alver explained: “We used a Series 45 ETL pump and we eliminated the electric motor stalling problem. We did not need to use a soft starter and inverter, and we could easily adjust the desired optimum torque value thanks to the PLUS+1 software.”
One pump fits all
For MPG’s truck-mounted crane, the Danfoss Series 45 ETL pump increased productivity by eliminating stalling, reduced costs by eliminating the need for a larger motor and driver as well as other components, and delivered efficiency improvements of 15% in comparison to a standard PCLS pump.
Alver said: “With the machines we produce with ETL pumps, our customers can push their limits without any problems, and we can offer quick and easy solutions to any system change requests thanks to PLUS+1 software. The key advantage here is flexibility and ease of implementation.”
The Danfoss Series 45 ETL pump can be applied in any existing PCLS system with or without existing power management functionality. It can be a drop-in replacement for any mechanical torque control pump. Since machine adjustments are made with software, there is no need to change pump hardware to adjust the torque-limiting settings. One ETL pump can cover the torque range of almost any engine or electric motor, eliminating the need to carry multiple part numbers for different torque settings.
Alver added: “Thanks to the Series 45 ETL pump, we are able to meet the different demands of our customers, not only electrification.
“Meeting these demands could have been more difficult and challenging for us before, but now we can meet these demands quickly. For example, some of our customers want to use an external diesel engine for the crane structure, and often the performance and torque curves of these engines can be different. Thanks to the Series 45 ETL pump, we can use our diesel engine with the highest performance by determining our torque limits via PLUS+1 for each diesel engine.”
Alver concluded: “Our customers are really happy with the performance of the machine, the flexibility, and innovations we provide.”
https://www.linkedin.com/company/mpgcomtr/
-
PPMA 2025
23 September, 2025, 9:30 - 25 September, 2025, 16:00
NEC, Birmingham UK -
Advanced Engineering Show 2025
29 October, 2025, 9:00 - 30 October, 2025, 16:00
NEC, Birmingham UK