Energy efficiency: The first step to decarbonising construction
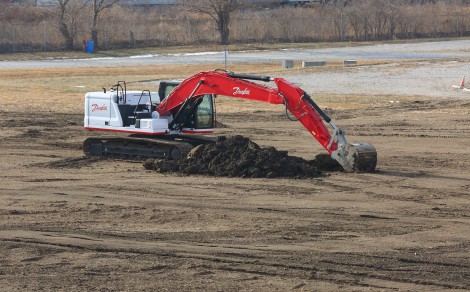
More than 50% of the world’s population lives in cities today – a number expected to increase to almost 70% by 2050 (1). As the global population continues to soar, construction of new cities and the expansion of existing cities will be required. In fact, the International Energy Agency estimates that global built floor area will increase by around 20% by the year 2030. Domenico Traverso, President, Editron & Incubation Divisions, Danfoss Power Solutions, explains further.
As we build new homes, schools, shopping centres, utilities, and infrastructure to support the growing population, we need to be cognizant of carbon emissions. Materials and construction of buildings currently account for approximately 11% of global emissions (2) . Construction machinery emits around 400 megatons of CO2 annually (3) – equivalent to the emissions from international aviation (4) – with excavators accounting for 50% of all CO2 emissions created by the construction industry (5).
We certainly don’t want to – and can’t – rein in construction. After all, it is central to economic and social development around the world. In the U.K., construction is responsible for one in every 20 jobs and contributes to 6% of GDP. In the EU, the sector provides 18 million direct jobs and contributes to about 9% of the EU’s GDP (6).
But as the scale of global construction activity increases in the decades to come, we must find a way to reduce emissions to reach the goals of the Paris Agreement and combat climate change. We must act now to build the new cities of tomorrow without relying on the building practices of yesterday. Decarbonizing off-highway machines such as excavators will play a critical role.
The future is electric
Electrification holds the largest CO2 mitigation potential for construction machinery, while delivering significant environmental, health, and economic benefits. Already we are seeing a lot of progress from manufacturers as they look to electrify their vehicles, especially smaller machines that often work in city-centre locations. We believe full electrification will come to many forms of construction equipment sooner or later.
However, some challenges need to be overcome if we are to make progress in the decarbonization of construction machinery. At first glance, it may seem simple to follow the same path as passenger cars: make construction machinery battery-electric and charge them with energy derived from renewable sources. This is, of course, easier said than done.
Compared to passenger cars, large machines such as excavators need to work much harder and for much longer between charges, which means they need extremely large batteries to match the productivity of their diesel equivalents. As a result, fully electric excavators consume a lot of resources for the battery and are expensive to buy, so the total cost of ownership over their lifetime can exceed diesel machines by a significant margin.
More investment is also needed in providing infrastructure for the electrification of construction sites. Not all work sites have enough charging energy to support a fleet of electrically powered excavators. Those sites that do have adequate electrical power are often very big, such as quarries, and require battery-swapping in the field at the beginning and end of every shift. Given that batteries weigh tons, this poses operational challenges.
While the world is rapidly scaling up much-needed renewable energy sources, we do not have unlimited green energy in the grid. The amount of additional green energy needed for electrifying the excavator fleet is not trivial: a rough estimate says that if all the world’s excavators were electric, they would consume as much energy as is generated by all the world’s offshore wind turbines today (7).
Despite these challenges, the industry is already pushing toward electrification. Today, small electric machines up to 3 tons exist and often work in city-centre locations. However, to make a substantial impact on CO2 emissions in the sector, solutions for larger machines over 10 tons are needed. These machines account for only 56% of units sold but contribute 92% of CO2 emissions (8).
Boost productivity and slash emissions with energy efficiency
Today’s excavator systems are only 30% efficient, meaning that 70% of the energy the engine produces is wasted instead of helping the excavator perform useful work. The key to reducing the footprint of these machines is to implement energy-efficient technologies that can immediately reduce diesel use and at the same time address some of the challenges for electrification.
Electrification is not a question of “all or nothing.” For some vehicles that cannot yet be fully electrified, it is possible to downsize the diesel engine and electrify critical components of the machine, creating a significant benefit from the increased efficiency of an electric system.
Improving system efficiency reduces the size – and therefore the cost – of batteries and electric drive motors needed to power the machines. It also reduces the amount of charging power as well as the amount of renewable energy generation required. This lowers the capital and operating costs of these vehicles, thereby accelerating market adoption. Ultimately, this means combining the most efficient technologies of today and tomorrow with the older machines of the past to reduce energy demand. Until full electrification can be achieved, this combination is the best and most practical solution available, and the results are impressive.
We can improve a machine’s energy efficiency in three ways. The first is by reducing idle losses with variable displacement pumps, digital displacement, and decentralised drives. Machine usage data available through telematics can also be used to advise optimisation opportunities. The second way to improve energy efficiency is to reduce hydraulic losses with solutions such as individual metering control, direct-driven hydraulic actuators, digital hydraulics, and multi-chamber actuators. And finally, through the development of energy recovery systems, we can recycle the unused energy during operations such as boom lowering and slew deceleration.
Some of technologies that we are seeing increasingly adopted can already deliver fuel savings of between 15-30% in excavators over 15 tons while at the same time increasing the work capacity of the machines. We believe it will soon be possible to reach fuel savings of up to 50%.
Construction has a role to play in battling climate change
Major metropolitan areas are proving to be a powerful force in decarbonization by demanding zero-emission operations, including on construction sites. Until recently, low-emission construction seemed unattainable. But as regulations for greenhouse gas emissions and sound pollution have been enacted, market innovations have gained traction, paving the way for change in the construction industry. Many cities around the world are now prioritizing different ways to reduce emissions from the construction sector. However, the pace needs to increase rapidly. The good news is emissions reduction can be accelerated greatly through the continued development of innovations and adoption of efficient technologies that are already available.
Construction OEMs and contractors play a key role in building the new cities of tomorrow, but all organizations involved in the supply chain must collectively take steps to decarbonize the industry. Doing so will unlock significant environmental, health, and economic benefits. We have the solutions; now is the time for action
[1] IEA (2021). Empowering Cities for a Net Zero Future, p. 3.
[2] World Green Building Council (2019). Bringing embodied carbon upfront.
[3] IDTechEx (2022). Electric Construction Machines Vital for Greener Construction.
[4] JRC (2022). CO2 emissions of all world countries.
[5] Reuters (2023). Struggling UK economy buttressed by construction as other sectors flag.
[6] European Commission. Construction sector.
[7] Danfoss (2023). FPC2023 Danfoss, p. 12.
[8] Danfoss (2023). FPC2023 Danfoss, p. 9.
-
SMART Manufacturing & Engineering Week
04 - 05 June, 2025
NEC, Birmingham UK -
PPMA 2025
23 September, 2025, 9:30 - 25 September, 2025, 16:00
NEC, Birmingham UK -
Advanced Engineering Show 2025
29 October, 2025, 9:00 - 30 October, 2025, 16:00
NEC, Birmingham UK